The Flatbed Opportunity


At Western Carolina University, Jacob Massie (left) and Jeff Ray show off a sign produced on the in-plant’s Roland LEJ-640 UV hybrid flatbed printer.
In October, Elon University Print and Mail Services installed a roll-fed Ricoh Pro L4160 wide-format printer. The machine has had a very productive few months.
“The wide-format’s already paid for itself,” reveals Manager Wesley Grigg.
Despite that success, however, there’s one significant drawback to that roll-fed printer.
“Fifty percent of the wide-format we’re doing is mounted on foam core or some other hard substrate,” Grigg explains.
Related story: Making it Big
That extra step slows down productivity and requires the in-plant to send some of its wide-format work to outside printers.
Grigg knows what the solution is, though: a flatbed wide-format printer. He’s already got his eye on the technology, and is confident he will find the work on his Elon, N.C., campus to keep a flatbed printer busy — something that other in-plants with flatbeds have already demonstrated.
“It’s booked all this week solid, with basically two shifts,” reveals Terry Jarmon, director of Digital Print Services at California State University, Fullerton, where a Roland LEJ-640 UV hybrid flatbed has been bringing in lots of business. The in-plant used to print wide-format work on its Epson Stylus Pro 9900 and mount onto foam core.
“Now we’re printing directly on the foam core,” Jarmon proclaims — and that’s not the only rigid substrate the shop is using.
“We just finished a job doing metal signs,” he says; the flatbed printed right onto aluminum. “Having a flatbed gives you so many more substrates you can print on.”
And it can open up countless opportunities for any in-plant that installs one.

Standing with the University of Tennessee’s new Mimaki JFX200-2513 wide-format flatbed printer are (from left) Jack Williams, Luc Tremblay and Andrew Travis.
A Wide-Format Boom
Across the country, wide-format inkjet is booming for in-plants, as substrates and applications expand. Already 64 percent of in-plants are offering wide-format inkjet printing, according to the latest IPG research. Flatbed installations are not as robust, but it’s an opportunity just waiting to be taken advantage of. The ability to print on a variety of rigid substrates, without the need for lamination, at faster speeds, is very attractive. And not having to mount prints onto foam core is priceless.
“We used to feel that we had to print everything and mount it, and now we just print it and hand it to somebody,” remarks Tom Frazier, manager of Printing, Mailing & PAW Print Services at Western Carolina University, in Cullowhee, N.C., which uses a Roland LEJ-640 UV hybrid flatbed. In addition to directional signage for conferences and campus “yard signs,” his in-plant prints all of the university’s parking signs with the Roland flatbed.
“We probably print 50 to 100 of those a year,” Frazier says.
Big Investment, But Big Revenue

