Getting the Most Out of Coated and Uncoated Papers
Paper Selection Tips
The tedious selection of paper is crucial to the final printed piece, as it not only has to perform on press, but also on budget. When making the choice between coated and uncoated paper, consider that uncoated paper conveys a sense of fiscal and environmental responsibility. Uncoated paper produces beautiful printed results and is also comfortable. Its non-glare surface makes reading effortless and its luxurious bulk feels substantial.—Beth A. Povie, Finch Paper LLC
If you're trying to achieve an upscale-look without the cost, select a smooth, color copy paper with high brightness. Many inks and toners come out looking shiny on uncoated paper, adding to the expensive look. If looking for a sheet with a soft tactile finish (vs. the colder, harder surface of a coated sheet), textures such as bark, crepe or felt are the answer.—Andrea Alstad, Wausau Paper
Each paper has characteristics that will influence how the final product will look. For example a brighter or bluer paper will contribute to a winter scene while a warmer color paper might be better for flesh tones or food products. A brighter paper is said to give the image more contrast and the illusion of a whiter sheet of paper. The smoothness of the paper surface will affect the gloss of the paper. A lower gloss paper surface, such as a matte, satin, dull or uncoated paper, makes it easier to read type, while a higher gloss paper surface can produce sharp/contrast images with a high ink gloss that makes the image pop from the page.—Brian Fenner, NewPage
While the different types of coated paper are identified by number (#1, #2, #3 and #4), uncoated papers have names such as Offset, Opaque, or Text and Cover. The different categories reflect quality steps in brightness, opacity, formation, shade, print quality and environmental attributes.—Beth A. Povie, Finch Paper LLC
Sustainability and Paper Choice
With the green movement becoming mainstream, the softer and natural look of uncoated papers has increased in popularity. In addition to white, there are a plethora of earth-toned uncoated papers available on the market, including muted browns and greens like bamboo, weathered oak and thyme. Many uncoated papers also carry important environmental certifications such as Green Seal and Forest Stewardship Council.—Andrea Alstad, Wausau Paper
Sustainable doesn't have to mean uncoated. Contrary to popular belief, there are coated papers that are as (if not more) sustainably manufactured than some coated papers. Ask your merchant which coated papers contain the highest PCW content and which are being manufactured responsibly. Calculate your paper's impact using Mohawk's Environmental Calculator (find it at www.mohawkpaper.com).—Pam McGuire, Mohawk Fine Papers
Printing Tips
Because uncoated paper is absorbent, ink soaks into the paper and dot gain (the spreading and deformation of ink during the printing process) occurs. To allow the press operator to print at normal ink densities, open the mid-tones 20 percent and shadow areas 5 percent. This will compensate for dot spread.—Andrea Alstad, Wausau Paper
When running a long job it is to your benefit to take a handful of paper, flip it and print on it, to verify the back side of the paper will print the same as the front side. Also, look at consecutive sheets, since most paper is sheeted from multiple rolls.—Brian Fenner, NewPage
Different types of ink and the way they're applied can produce great effects on uncoated paper. When using metallic inks, the smoothest uncoated papers deliver the best results. We recommend using non-leafing metallic inks, as the metal flakes in these inks sink down and result in less rub off. We also recommend applying dull varnish or dull aqueous for additional rub protection.—Pam McGuire, Mohawk Fine Papers
Besides the visual aspect of the paper, the biggest difference between coated and uncoated paper is how they react on press. The coated paper will usually hold out the ink and fountain solution more than the uncoated paper. This would suggest the press person would need to reduce the amount of ink and fountain solution when running coated paper compared to uncoated paper if they are printing to a specific ink density.—Brian Fenner, NewPage
Not all paper will react the same on press. Changes in the amount of fountain solution, ink, or printing pressures might be necessary to achieve maximum print quality.—Brian Fenner, NewPage
That unwanted extra "spread" can be controlled to a great extent in digital prepress through the use of "curves," a set of adjustments (usually proprietary to the printer) that will accommodate for the natural dot gain caused by different types of paper, equipment and images and lead to cleaner, crisper printing.—Pam McGuire, Mohawk Fine Papers
Drying Time
Uncoated paper typically needs more drying time than coated paper. Oxidizing ink or the use of drying stimulators in the standard ink can be used as an alternative.—Andrea Alstad, Wausau Paper
Sheetfed inks dry by absorption and oxidation. Ink drying can be influenced by a combination of variables on press: ink strength, ink emulsification characteristics, fountain solution pH, the ink/water balance, the temperature of the fountain solution and the ambient air, the RH of the press room, the paper capillary action or hold out, the delivery pile height, the amount and size of the spray starch, the temperature of the delivery pile, the coverage of the form, etc. It is the compatibility of these variables that will better your chances at producing a high-quality job.—Brian Fenner, NewPage
Coated paper's influence on ink drying would be how fast the paper absorbs the vehicle of the ink, which allows the remaining portion of the ink to stay on the surface and polymerize. The coated paper selectively pulls out the vehicle of the ink through the capillary action of the paper surface. The capillary action of the paper is directly associated with the pore size and volume of the paper surface. A paper that quickly sets up the ink will be good for ink drying, but if the ink sets up too quickly it can contribute to other problems such as picking and downstream piling.—Brian Fenner, NewPage
Paper Storage Tips
To prevent your uncoated substrates from curling, keep paper in the same room as manufacturing. This will prevent moisture swings because the paper will become better acclimated to the room's temperature. Wausau Paper recommends the pressroom relative humidity be between 40 and 55 percent at a room temperature of 72° F.—Andrea Alstad, Wausau Paper
Cover the skids of paper or any open piles of paper to prevent the ambient air from changing the paper. Paper will act like a sponge, adjusting to the moisture or lack of moisture in the ambient air. Registration issues and feeding problems could occur if the paper is not covered.—Brian Fenner, NewPage
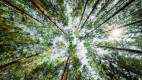


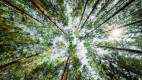
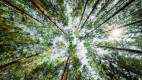
