The Flat Printer Society
The need to provide a broader range of printed products has driven in-plants to explore new technologies, and one that is increasingly showing up on production floors is the flatbed wide-format printer. Often installed to eliminate the need for mounting prints onto foam board, flatbed printers have subsequently opened up new opportunities and allowed in-plants to provide products they hadn’t imagined previously.
At Ohio State University’s UniPrint operation, the first flatbed printer was installed in 2010, and was replaced last year by an EFI H-1625. Having a flatbed printer has transformed the Columbus, Ohio, in-plant’s workflow and allowed it to keep more work in-house while streamlining operating costs.
“Eight years ago, we would print on paper and mount to foam board,” says Plant Manager Jim Strapp. “Anything outside of that we would send to a vendor to produce or the customer would use a local vendor for their signage needs. Now we do 95% of our work in house. We are doing a lot of board work. Foam board and Coroplast are our main substrates for rigid material.”
At Modern Woodmen of America, in Rock Island, Ill., the in-plant installed an HP Scitex FB 750 flatbed printer in late 2016 and has had great success with it.
“We identified a need to print directly onto thicker substrates,” explains Print Services Manager Tim Fanella. “Also, we wanted the ability to print large banners. The addition of the Scitex allowed us to do both.” In particular, he notes, banners and yard signs were just outside of the shop’s capabilities before; the flatbed has allowed the in-plant to bring that work in-house.
Meanwhile in Nashville, Vanderbilt University Printing Services realized that to continue to meet the needs of the university, it was going to need to transform itself. So in 2016, the in-plant installed an HP Scitex FB550 flatbed UV printer, alongside an HP Latex 360 printer.
“As the department evolved to meet the needs of the university, it was apparent that our customers wanted a one-stop shop for their print communications needs,” explains Sean P. Carroll, director of Business Operations. “Wide-format print seemed to be the next logical step in our evolution, and customer response has been amazing. From an efficiency standpoint, it also made sense; we were able to reduce the number of steps it took to produce a presentation or display board and, in turn, increase our value to the customer. What we didn’t realize at the time of our acquisition, however, was quite how big the potential market for specialty applications really was.”
Reaping the Benefits

Operator Jeff Krigbaum shows off Ohio State University’s EFI H 1625 flatbed printer, which it installed last year.
For all three organizations, the benefits to having a flatbed printer have been surprising. Vanderbilt knew it would see productivity gains, but, as Carroll notes, the in-plant wasn’t expecting the explosion of opportunity that followed the acquisition of its two wide-format devices.
“While we have saved money by bringing in previously outsourced work, the biggest gain has been in expanding the market,” Carroll says. “We are able to sell new solutions to customers who previously did not order wide-format printing, and have really worked to become their in-house marketing resource when it comes to graphics. One exploding market for us, for instance, is in outdoor sidewalk graphics. There is a lot of interest, and with our latex printer, we’re now able to say ‘yes’ to these needs.”
That ability to say “yes” translates into money saved for these in-plants, which in turn helps them demonstrate the value they bring to their organizations. This value is not just measured in cost savings either; by having the capabilities of a flatbed printer at their fingertips, the in-plants can also take on last-minute projects with ease.

Vanderbilt University Printing Services’ flatbed printer has enabled the Nashville-based in plant to print signage for buildings all over campus.
“We have been able to save money over outsourcing and provide better service. Often these jobs require quick turnaround. By bringing this machine in-house we can often turn jobs in as little as a few hours,” Fanella notes.
But these benefits don’t just appear out of nowhere. Flatbed presses do have a learning curve.
“Substrates [were] the biggest learning curve,” Strapp declares. “There are so many offerings of materials and suppliers. Once we got over the ‘we can print on anything’ mentality we let our orders drive what material we keep on hand.”
Storage and Transport
Beyond substrates, another issue in-plants need to consider when adding a flatbed printer is that boards can be challenging to store and transport. They must be protected from damage while they’re being moved.
“Protecting a 48x72˝ foam board is tricky at times,” Strapp affirms, “but once you learn how to handle the material it gets easier.”
“Transportation is a challenge,” Carroll acknowledges. “Freight can often be a costly factor in addition to the cost of the board. To that point, stocking up on a single material can be a very expensive proposition. I recommend starting small, and gradually expanding your offerings. Work with your suppliers … to get samples, and test, test, test.”
Also, adds Fanella, don’t forget to take into account vendor training and support when deciding on a flatbed printer to purchase. Finding a vendor that is willing to work with the in-plant to ensure all of the staff knows how to best use the equipment and get the most out of every job can be the difference between a flatbed printer that transforms the entire operation, and one that languishes in a back room, rarely touched.
Adding a flatbed printer can open up new doors and spur the creativity of the rest of the organization. It can reduce turnaround times and streamline operations by removing the need for mounting and laminating. Those are good reasons to consider whether or not a flatbed printer should be the next investment your in-plant makes.
All of the latest flatbed wide-format printers will be on display at the upcoming 2018 SGIA Expo, Oct. 18-20 in Las Vegas, along with contour cutting, dye-sublimation, garment and 3D printing technologies. Visit www.sgia.org for more information.

Toni McQuilken is the senior editor for the printing and packaging group.

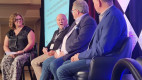



