Is there a CTP device in your future? To get the scoop on CTP, we asked the experts a few questions. Their answers will help you decide.
Sharing their expertise on computer-to-plate topics were:
• Mark Vanover
Marketing Director of Advanced Solutions, Creo Inc.
• Marc Johnson
Product Line Marketing Manager, Off-Press Products, Presstek
• Jeff Hopkins
President, basysPrint
• Stu Gallup
Director, Digital Systems Marketing and Product Planning, A.B.Dick Co.
• David Furman
Agfa Product Marketing, CTP
• Peter Vanderlaan
Product Development Manager
Electronic Imaging Hardware
Fuji Photo Film U.S.A., Graphic Systems Division
.
What advantages does a computer-to-plate device have over an imagesetter?
Mark Vanover, Creo Inc.:
The elimination of film, film chemistry and silver recovery. CTP reduces the cost of manufacturing (cost of film, chemistry, etc.) It is a more environmentally friendly solution.
CTP offers improved consistency in registration and process control from plate to plate, job to job. It brings a reduction in film used in proofing cycles. You'll have a shorter cycle from prepress to press. Last-minute corrections can occur in tighter time frames.
Marc Johnson, Presstek:
By eliminating multiple steps in their workflows, both in prepress and in the pressroom, the CTP-enabled in-plant can get its work not only plated, but on press in less time.
Much of the time saved will be the result of performing imposition digitally. Digital imposition efficiently moves files from "intake" to final output in fewer steps, eliminating not only the final plate exposure on the frame but also the need for intermediate burns and manual stripping.
In the pressroom, the savings are equally dramatic. Plates imaged digitally are in perfect register, produce a sharper dot with crisper text, and offer faster roll-ups.
Traditional chemistry costs printers in many ways: the up-front costs of the chemistry itself, disposal costs, processor maintenance time and materials. Chemistry also is a variable in the process, which can lead to increased waste.
Jeff Hopkins, basysPrint:
CTP has many advantages:
Faster makeready: Even if the customer has a full-size imagesetter, the makeready on a CTP plate is improved because there is no chance for misalignment between the plate to be imaged and the film. Customers who transition from a full-size imagesetter to CTP claim a 10 to 25 percent improvement in makereadies.
Quality: The original resolution/line screen product produced with film looks to be a step up in resolution/line screen with CTP because the image has not lost any quality or sharpness by being imaged through the film. Imaging the plate through the film produces a less sharp image because of light diffraction around and through the film as the light makes its way to the plate. Additionally, other film-related issues, such as "hot spots," are a thing of the past.
Fewer makeovers: Plates do not have to be remade because of bad stripping, mishandling in the film imaging process, or hot spots created by film.
Reduced labor: CTP eliminates the film making and handling process.
Reduced costs: The key elements for the ROI of CTP in order of payback dollar amounts are: Film and film chemistry savings, makeready improvements including press time and paper and ink, prepress labor reductions, stripping supplies, and maintenance costs for imagesetters, light frames and other film equipment.
Stu Gallup, A.B.Dick:
Advances in printing technology have either been to increase productivity or increase quality. Computer-to-plate technology allows the in-plant printer to do both.
The goal in increasing productivity is to get from concept to printed sheet as fast as possible. This is achieved by taking out the middle steps. Imagesetting adds middle steps: you have to image film, process film, strip film and burn plates. This adds extra steps, extra equipment and extra cost.
CTP allows the in-plant to go from file to imposed, press-ready plate in minutes. This reduces costs.
The other major benefit of CTP is that the image is the first generation. The laser is putting the image right on the plate, not on an intermediary, such as imagesetters do. This allows for higher-quality printing.
David Furman, Agfa:
Advantages of CTP include: Reduced cycle time due to elimination of film intermediary; better registration; faster makeready on press; and lightning fast remakes.
Peter Vanderlaan, Fuji Photo Film:
The most obvious advantage would be the elimination of film from the prepress process. While this seems reason enough to switch to CTP, other considerations must be made, such as digital workflow and a new or enhanced workflow.
It is very important that users make sure that the switch to CTP provides an acceptable ROI for them. Platesetter, digital proofer and workflow capital investments, as well as consumable usage, all need to be considered in the ROI calculation.
Users switching over to a CTP workflow can produce a new enhanced level of quality in their printed work. With the elimination of the film process, users can avoid possible registration and fit errors as well as dot gain/tonal control issues.
From workflow to digital proofing to digital plate making, CTP users will enjoy a new, streamlined digital prepress operation. With the elimination of film in the process, users simply direct the digital data to the appropriate device, i.e., platesetter, proofer, plotter or remote proofer. Additionally, when utilizing a high-speed platesetter, a plate remake (punched and ready to run on press) can be produced in about three minutes.
Thanks to the speed of the devices available to the market and the resulting simpler process, makeready times will decrease and productivity will increase.
.
What changes must in-plants make to their workflows when adding CTP?
Mark Vanover, Creo Inc.:
In most cases where a customer is currently imaging film, the change to CTP seems transparent in the workflow process, and facility modification to the electrical and air supplies are typically modest.
