
The following article was originally published by Printing Impressions. To read more of their content, subscribe to their newsletter, Today on PIWorld.
Across the printing spectrum, companies face the challenge of achieving acceptable — even exemplary — levels of quality. From the customer standpoint, the definition of quality is subjective, a sense that the finished piece meets the expectations agreed to, spoken about, or specified. Within the “printing” step of the broader process, much of the focus is on achieving color. For commercial printers, a key element in this quest is the paper or other substrate.
To further explore this reality, and what commercial printing operations can do to address it, four color professionals possessing in-depth knowledge of paper and other substrates, and who have worked extensively with printers to achieve quality color and simplify processes, are providing their input. They are David Hunter, founder and principal of Pilot Marketing Group; Peter Pretzer, ColorPath solutions development manager for Fujifilm North America; Jim Raffel, CEO of ColorCasters; and Ben Starr, director of technology for the Color Management Group.
Traditional Papers
Traditional papers — those based on wood pulp — come to each print shop with their own, specific color needs. According to Pretzer, key factors affecting color on pulp-based paper products are absorbency and the range of brightness. Paper, he says, ranges from newsprint up to premium, coated stock, and international standards exist for seven specific paper types, which define their typical color spaces. Addressing absorbency, he shares that it directly affects how much ink can be put down, and that too much can lead to curling or breaking of paper on press.
The overarching concern about substrates, says Raffel, is the white point, which will shift based on additives and the amount of recycled content in the paper, as well as the presence of optical brighteners. He adds that for offset printing, the amount of absorbency affects color density. Hunter adds that the true color of the paper — particularly its cast from absolute white — is a key factor, as are opacity and texture.
Synthetic Papers
A wide array of plastic-based synthetic papers — many of which are intended for specialty applications — are also available for the commercial sector. When it comes to these products, Hunter says that texture can profoundly affect color. “If the print is on a PVC material that is smooth, it will have a totally different appearance versus, say, an eggshell finish,” he says. This has been a surprise, he adds, for traditionally focused printers who move into synthetic stocks.

The addition of optical brighteners — which utilize the same agents as laundry detergent — have a direct impact on both the color of the substrate itself, and in color measurement.
With synthetics, Raffel says the lack of absorbency can become a significant issue because the inks do not absorb, and instead must adhere to the surface — a reality under which surface tension becomes important. Pretzer adds that, much like pulp-based papers, brightness and absorbency must be understood. To that, he adds curing, which is different on synthetics than it is on pulp.
Regardless of the type of paper used, Starr stresses the need for careful substrate management. Part of this management process involves a firm understanding of how a spot color will look among the substrates available. Not only does this minimize color surprises on-press, it can also be used to preventatively address incorrect customer color assumptions.
Substrate Whiteness
The concept of “pure white” is more theoretical than it is reality. Pretzer states that while industry standards exist for what is known as “near neutral white,” U.S. standards allow a variation of up to 1.5 Delta E of the absolute, while international standards set that level to 3 Delta E.
Hunter states that, in scientific terms, whiteness is the measure of how close one can get to 100 on the L* axis of the L*a*b color space. For paper stocks at the very high end, 97 is as close to that absolute as is available. A high degree of whiteness in coated stock, he says, can result in both a wider dynamic range and larger color gamut.
Hunter adds that while absolutes of whiteness are not a reality on paper stocks, eyes will perceive the substrate as white anyway, through an effect called chromatic adaptation. “This allows for flexibility and forgiveness,” he says, “and speaks to the value of G7 color management standards, which are built around the concept that gray on any substrate will look gray.”
Starr adds that this is true as long as there is a single reference. If the white point of substrates for a multipiece, multi-substrate project is inconsistent, he says, multiple references exist, and the differences may be quite visible.
Raffel notes that in addition to the whiteness and chroma of the substrate, viewing angle can change perception of the paper’s inherent color. He says it can lead to a significant, visible change in color and must be considered.
Optical Brighteners
The profusion of papers and other substrates enhanced using brighteners has changed the way white is perceived, and not always in good ways. Starr says that optical brighteners, which utilize the same agents as laundry detergent — thus making things appear whiter — have a direct impact on both the color of the substrate itself, and in color measurement.
He states that because brighteners can reflect more blue light than is actually on the substrate, color management software can overcompensate by adding too much yellow. “It’s kind of the Wild West right now,” Starr adds about the amounts of optical brighteners used.
Optical brighteners, says Pretzer, absorb UV energy and then reemit it in a way that the eye can see — via fluorescence. A black light works the same way. Hunter says that optical brighteners can be both a wildcard and a headache because their fluorescence makes for a significant challenge in accurate color measurement.
Batch-Based Challenges
Across print disciplines, a common color-focused “surprise” is color variation from batch to batch of a specific paper or substrate, which can upend a color approach based on controllable knowns. Raffel says batch-to-batch color variations really depend on the product manufacturer.
A higher-quality name brand, he says, will have significantly less color variation because the manufacturer will have tighter production controls. He says that while some companies resort to buying seconds or odd-lot paper as a way to control costs, more batch variation is likely. It’s a choice between cost and quality.
Pretzer says that while very little variation is seen among premium products, he has noticed that the lower the cost of the paper, the higher the variation might be. Hunter says that with some products — cheap styrene, for example — batch-to-batch differences of 4 to 5 Delta E can exist. This speaks to the true benefit of investing in quality materials.
With traditional paper batches, according to Hunter, the white point can migrate due to variables in the manufacturing process. In some cases, this is due to chemistries reacting to the pulp itself, which can happen when using the same type of paper from the same company. With synthetic stock, he says, other variables may affect batch-to-batch quality.
Starr encountered a situation in which a major paper manufacturer changed the formulation of the rolled material of a specific product, but left sheet material unchanged. This unannounced change led to surprising challenges for printers used to consistency within that product. He adds that managing batch variation is an ongoing issue, and that checking lot numbers, mill numbers, and production dates can help, as can consistently buying quality products.
Finish’s Effect
Paper surfaces range from dull, uncoated stock, to shiny, glossy coated materials, and the finish of material can have a direct effect on color quality. Pretzer says that a paper’s finish can have a huge effect, particularly when a proof is printed on a coated, often inkjet-receptive media, and the final project is printed on traditional paper, either uncoated or coated differently.

