What's the future of offset technology? Find out where direct imaging is taking it—and how presses may eventually shed plates altogether.
Look at the trends: Shorter runs. Faster turnaround demands. Digital job data. Cut-throat competition.
Many printers won't survive. Those that do will have to use new technology to heed these trends.
That's where on-press imaging comes in. It offers everything today's business climate demands: Short-run efficiency, lower costs, faster makereadies and fewer steps.
True, direct imaging (DI) is nothing new; Heidelberg introduced its GTO-DI in 1991. But DI quality has improved since then. New imaging systems from Presstek and CreoScitex have paved the way for more DI presses. At Drupa, some nine vendors showed DI products, a clear statement that offset is heading in this direction.
"The quality is equivalent to conventional offset," remarks Eric Frank, Heidelberg's vice president of marketing for direct imaging and digital printing. Frank was one of four panelists at a seminar on DI held at the recent On Demand Conference in New York. He and representatives from Xerox, Presstek and CreoScitex discussed the benefits of DI, including perfect registration, lower production costs and faster prepress times.
The Cost Factor
The one hurdle that hasn't been cleared, however, is price. Frank says DI presses cost 25 to 40 percent more than conventional models—but he adds that computer chips and other electronic components are getting cheaper. DI presses, he says, will drop in price perhaps 5 percent a year.
"As technology becomes more affordable, it will be adapted more readily," he says of DI.
One sign that DI is destined to stick around is the entry of Xerox into the market. The company showed its DocuColor 233 DI-4 at On Demand and is offering a larger-format press, the DocuColor 400 DI-5, as well.
"We know the digital business better than anybody else in the graphic arts," contends Ron Kendig, general manager of direct imaging for Xerox. "And we think we're in a good position to move people into digital."
Xerox entered the offset world "to round out the product line," Kendig says, and because its customers are moving in that direction. Whatever experience Xerox lacks in supporting offset, he adds, it is making up for through a partnership with Presstek, which has years of DI experience.
Indeed, Presstek's ProFire is the imaging system most DI press manufacturers have chosen. Its advantage, says Efrem Lieber, Presstek's vice president of sales, marketing and customer support, is its compactness.
"Profire is a modular, integrated system," he says. "We've put everything together in the imager that's required to do on-press imaging in a compact system that can essentially be fitted to anybody's press"—particularly A2, A3 and A4 sizes, he adds.
On some larger presses, like the 40˝ Komori Project D and the Heidelberg Quickmaster DI 46-4, CreoScitex SQUAREspot is the imager of choice. Its advantage, says Brad Palmer, director of short-run printing with CreoScitex, is its very high optical resolution, which yields sharper, crisper images than Profire. It's also faster, he says, and has higher process stability.
But Lieber says Profire is more reliable. "We're designed for high reliability," he says, adding that Presstek has been selling lasers for DI presses for eight years.
Though most DI machines are basically traditional offset presses with laser imaging tacked on, some manufacturers have started from scratch. Karat Digital Press (a Scitex and KBA joint venture) has rethought the whole offset process with its 74 Karat press.
For example, the press has just one impression cylinder and two plate cylinders, each with two plates. Two colors are laid down on the first pass, and two on the second pass. The feeder and delivery are on the same side, next to the console.
David Bartram, director of marketing, says that most DI press makers are trying to overcome the inherent weaknesses of offset.
"Our approach is to make the process itself more efficient and still use the technology to make the whole system work," he says. He boasts that the 74 Karat offers "operator-independent color." It uses a keyless, self-calibrating inking system called Gravuflow, designed to provide consistent, predictable ink coverage.
"In 10 sheets the machine's up to color," he says.
Other new DI developments are afoot, as well. At Graph Expo, CreoScitex demonstrated plateless printing by spraying a laser-imageable polymer onto a plate sleeve. Its SP plateless digital offset printing system uses a liquid media from Agfa. The process is targeted at short-run printing, though Palmer says CreoScitex hopes run lengths reach 50,000 before the product goes commercial.
"We can now completely automate the changeover so it's just one click on the screen and the entire changeover of the press occurs," he says. "There's no need for manual intervention. The amount of press time you consume to do the changeover goes down."
In addition, printers will save lots of money on plate costs.
The quality of the samples at Graph Expo was good, but Palmer is confident it will be much better by the time the product goes commercial in a few years.
Direct imaging will undoubtedly change offset printing. But conventional presses won't disappear, experts say.
"Is every press going to be loaded with a direct imaging system?" asks Presstek's Lieber. "The answer is no."
But certainly, he adds, the printers who want to stay ahead of their competition will be moving toward direct imaging.
See our DI comparison chart in the print edition of the April issue.
by Bob Neubauer
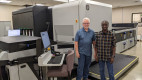