Marc Johnson, Presstek:
In-plants that are already outputting imposed "plate-ready" film from their drum imagesetters will find moving to CTP to be very easy; it's a simple change of the output engine. Most workflows today are capable of outputting in an industry-standard, one-bit TIFF file format.
For operations that are outputting to a smaller filmsetter, or to RC-paper, the workflow enhancements required are for digital imposition and digital proofing.
Jeff Hopkins, basysPrint:
The printer that has a full size imagesetter today has already made the digital transition and only needs to send the RIPed file to the CTP device versus the imagesetter.
The printer that has less than a full-size imagesetter should add imposition to the workflow, but utilize the existing workflow.
Stu Gallup, A.B.Dick:
The biggest change that an in-plant must go through when going to CTP is in how hard copy originals are handled. In-plant shops still have a fair amount of camera-ready art that needs to go to plate. In-plants especially have a lot of forms, letters, charts, etc. that are not digital. Handling these workflow issues can become a bottleneck if not done right.
David Furman, Agfa:
You will need storage to archive digital flats in order to access files for plate remakes. If you run an eight-up press, you will need to establish a page-based workflow; Two-up and four-up printers may need a RIP only. You may want to consider PDF if you want to run cross platform, either upstream to clients or across the organization.
Peter Vanderlaan, Fuji Photo Film:
It is advised that a user be experienced in imposition layout via an imagesetter prior to implementing a CTP workflow. Beyond that aspect, a user must also utilize a workflow that will support the CTP device and a digital proofer, as well as the color management and trapping processes. This may require implementing a new workflow or upgrading the existing in-house workflow.
What proofing options do in-plants have when they image direct to plate?
Marc Johnson, Presstek:
Proofing has changed a great deal in just the last year. While inexpensive ink-jet proofers initially were viewed as good for positional proofing, or for content, they weren't viewed as sufficient for color or contract proofing. The newest breed of ink-jet proofers is challenging that notion—and in many cases winning.
Instead of tens of thousands of dollars for a proofer, and upwards of $50 for a proof, print buyers are showing growing acceptance of proofs generated by ink-jet printers that can be purchased for well under $10,000, with a materials cost of under $8 per proof.
One of the drivers for change in proofing has been the proliferation of industry-standard ICC color management, which every major workflow system today works with. Color management allows an in-plant to fingerprint its press, ink and paper stock and match it on an ink-jet proofing system.
Proofing solutions are available now that simulate halftone dots—accurately predicting moiré that would occur on the press sheet on an inexpensive ink-jet proof.
Jeff Hopkins, basysPrint:
Certain CTP devices utilize the same file to image the conventional plate and to produce the dot proof, using the same materials. All that changes is the exposure intensity based upon the material being imaged. Just as with the Dot Proofs, blue lines can be imaged using the same file, only varying the imaging time/intensity.
Stu Gallup, A.B.Dick:
When eliminating film and going to CTP, the in-plant must also eliminate traditional film-based proofs. This is a big benefit, since traditional proofing was time consuming and decreased the shop's productivity, while increasing costs.
The main type of proofing for CTP is the ink-jet proofer. The quality that is achieved on ink-jet proofers is fantastic. At one time ink-jet proofing was looked at as inferior to traditional proofs. That is no longer the case. Especially now that you can use ICC profiles to match the press output to the ink-jet proofer output.
David Furman, Agfa:
Ink-jet digital proofing is ideal. It is low cost, high quality and high productivity. Remote proofing is an option. You can proof where the file is originated vs. within the printing environment.
Peter Vanderlaan, Fuji Photo Film:
Many proofing options are available, from wide ink-jet format for checking imposition to halftone "contract" proofers. Some proofers offer a press match quality proof with the ability to run virtually unattended. You can set up "remote" proofers for satellite locations. IPG
Computer-to-plate offers in-plants many advantages over imagesetters. The Fujifilm Saber Luxel P-9600 CTP eight-page visible light platesetter will provide 27 plates per hour at 2,400 dpi, or four plates imaged and punched ready for press in about 10 minutes.
Quick Look
• By eliminating multiple steps, platesetters allow in-plants to get work plated on the press in less time.
• Because CTP platemaking eliminates the whole film making and handling process, labor is reduced.
• With CTP, the up-front costs of the chemistry, disposal costs, processor maintenance time and materials are eliminated.
• By eliminating chemistry, CTP is a more environmentally friendly solution.
• Last-minute corrections can occur in tighter time frames with CTP.
• With CTP, plates do not have to be remade because of bad stripping, mishandling within in the film imaging process or hot spots created by film.
• Plates imaged digitally are in perfect register. CTP produces a sharper dot with crisper text.
• The total floor space required for CTP is usually smaller than the existing imagesetter and processor.
• The in-plant that has a full-size imagesetter has already made the digital transition and only needs to send the RIPed file to the CTP device versus the imagesetter. Facility modification to the electrical and air supplies are typically modest.
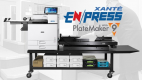