Scott Cooper prints a sign on the Roland LEJ-640 UV hybrid flatbed printer at California State University, Fullerton.
The variety of applications that can be printed with a flatbed printer can potentially generate a lot of new revenue for an in-plant. But getting into the business comes with a price. Flatbed wide-format printers are generally more costly than the roll-fed wide-format printers most in-plants are familiar with.
“You can get an entry-level flatbed these days probably for as low as $30,000,” says Dan Marx, vice president of markets and technologies with the Specialty Graphic Imaging Association (SGIA). He notes that print head costs have come down over time, which has allowed printer manufacturers to create larger arrays of heads on printers, increasing their speeds.
“So, for the same price, you may get a machine that’s three times as fast,” says Marx.
The entry cost, however, has not been a significant barrier for those in-plants that have installed flatbed printers.
“What really pushed us into the flatbed market … we were printing on an adhesive-backed vinyl material and then peeling it up and applying it onto Coroplast [corrugated plastic],” explains Frazier. After tracking what the in-plant paid for that vinyl material over a year, he made a surprising discovery.
“That total for that particular year was more than what the lease cost would have been on a flatbed printer,” he says. “And so we were able to justify it to our administration that we’re going to buy a much nicer piece of equipment, we’re going to eliminate a step, we’re going to save money [and] we’re going to print directly on the material.”
Frazier adds that his school’s out-of-the-way location may have also played a part.
“We’re not far from the Great Smoky Mountains National Park, so out here, if we can’t do it, there’s not many options,” he notes.
His in-plant has done a variety of projects with its Roland LEJ-640, such as museum displays and team information signs posted in locker rooms.
“We have printed a fair amount of Plexiglass where we print the image in reverse and then print white on top of it,” Frazier explains, “and then when we’re done, you flip it over and you’re actually looking through the Plexiglass at the image.”
Frazier has been very impressed with the output from the flatbed printer.
“The quality of the color we get off of it is excellent,” he praises. “The quality is just breathtaking.”
UV Curing Advancements
This is because the UV curing process instantly dries the ink, which adheres to the substrate surface. Recent advancements in ink technology have made this ink less brittle after curing, so it won’t crack as easily as it would have in the past.
“Over the last few years, a number of manufacturers have come out with physically flexible UV-curable inks,” notes Marx.
Most of the flatbed inkjet systems being sold today, he says, use UV curable ink, which adheres well to a wide variety of materials. Lamination may not even be required, he says, depending on the substrate and the intended use of the print. Where in years past the curing was done using hot mercury-vapor lamps, these days UV LED lamps are taking over, he says.
“Generally those systems don’t generate much heat at all, so the machine doesn’t need either water or air cooling systems,” he notes.
UV LED systems require less maintenance and they can be plugged into standard 110-volt electrical outlets, he points out.
“So that’s been kind of a game changer in a big way,” Marx says. “It’s brought UV curing down to the level where in-plants can get it.”
He has two important tips for in-plants getting flatbed inkjet presses:
- “Protect the heads.” They are very expensive.
- “All inkjet machines like to run. If a system is sitting in the corner and it’s powered up every six weeks, it’s going to be probably kind of glitchy and problematic.”
Hybrid Versus True Flatbed
There are two types of flatbed printers on the market.
True flatbeds hold the media stationery on a table while the print heads move across the media. The print size is limited by the size of the bed.
Lower-cost hybrid systems, which also handle roll-based media, move the rigid media through the stationary printing area. Hybrid flatbeds make up the majority of installations, Marx says.
Bucking that trend is the University of Tennessee, which recently installed a Mimaki JFX200-2513 wide-format flatbed printer in its Knoxville facility. With one of its two print heads running CMYK and the other reserved for white and clear ink, it can print up to four 4x8´ boards per hour.
“We can print on just about any flat material up to 2˝ thickness,” remarks Director Jack Williams. “And the material is stationary when printing, which will allow for additional passes, if needed.”
Because the substrate stays still — held flat by a vacuum table — registration is much better than on a hybrid flatbed. The in-plant prints on Coroplast, foam board, PVC and aluminum-faced material, Williams says.
Prior to getting the Mimaki, the in-plant used its Mutoh ValueJet 1608 hybrid printer to print on flat substrates, Williams says, but it was a slow process.
“The Mimaki is four times faster on the flat substrates,” he maintains.
To cost justify the Mimaki, Williams examined the shop’s wide-format expenditures.
“In the past fiscal year, we outsourced, in wide-format sales, almost equivalent to the cost of the Mimaki,” he says. Based on this, Williams calculates an ROI time of between two and three years.
Bringing Flatbed Printing In-house
This matches the ROI that fellow Tennessean Sean Carroll projects for the flatbed inkjet printer he plans to install at Vanderbilt University in Nashville.
“I’m outsourcing about one third of what the cost of an entry-level machine would be,” notes the director of Printing Services. The shop has been buying flatbed printing on foam core, gator board, PVC, acrylic and other substrates from a local supplier for nearly five years.
“Unfortunately, with that comes a bit of a cumbersome process,” he points out. “We’ve got to do a purchase order, we’ve got all the paperwork on our end, we’ve got to dispatch a courier. It would be a lot easier to have one within our four walls, to be able to produce at a lower cost [and] offer a quicker turnaround time.”
He could also control the university’s branding better by doing the work in-house, ensuring that all printing — offset, toner or UV inkjet — is consistent. And being able to show customers the flatbed printer at work during open houses will be worth its weight in marketing gold, he says.
The in-plant is currently getting proposals from vendors for a new flatbed. Carroll sees a lot of potential business for the printer once it arrives: temporary event signage, campus maps, photo artwork, permanent signage. Just walking around campus, he sees countless wide-format applications that aren’t even being ordered through his department.
“I think it’s got unlimited potential,” he enthuses.
Carroll intends to provide signage templates on the EFI Digital StoreFront system the in-plant is currently implementing to facilitate online ordering.
Signage isn’t the only application though. At CSU Fullerton, the in-plant has printed name badges on plastic blanks, 20 to a board, with a clear coat on top for an embossed feel. Adding the Roland LEJ-640 hybrid flatbed has been a big win, Jarmon says, bringing in lots of new business and saving money.
“People always think, ‘oh, well that’s so much more expensive,’” he says. “Actually, production-wise and labor-wise, it’s cheaper.”
At Western Carolina University, Frazier anticipates the work will continue flowing in for his shop’s Roland LEJ-640. Even in the age of mobile technology, he says, there’s still a strong need for printed signage.
“With all the ways we have to connect to students,” he notes, “sometimes a sign in front of them is the only way to get their attention.”
- Companies:
- Ricoh Corp.

Bob has served as editor of In-plant Impressions since October of 1994. Prior to that he served for three years as managing editor of Printing Impressions, a commercial printing publication. Mr. Neubauer is very active in the U.S. in-plant industry. He attends all the major in-plant conferences and has visited more than 180 in-plant operations around the world. He has given presentations to numerous in-plant groups in the U.S., Canada and Australia, including the Association of College and University Printers and the In-plant Printing and Mailing Association. He also coordinates the annual In-Print contest, co-sponsored by IPMA and In-plant Impressions.

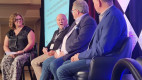