Achieving great color should never be done by accident — the variability of today’s complicated array of print platforms and substrates renders this approach moot. The color of the substrate is really the “fifth process color,” because all colors come from the reflection of light from that surface.
The smoothness of coated paper, according to Hunter, allows more light to escape from the printed surface, thus allowing more visual “pop.” Raffel describes this effect by saying that more light hits the paper, and thus more light bounces back to the eye.
For better results across platforms, Starr says one key strategy is to understand the difference between coated and uncoated stocks and how the finish (glossy versus matte) can affect color, and then using that knowledge with intention. “While printing on uncoated stock is duller,” he notes, it “doesn’t make it lesser. It just depends on what you want.” On top of this — literally — he says that companies must understand how post-print coating and lamination will affect color, and recommends creating profiles that compensate for the addition of these common add-ons.
Cross-Platform Consistency
Just as today’s printers commonly use more than one type of substrate material, they may also use more than one printing platform. Pretzer shares that cross-platform concerns — whether printing is done using offset, toner, or production inkjet — are addressed through the automation of workflow and the creation of consistent processes. Equipment alignment is essential, as is process measurement.
Hunter echoes this assertion, stating that this is where a cohesive color management strategy comes into play, and how approaches like G7 can help. “People need to understand the color differences between coated and uncoated stock, and how to achieve a shared visual appearance between different substrates.”
A decade ago, according to Raffel, toner-based color “wasn’t there yet.” Today, toner color is much more acceptable, in some cases approaching offset quality. For toner, inkjet, and offset, a key factor at hand, he says, is to use the right material for the platform — a manageable, easy concept within a broader quality-based production approach.
Tales from the Trenches
Each of these color professionals has direct contact with color managers and technology users. In addition to sharing their insights, they’re encapsulating a specific paper-based challenge they have faced and the solution offered.
Working with a customer dealing with 30 different substrates that fell into 17 different profile groups, Hunter used a software solution to increase the company’s acceptable Delta E variation (to 3), and thus reduce the number of profile groups to three. In doing so, the company was able to find a sweet spot between simplifying production and maintaining quality standards acceptable to its core customer base.
Starr’s real-world example with a fashion company illustrates the value of preplanning. He worked with the company’s printer to establish the stocks that would work best for the customer’s needs. By working to align the priorities of the customer with the capabilities of the print provider, jobs were initiated with less friction.
Pretzer worked with one printing company that was challenged to print consistent color on three different types of stock. He worked with the company to create a strategy where three separate white points were used, better helping the print shop align devices and ultimately control color.
Raffel’s challenge was with a digital-focused commercial printer that had added wide-format as a way to create cross-platform campaigns. He helped the company understand its substrate-based color challenges, an approach that included careful color profiling on both coated and uncoated stock. This systematic approach significantly minimized production challenges.
Essential Tools and Training
For print service providers, managing color requires vigilance and intention. Pretzer says that training and process measurement are essential, and adds that companies should have a color “champion” in-house, and take advantage — where applicable — of customer support from both ink and paper manufacturers. “We would rather help our customers early than have them struggle,” he says.
Raffel says that because color is inherently measurable, color approaches should “always bring it back to the numbers.” Starr urges companies to acquire a spectrophotometer and know how to use it. He adds that it is essential to understand the three-dimensional color space. “Get everybody to
understand color better,” he says, “the mechanics of it, and how to communicate it.” Starr also recommends training — giving a specific “shoutout” to the Color Management Boot Camps offered by PRINTING United Alliance.
If he could simply snap his fingers and change something about paper stock and its relation to color, Hunter says he would choose to eliminate optical brighteners altogether, adding that it would make everyone’s color management life a lot easier. Raffel agrees, saying that for those who deal with color management on a daily basis, having all substrates free of optical brighteners would be a godsend.
Surely, the quality and color reliability of paper — whether pulp-based, synthetic, or otherwise — is paramount to acceptable quality, and should not be overlooked. As with many process-focused discussions within the printing industry, viewing substrates and their specific color issues as a stand-alone is a mistake. For most companies, successful printing involves a multistep process, with each step offering numerous variants, one of which is paper/substrate and its inherent considerations. Knowledge, measurement, and consistency are paramount.
The ‘Fifth Process Color’
Achieving great color should never be done by accident — the variability of today’s complicated array of print platforms and substrates renders this approach moot. Great color is about strategy, and when Raffel teaches about color, he prefers to say the color of the substrate is the “fifth process color,” because all colors come from the reflection of light from that surface. Skimping on the substrate, he conveys, is never a good approach.
When considering substrates and color, the concept of “you get what you pay for” rings true.

Dan Marx, Content Director for Wide-Format Impressions, holds extensive knowledge of the graphic communications industry, resulting from his more than three decades working closely with business owners, equipment and materials developers, and thought leaders.

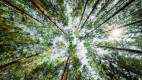

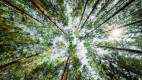

