No more film. Faster makeready. Better quality. Direct imaging presses seem to have everything a printer wants. Is this where the industry is going?
SAFECO had a dilemma. Press runs at its in-plant were getting increasingly shorter, and these short-run jobs were keeping the six-color 20x28˝ Mitsubishi constantly busy—so busy that when long-run jobs arrived, they frequently had to be outsourced.
"We knew we needed another press, and we needed a press that would facilitate the shorter-run jobs," recalls Larry Jablinske, manager of graphic and printing services for the Seattle-based insurance and financial services firm. Additionally, the new press would have to run five colors and have inline coating.
After first looking at conventional offset options, members of the in-plant's staff stopped at the Omni-Adast (now Adast America) booth at Graph Expo and saw direct imaging (DI) in action. After talking to customers and running test files on the press, they knew they had found their answer.
In October the in-plant installed a five-color, 19x26˝ OMNI-ADAST 755C DI press with an inline coater, and life hasn't been the same since.
"The makeready is very quick," Jablinske enthuses. "Generally you've got good copy with about 50 sheets of paper." Registration is always perfect because plates are imaged on press, he says. Since files can be sent right to the press, prepress functions are eliminated and jobs get printed much faster. And despite a slight increase in plate and ink cost, overall costs have dropped dramatically, he says.
"We were able to save about $800,000 a year," Jablinske reveals.
SAFECO's in-plant is just one of the latest printers to realize the benefits of direct imaging. These include reduced material and labor costs, faster makereadies, more accurate registration, and the ability to access, archive and retrieve jobs. Plus, by using digital data for on-press plate imaging, quality increases. DI presses eliminate the exposure and processing of film, manual stripping and assembly, plate burning and processing, manual registration and other traditional procedures.
"In any manufacturing process, when you eliminate manufacturing steps, almost by definition you increase quality and reduce cost. That's what DI presses are doing," notes Doug Clott, North American sales and marketing director for Karat Digital Press.
Karat, a Scitex/KBA joint venture, showed its 74 Karat press at Graph Expo and will launch the commercial version at Drupa. It is currently installed in six beta sites.
Heidelberg and Adast America have been offering digital imaging presses for years, but a number of other vendors have products on the way, most of them set to debut at Drupa (see page 40) next month:
• Sakurai Graphic Systems will show the newest version of Presstek's DI technology in its four-page Oliver-474EPII DI press. It can be run in either DI mode (using Presstek's PEARLgold plate media) or in conventional mode.
• MAN Roland plans to show its new DICOweb digital web offset press, which uses Creo Products' SQUAREspot thermal imaging.
• Screen (USA) first showed its new digital imaging system, the TruePress 544, at Graph Expo. It uses an offset process and conventional CMYK process inks.
• Akiyama, in partnership with Presstek, is working on a DI press, but it will not go into production until 2001.
• In addition, Presstek and Adast have announced an automated, two-page DI printing press. It will be available in four- or five-color configurations, and will use Presstek's internal, automatic plate cylinder design and Presstek's PEARLdry Plus plates.
What's Available Now?
Until this Drupa DI onslaught occurs, Heidelberg and Adast still rule the DI world. Heidelberg offers the Quickmaster DI 46-4 plus, a two-up, waterless press that uses polyester thermal plates, and the Speedmaster DI 74, a four-up press that uses metal thermal plates. Adast currently carries the 705C DI, which uses waterless thermal plates.
In the Quickmaster DI 46-4 plus (the enhanced version of the Quickmaster DI), each plate cylinder has an autowinding unit with two rolls. Fresh plate material for new jobs is taken off one roll while used masters are simultaneously wound onto the other roll. When a new job is RIPed and sent to the press, plates are advanced and tightened automatically, then imaged in under four minutes. In less than 10 minutes, a job can go from the RIP to the first sheet, according to Victor Wiley, Heidelberg's direct imaging sales manager for the western region. Because of this quick workflow, he says, costs go way down.
"The DI can print economically in the range of 200 to 300 sheets, on the minimum end, per run," he says. "We see the market between 500 and 5,000 [sheets]."
In a recent study of DI users conducted by CAP Ventures, a market research firm, users reported average profit margins of 42 percent. Ninety-eight percent said the DI had made a decisive contribution to their growth, and they reported that sales are growing 40 percent annually.
The Speedmaster DI 74 is a much larger press. Available in four-, five- or six-color configurations, with or without coating and perfecting, it takes a maximum sheet size of 21x291⁄8˝, and runs 15,000 sheets per hour. Like the upcoming Sakurai Oliver-474EPII DI press, the DI 74 can run both standard plates and DI plates.
