Managing Growing Volumes at Mary Kay Inc.

"IT HIT us like a ton of bricks" recalls Keith Hopson. "We didn't know it was coming until we were flooded with work."
The sudden increase in workload came when cosmetics company Mary Kay Inc. shifted the printing and folding of "pharmaceuticals"—the inserts that accompany its skin care and cosmetics products—from outside printing suppliers to the company's in-plant facility in Carrollton, Texas. Similar to those included with many over-the-counter medications, the inserts provide specific, –detailed product usage instructions. These are included in virtually all Mary Kay products sold in Europe, where multiple languages add complexity to the mix of jobs.
Printing these is a straightforward process on the shop's two 29˝ Heidelberg presses. But folding them quickly became a bottleneck.
"It doubled or tripled our volume and we couldn't handle it with our existing folding equipment," explains Hopson, supervisor of Printing Services, which is located a short drive from Mary Kay's global headquarters in Addison, Texas. "We were sending about 100,000 pieces a month to an outside shop just to keep up."
Hopson moved some staff to different jobs and added some overtime to keep pace while waiting for a new Vijuk SAF 36 folder to arrive. Once installed, the new machine dramatically increased in-house capabilities. By eliminating the outside supplier, Hopson saw payback in just two months, while significantly improving efficiency and turnaround in the shop.
Growing Volumes
That was more than two years ago and today the 14-person shop is constantly busy. Some 50 million pharmaceuticals will be produced in 2010, exceeding the 48 million in 2008. Inserts are printed, folded to a specific size, and shipped to the manufacturing warehouse where they are packaged with the products.
All pharmaceutical printing is done on the two Heidelberg presses, capable of straight and perfecting printing. Plates for each job come from a Fuji Luxel T-6000 computer-to-plate (CTP) system running Screen Trueflow 6.0 in a PDF workflow. In addition, a small A.B.Dick press handles quick printing needs such as labels and business cards, while a Halm Jet Press prints envelopes from baronial sizes up to 10x13˝.
All folding is done on the in-plant's three Vijuk folding machines. The newest, the Vijuk SAF 36, is a six-plate folder that can handle the lighter weight paper used for the pharmaceuticals—a 35-lb. offset sheet. And the folding can be complicated. For instance, one job that was in process when Hopson was interviewed for this story required folding an 8x20˝ sheet to 8x1˝ so it would fit in a tall, skinny box. Printed two-up on one of the Heidelbergs, the job ran at 5,000 perfected sheets per hour on press. Then came folding.
"It requires a lot of folding, and that limits total output," explains Hopson. "Typical folding jobs run at about 25,000 per hour, and can reach 60,000. But on a job like this, output goes down to about 5,000 per hour. We have a single-shift operation, so with 325,000 pieces to fold, it ties up the machine for several days."
Still, Hopson's seasoned, experienced staff knows how to get the most out of the equipment. The complex setup for a job like this would take many shops an hour or more, but Hopson's team can have even complex jobs ready to run in half that time—even though folding specifications often come down to a small tolerance of 1⁄32 of an inch.
"The folding specs for each job come to us from the packaging engineers," he explains. "Then we set up the machines. Most of the jobs we see, we've seen before, so the folder operators know what they need to do to have a sheet fold correctly."
Sometimes, though, the folding specifications don't work quite right. "The size could be fine, but the sequence of the folds or scoring might leave the finished sheet feeling spongy rather than tight," says Hopson. "We have the latitude to make adjustments that make sure the quality of the folded sheet is where the company wants it to be."
Changing Workload
In recent years, the in-plant has experienced a shift in the type of work it does. The once constant flow of –one- and two-color letters and other printed communications to the company's global independent sales force was replaced by e-mail, eliminating a portion of the volume that flowed through Printing Services. Slowing things down even more, the insourcing work—all pharmaceutical folding—dropped some 75 percent in 2009 due to the economy.
With the recent opening of Mary Kay Armenia, the print shop is again faced with a new challenge of meeting the demand for its services.
"Every insert has a part number that matches its product," explains Hopson, "and that includes language. Armenian just adds to the volume. Plus, delivery is always on a tight schedule. Our due dates are tied to manufacturing and shipping schedules so the dates can't move very much. Clear communication between manufacturing, shipping and Printing Services is critical, especially when a deadline needs to shift."
Beyond the Fold
The bustling print shop isn't limited to printing and folding. Although mailing and inserting volumes have reduced due to converting to e-mail communications with the Mary Kay independent sales force, there is still a constant print and mail volume, including statements, letters, checks and the like. These are printed in the headquarters data center and driven the nine miles to Print Services for mailing. A Böwe Bell + Howell MasterMailer inserter and two Böwe Bell + Howell Mailstar inserters capable of OMR reading do the heavy lifting. The Mailstars can insert up to four pieces into an envelope. With two million Mary Kay independent beauty consultants around the world, the mailing volume remains a consistent part of the workflow depicted in the twice-weekly spreadsheet.
Because of the growing volume, many of the shop's 14 employees are cross-trained, giving Hopson the ability to realign staff to meet production demands. He sees further cross-training as a way to increase flexibility.
"We have just enough people for our volume and we're adapting to the changes and growing volumes," he reports. "And there's always something new." IPG
Related story: New Folder Helps Lead In-plant to Banner Year

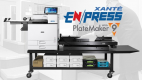




