University of Arkansas Reinvigorates its Prepress Operation

A year or so ago, things were not looking so good for the in-plant at the University of Arkansas. Though the shop had added a Xerox iGen3 in 2006, its offset operation was a little behind the times.
The in-plant still ran film on an imagesetter, and its old Iris proofer was slow and not very color accurate. As a result, it was nearly impossible to give customers the colors and the quality they wanted. Add to this the financial difficulties brought about by the recession, and it seemed like decision time was at hand for the Fayetteville-based in-plant.
“We felt like we needed to make a commitment to either fold our tent and go a different direction, or maybe see if there’s a different way to do what we do,” says Jim Hicks, interim director of the 24-employee PMC Solutions department.
So with the support of the school’s associate vice chancellor for Business Affairs, David Martinson, the in-plant put out an RFP for a new computer-to-plate system. Then fate stepped in.
On a visit to Walmart’s nearby Print & Mail Distribution Center, Bob Demmitt, a salesman for Clampitt Paper, happened to notice a nearly new Kodak Magnus 800 CTP system sitting unused in a corner. He inquired, and learned that when Walmart had added a larger press last year, it needed a larger CTP system, so it put the Kodak unit in storage after just a year of use.
“He already knew that we had put out an RFP,” remarks Hicks. So Demmitt told him about it. “It turned out it was just what we wanted.”
The two in-plants worked out a deal, and then Walmart put it on a truck and brought it over. But CTP alone wasn’t enough; the in-plant needed an accurate proofer and a whole new workflow. So Hicks put his prepress manager, Melissa Couch, in charge of writing an RFP.
As a result, the in-plant recently added Heidelberg’s Prinect workflow, getting a package designed especially for school production. This included the MetaDimension RIP, the Prinect PDF Toolbox (with Adobe Acrobat plug-ins like PDF Assistant, Trap Editor and Color Editor) and Prinect Signa Station for impositioning and sheet assembly.
“It’s astronomically better,” gushes Couch. “It’s unreal, the change in our workflow. Our in-house production time is less than half of what it used to be for most of these jobs.”
The shop also added an HP Designjet Z2100 inkjet proofer, which was color profiled to the in-plant’s five-color, 20x28˝ Komori. The shop also has a two-color, 24x36˝ Heidelberg SORD, two Hamadas and a Multi 1450.
“Heidelberg came in and spent two days with us devoted to getting a color profile written for our press, for our pressroom and our conditions,” Couch says. “The color proofing profile, to me, is the most important link.”
Now, the colors that customers see on their screens match the colors on the proof and the final product. This was evident in a recent brochure the shop printed containing colorful art images. The quality, Couch says, was noticeably better.
The new Magnus 800, an eight-up, thermal, external drum platesetter—running Heidelberg Saphira chemistry-free plates—has played a big part in stepping up the print quality. It produces cleaner dots, with less gain, Couch notes. It’s also much faster than the previous film workflow. And the press operators love the new plates, which register better and ink up quickly.
“Every single one of them has come up to me and raved about the new plates,” she says.
The new workflow even allows the shop to export imposed PDFs to the iGen3.
Couch says she was initially nervous about working with two different vendors—Kodak and Heidelberg—but she says their technical staffs worked well together.
“The process went very smoothly,” she says. “It was a relief.”
Related story: University of Arkansas Installs Xerox iGen3

Bob has served as editor of In-plant Impressions since October of 1994. Prior to that he served for three years as managing editor of Printing Impressions, a commercial printing publication. Mr. Neubauer is very active in the U.S. in-plant industry. He attends all the major in-plant conferences and has visited more than 180 in-plant operations around the world. He has given presentations to numerous in-plant groups in the U.S., Canada and Australia, including the Association of College and University Printers and the In-plant Printing and Mailing Association. He also coordinates the annual In-Print contest, co-sponsored by IPMA and In-plant Impressions.
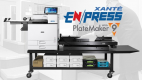




