Time to Go Green With Your Plate Production?
ONE OF THE smartest things an in-plant can do to reduce production time and environmental impact is to go computer-to-plate (CTP), eliminating the entire film imaging and developing stage and all of the toxic waste issues involved. The quality, speed and efficiency improvements of CTP make it an excellent business decision for almost any shop. Many have already done just that, and are now ready for the next step up: low-process/chemistry-free or no-process plates.
Going green has been a big story in the print business for the past decade, and chemistry-free plates are the next wave.
“Non-process plate technology will improve to meet the increasing demand for sustainable solutions, and we’ll reach out to a broader range of printers, including larger printers and printers outside the commercial printing arena,” notes Rich Rindo, Kodak’s director of global product management for printing plates.
Over at Presstek, John O’Rourke, director of CTP products, agrees: “Chemistry-free plate technology will continue to be the fastest-growing product category for digital plates.”
These eco-friendly plates will reduce your pollution footprint right away and further speed up your production cycle. Most are not completely process-free, but they’re close to it; they often require only a water rinse or a clean-out/gumming step, while others “develop” on-press, with the fountain solution handling the clean-out step. None of these plates need conventional developing chemistry or a regular plate processor, and so avoid many of the environmental/waste issues. Eco-plates are available in sizes from two-up to eight-up. Some manufacturers offer polyester plates, but the majority of the product offerings are metal plates.
The Technologies Used
The vast majority of eco-friendly plates are thermally imaged, and there are a couple of variations on this technology. Thermal ablation, as used in Presstek’s Anthem Pro metal plates, requires a high-power thermal laser or laser diode array that literally blasts away non-image portions of the plate coating. This approach requires an internal vacuum system to remove the debris before it settles on the optics. The plates require a simple water wash to remove any residue.
The second thermal CTP technology is called thermal coalescence, and it’s used in Agfa’s :Azura and Heidelberg Saphira Chemfree metal plates. In this approach, the high-energy thermal laser fuses ink-receptive latex microbeads into the grain of the metal sheet to form the image. The non-image area is cleaned in a post-imaging gumming step.
Another variation on the thermal technology is used in Kodak’s Thermal Direct and Fuji’s Brillia HD PRO-T plates. With them, the ink-receptive plate coating is designed to be soluble in most press fountain solutions, except where the thermal laser writes the image (making those areas non-soluble). Then the plates are developed on-press as the fountain solution removes the non-image areas of the plate’s coating as the press starts running.
There are a few non-thermal processless plate approaches, including the electrophotographic imaging used by Xanté on its Aspen plates and the processless ink-jet plate imaging use by Glunz & Jensen’s PlateWriter 4200 and its iPlate product. Each has its pros and cons worth careful investigation, especially for smaller in-plants and those doing low-to-mid-range press runs (typically up to 25,000 impressions).
Processless Violet Plates
This year the market will change. Some of the larger plate companies will be showing a brand-new category at Drupa 2008: processless violet plates. This technology offers all of the usual advantages of conventional violet plates—faster imaging, much lower power consumption, suitability for fairly long press runs (100,000+ impressions) and excellent image quality—combined with the elimination of conventional plate processing and the time, floor space and environmental issues associated with it. This technology has been in development (and rumor) for about five years, but 2008 seems to be the year it will actually come to market.
“We’ll have live demonstrations of our new Saphira ChemFree Violet plates this year at Drupa, and it should be on the shelves sometime later this year, with sizes and specifications similar to our current thermal Saphira Chemfree plates,” reveals Don Rogers, Heidelberg’s product manager for consumables. “And as we release larger presses, I think you’ll see that we’ll bring in new plate sizes down the road a bit to support them.
“The environment is a very important issue to Heidelberg and our customers, and we’ll see ongoing improvements to our existing plates and some new environmentally friendly announcements,” Rogers concludes.
Both Fujifilm and Agfa are expected to show new violet process-free plates at Drupa as well. It will be interesting to see who gets their product to market first and how they compare in specifications and pricing.
The market for thermal process-free plates will continue to be strong, given their very high image quality, regular white-light handling (violet plates require yellow-light handling) and suitability for very long press runs. But you can expect these new violet process-free plates to establish a strong market share over the next two years.IPG
The Key Players
• Agfa was one of the first companies into the processless arena, and maintains a strong market position in the category. Its :Azura thermal metal chemistry-free plates (sizes to eight-up) run on Agfa’s own platesetters and other thermal CTP systems. They’re safe for daylight handling, and only a simple cleanup stage is needed after imaging. :Azura is designed for low-to-medium press runs (up to 100,000 impressions unbaked) and resolutions up to 200 lines. Also, watch for a new faster thermal plate—the :Azura TS—and a new violet process-free plate (currently designated N92-VCF) from Agfa at Drupa, with 200-line and 125,000-impression capabilities. Agfa will release this product in the newspaper market and later for commercial print. (www.agfa.com/en/gs/products_services/all_products/azura.jsp)
• Fujifilm Graphic Systems’ Brillia HD PRO-T is also a thermally imaged processless metal plate offering image quality and durability close to Fujifilm’s conventional plates. It can be used on most thermal platesetters. Fujifilm’s upcoming Brillia HD PRO-V plate (expected at Drupa and likely for commercial release later this year) is a photopolymer violet-imaged processless plate that will allow all of the advantages of violet platesetting (faster, lower-power imaging, lower machine cost) as well as the advantages of going processor-free. (www.fujifilmgs.com/pages/ctp/143.php)
• Kodak’s entry into the processless plate market is its Thermal Direct plate (up to 200 lines/100,000 impressions), a thermally-imaged metal plate that develops on-press—no rinsing, cleaning or gumming required. It’s daylight-safe and works with most thermal 800-850nm CTP platesetters and handles press runs up to 100,000 impressions. (graphics/.kodak.com/uk/consumables/plates)
• Presstek, another early innovator in DI printing and process-free plates, offers its UV ink-compatible Anthem Pro thermal CTP processless plates, which can be imaged in most 800 - 1200 nm thermal platesetters and require only a simple water rinse after imaging. Its Freedom processless plates are designed for use on Presstek’s Vector TX52 thermal platesetter and are cleaned in a water wash built into that device. (www.presstek.com/consumables)
• Xanté uses a different approach to processless plates. The company’s electrophotographic PlateMaker 5 platesetter and Myriad 2 process-free polyester plates work together to produce up to 120 two-up press-ready plates per hour, ready to mount without any post-imaging steps required. (The device can also output on film or paper.) If you’re looking for metal plates, the Impressia CTP/GTO platesetter line and Aspen non-photosensitive processless metal plates will get the job done at up to 60 plates per hour. (www.xante.com)
• Last, but certainly not least, press giant Heidelberg offers the negative-imaging aluminum Saphira Chemfree plate, which uses thermal coalescence technology, requiring only a clean-out/gumming step. Launched just over two years ago, it’s designed to work with Heidelberg’s thermal Suprasetter platesetter line. These plates are suited for longer runs (up to 200,000 impressions, or with post baking, up to 500,000) and with UV inks. Look for an announcement from Heidelberg at Drupa regarding its upcoming Saphira Chemfree Violet plates. (www.us.heidelberg.com).
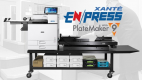