On the Speedmaster DI 74, operators must hang the plates, though they are automatically loaded and tightened. This takes about a minute for each. All four plates are then imaged in less than four minutes. Total makeready time is about eight minutes.
The 74 has imaging devices on each printing unit. A single laser scans across the plates. Using Creo Squarespot thermal imaging technology, plates are simultaneously imaged in up to six printing units at 2,400 dpi. By comparison, The Quickmaster uses a common impression cylinder with four printing units around it. Each unit has a bank of 16 lasers. Laser beams remove silicone on the waterless plates to expose polyester areas, which accept ink. At Drupa, the new CP2000 operating system will move to the 74.
The Adast 705C DI Series has a maximum sheet size of 19x26˝ (181⁄2x251⁄2˝ printing area) and run speeds up to 10,000 iph. Because the press is waterless, chemical wastes are eliminated.
As plates are being imaged, a remote color console automatically adjusts for sweep and registration and sets the ink key profiles. In place of dampening units on each tower the PEARL System uses 32 laser diodes to generate dots on the plates at up to 2,540 dpi.
Adast is poised to debut a new DI product, geared toward in-plants. The 500 series will be a 15x201⁄2˝ press that uses poly plates and a take-up reel, similar to the Quickmaster DI 46-4 plus.
"Because it's all automatic, you can change all five plates in the press in 20 seconds," explains David McMaster, managing director of Adast America. "The plate cylinder itself declutches from the drive train so it can spin without the press rolling, and then we spin the plate cylinder at 22,400 an hour while we're imaging, and we image standard resolution jobs in two minutes and 20 seconds. So what that means is that in three and a half minutes you can be done imaging and plate changing on a five-color press, and then start printing at 200 sheets a minute." This comes out to 12,000 sheets an hour.
"It makes us competitive on a production timing standpoint at runs of under 50 or 60 sheets," McMaster adds.
This speed will be possible because of advances in laser technology. The new 500 series will use the ProFire integrated imaging system, from Presstek. Presstek has been involved in the DI world for many years, providing the imaging systems for the initial Heidelberg and Adast DI products. ProFire will reportedly make direct imaging, both on- and off-press, significantly more affordable. Its laser diode system comprises four-beam laser diodes and fast laser drivers.
Dry Direct Imaging
Another new DI offering, the 74 Karat waterless offset press from Karat Digital Press, interfaces with an offline digital prepress system, offering complete digital workflow and color management. Boasting an automated 15-minute makeready, it is optimized for short- to medium-run four-color print jobs. The 74 Karat press can print up to 10,000 sheets per hour in formats up to 201⁄2x29˝. It images all four aluminum plates on press in six minutes.
One difference between the 74 Karat and other DI presses is that it has just one impression cylinder and two plate cylinders, each with two plates. Two colors are laid down on the first pass, and two colors on the second.
"The advantage of that is that you only need two imaging heads instead of four," notes Karat's Doug Clott. "We didn't take a conventional press and put imaging on it. We said, 'Let's make a press that does short runs cost-economically and build everything you'd ever want into it.' "
As a result, the 74 Karat is a very compact press, with the feeder and delivery on the same side, next to the user console. The 74 Karat uses a keyless, self-calibrating inking system called Gravuflow, designed to provide consistent, predictable ink coverage over the entire sheet. Ink is packaged in cartridges, and it flows from there into the ink chamber, monitored by sensors, which automatically keep ink at a prescribed level. As a result, the 74 Karat lays down high-density, smooth solids over the entire sheet, along with crisp, uniform dot structure. The imaging system produces screen rulings in excess of 200 lpi.
Clott praises the elimination of ink keys, noting that operators don't have to adjust the press for color.
"Once you have a consistent, predictable output machine, you can prepare your file more precisely for the output device," he offers.
But Wiley, of Heidelberg, disagrees, saying that ink keys let you adjust the amount of ink in any given area. Without ink keys, he adds, "That would hold them back in a longer makeready to try to achieve color."
On the 74 Karat, plates are automatically changed, imaged and cleaned while the press parameters for the new job are set. Perfect register and full, proof-matching color are achieved without any operator intervention within 20 sheets of starting the run. The press can reach full running speed within 100 sheets.
The TruePress 544 digital imaging system, from Screen (USA), does not yet have any U.S. installations. It comprises a digital imaging and offset printing unit, and a controller that handles tasks like job control and RIP processing of page files. Geared for short-run work, the TruePress 544 uses Mitsubishi Silver Digi Plate polyester plates. It runs at half the speed of the Quickmaster DI, printing up to 4,000 impressions an hour for four-color work or 8,000 iph for two-color work, using conventional process inks.
"We see this as being an important next step for Screen—digital imaging presses," notes Rick Siwicki, marketing and sales manager for Screen's support products division.
MAN Roland's new DICOweb digital web offset press images directly onto press cylinders and automatically erases the images after printing, eliminating plate changes. It is targeted at short-run (500 to 20,000 copies) color printing and features cylinder sleeves that can be quickly changed to accommodate different printing formats.
Creo developed the thermal imaging system, as well as the control electronics and associated software supplied to MAN Roland for the DICOweb. Its SQUAREspot thermal imaging technology, which boasts fast imaging times and high optical resolution, has also been integrated into Heidelberg's Speedmaster 74 DI.
The Future Of Direct Imaging
Manufacturers see a number of possible trends in DI. Clott, of Karat, feels that in the future, DI presses will be able to run more types of substrates, and they will incorporate variable data printing through the use of ink jets on the back end. UV drying may also get incorporated, he says.
Heidelberg's Wiley agrees with this last prediction.
"We're working on drying technologies to shorten the production process from printing to going to postpress," he says.
Though many in-plants are waiting for prices on DI equipment to drop, Wiley says Heidelberg is instead adding features, giving printers more for the same price.
McMaster sees DI presses moving in the direction of Adast's new 500 series, with automatic plate replenishment and blanket washing. He also predicts faster imaging speeds due to more powerful and compact lasers.
In the end, though, the future of DI depends on its acceptance by printers. From Jablinske's perspective, that future is secure at SAFECO.
"It is probably the future in our industry here," he says. "I couldn't see us buying another press that was not direct imaging. It just makes sense."
DI vs. Indigo And Xeikon
Despite the cost savings on short-run jobs offered by DI presses, digital devices from vendors like Indigo and Xeikon are also geared toward short runs—and they allow variable data printing, as well. So why should anyone bother getting a DI press?
That's what Benny Landa, Indigo's founder and chief executive, wants to know. He feels that a battle is taking place between mechanical offset and digital offset color printing.
"Offset printing is fighting digitization with hybrid machines—mechanical printing presses fed by CTP systems and on-board platemakers," he says. "But it is inevitable that everything that can become digital will become digital. And in this digital era, I believe these transition technologies are foredoomed to a relatively short life."
Indigo recently announced a new four-engine digital web press designed to bring offset-quality digital printing to the mainstream commercial printing market. Boasting variable data printing capabilities, the Indigo Publisher 8000 prints 8000 four-color A3 images per hour, and comes with in-line finishing. Another product, the Publisher 4000, has two engines and offers half the speed. Both products use Indigo's liquid electro ink.
Also touting the benefits of variable data printing, Xeikon recently added a sheetfed digital printing device to its line of web products. The CSP 320 D is labeled an entry-level, production strength digital color press built to handle monthly volumes of up to 100,000 sheets. It outputs 960 duplex 81⁄2x11˝ color impressions per hour, and its digital workflow eliminates makeready time and costs. Though it uses dry toner, Xeikon says it has developed a new toner for the CSP 320 D that provides a tonal range and color fastness equal to typical offset ink specifications.
These devices have their niche, admits Heidelberg's Victor Wiley, but for run lengths between 500 and 5,000, a Heidelberg DI press will print faster and more cost-effectively, he says.
To back this up, Larry Jablinske, manager of graphic and printing services for SAFECO, notes that his in-plant already had an Indigo digital press before it added the Adast DI press. He says it made more sense to use the Indigo for the really short run work—under 500 copies—and get the new press for volumes over that. Plus, he adds, even though the Indigo press' quality is very good, his customers wanted offset-quality work.
No doubt this news would set Indigo's Landa on edge, but the perception remains among printers and customers that conventional offset presses still provide better quality printing. And DI presses, at least according to Jablinske, provide even better quality than conventional offset.
"We had some brochures that we'd been printing on the Mitsubishi, and the front of the brochure had a house on it, and the house was always white," he says. "We moved the job over to the Omni [Adast 755C DI], and we saw the house had a beige tint."
After looking closely at the printed piece, his operators made a surprising discovery: Dots.
"The dots were always in the file, but they dropped, in going to negative to press. They were very small dots, but they were there and very clear. The quality and the detail that you get off of the press is pretty phenomenal."
by Bob Neubauer
- Companies:
- Heidelberg
- Manroland
- Presstek Inc.
- People:
- Karat
- Larry Jablinske
- Places:
- Adast
- Heidelberg
- Seattle
- U.S.
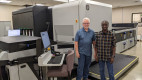




