Student Employees Give An Edge
Employing students part-time has allowed many college and university in-plants to prosper, helping them achieve Top 50 status in the process
By Erik Cagle
Not all in-plants are created equal. If they were, then we wouldn't have the IPG Top 50.
One look at that list, though, reveals that college and university in-plants have a special advantage: their ability to cull a large number of part-time employees from their student populations. Many of them owe their lofty status on the Top 50 to employing students; frankly, some in-plants would not have cracked the list without them.
Students are cheap labor; they're intelligent and bring (for the most part) a positive, cheerful disposition to the job. Employing them allows the in-plant to save on paying full-time benefits and increase staff during peak periods without assuming long-term commitments.
"I think [using students] is one of the many reasons we have a reputation for providing great service and competitive prices," remarks Gary Boyd, manager of Iowa State University Printing Services, where between 25 and 30 part-time student employees enable his operation to provide a high level of service, extended hours and faster turnaround times.
The practice of university in-plants employing students is not a one-way reward avenue. These youngsters are given the opportunity to learn hands-on skills, keep abreast with printing technology, gain an appreciation for the responsibilities that come with employment and pick up a little pocket money in the process.
"We could not function without our students," states Doug Maxwell, director of the Print and Mail Production Center at Brigham Young University. Considering that BYU's Provo, Utah-based in-plant is ranked eighth on the Top 50, the statement is not a mere platitude.
Maxwell oversees 200 part-time student workers, a figure that balloons to as much as 270 during peak periods. Since the various departments at the school have the option to take their work elsewhere, Maxwell leverages his student population.
"One of the strategies we use is, if you print or mail with our organization, then you're providing students with jobs," Maxwell says. "We spend about a twelfth of our annual revenue on our students. So I would say they have a significant impact on our revenue."
With 35 part-time employees, Washington State University's in-plant saves about $100,000 a year in salary and another $50,000 in benefits, according to Steven Rigby, director of printing and Web development at the Pullman-based in-plant, which ranked 38th on the Top 50.
Employing Students: Only Fitting
Universities and their in-plants exist only to serve the students, notes Rick Wise, director of Printing Services for the University of Missouri-Columbia. So it is only fitting that students are given the opportunity to work at the shop on a part-time basis.
Wise's in-plant, which ranked 28th on the Top 50, generally employs between 22 and 24 part-time student employees. They all work at the campus Quick Copy Center in the main student commons building where the campus bookstore is located. They are paid between $5.25 and $6.25 per hour, according to Wise, which is on par with what the shop would pay an outside part-time employee.
"The student employees typically bring a lot of enthusiasm and energy to our Quick Copy Center," Wise says. "They obviously communicate effectively with our many student customers. The students are also quite proficient on computers—a big plus—and are quick learners."
In Minneapolis, Dianne Gregory, executive director of general services at the University of Minnesota, notes that while her shop's 28 part-time student employees are paid above minimum wage, the scale is on a par with outside part-time help.
But using students has enabled the in-plant to save money in other ways, she adds.
"The ability to flex staff during busy and slow times with students saves the department money and enables us to provide better service," Gregory says. All this has contributed to the in-plant's number 32 ranking on the Top 50.
At Iowa State University Printing Services, Boyd notes that some of his student employees are used for on-campus deliveries, while others perform production and assist customers in satellite centers. Student employees staff one of the in-plant's locations for evening and weekend hours.
ISU students typically start out at a scale lower than those in full-time temporary positions do, but those who stay on and perform well receive increases. Many students end up working with the in-plant their entire college career, Boyd notes.
Lots of Applicants
In addition to cost savings, there are other advantages to employing students. At BYU, Maxwell can choose from a pool of 27,000 students. It is not uncommon for him to receive 20 applications for one job opening, which allows him to be selective in hiring.
"We have sharp kids who interact well with customers," Maxwell says. "A lot of my full-time people began here as students. I don't have to spend a lot of time recruiting."
Maxwell notes that scheduling is easier than most would think. Even with 200-plus part-timers, Maxwell uses a four-hour block schedule, with morning, afternoon and evening to easily situate the work schedule. Because he sees his in-plant as part of the educational process, Maxwell is sensitive to students' academic needs, and is flexible with scheduling.
The students have allowed Gregory's shop at the University of Minnesota to provide quicker turnarounds on jobs during the peak season. Another critical factor is the educational slant—students are more receptive to new technologies and aren't fazed by computers, programming and file transfers.
"In our Copy Centers, this is especially helpful as we talk customers through sending files electronically for various types of equipment," Gregory adds. "In general, our ability to process more work electronically is a benefit to our business, which keeps us in the Top 50."
Washington State University's Rigby enjoys students that have built-in computer savvy. All three of the school's copy centers are networked, and the students are at ease with manipulating jobs.
"They're a lot easier to train because of their computer backgrounds," he says.
Another advantage student workers provide, Rigby says, is the ability to staff the copy centers on weekends, which allows the shop to compete with Kinko's. And while there isn't a surplus of walk-up work, the weekends give the shop a chance to catch up on overflow work.
Challenges With Student Workers
The greatest challenge brought about by the student employees involves the scheduling, notes Wise. Homework, studying and activities cause him to juggle the schedule constantly.
On occasion, Wise will encounter students who are immature, have poor work ethics or are dishonest. But the ratio of students to "outside" employees who fit that description is probably equal, he says.
Gregory tries to create a mutually beneficial atmosphere, but there are drawbacks for those who expect the part-time position to be an opportunity to get in some neglected studies. And for some students, mastering the job can be difficult if they aren't putting in enough hours to learn the craft.
Iowa State's Boyd occasionally has issues with the pick-up and delivery service because the shop has a policy that forbids students from handling exams. But he finds a majority of his student experiences to be very positive.
There are times, however, when even these fragile, young employees can help provide a different vantage point and bring something to the table. What Gregory likes about having the student workers is the fresh perspective they bring with them, as well as serving as a conduit to student, staff and faculty needs.
Boyd also notes that since the student workers ask a lot of questions, they sometimes make him rethink shop procedures and processes.
"We learn a lot from them," he admits.
Students Benefit Too
For students, working part-time at university in-plants represents more than just an opportunity to pick up some pocket money.
Rick Wise, director of University of Missouri-Columbia Printing Services, sees it as a mutually beneficial experience; the students have helped his in-plant attain its position on the IPG Top 50, and in return they have gained skills that will benefit them later in life.
"The student workers benefit by learning to follow a work schedule," he says. "They get to work with a cash register and process Quick Copy orders, and learn the responsibility of being an employee and getting along with both co-workers and customers."
Dianne Gregory, executive director of general services at the University of Minnesota, points out that her shop supports the university's academic mission, including hiring a design student in a paid intern position each semester. Depending on their experience, these students can be given live projects to accomplish, and Gregory has heard students comment about how invaluable it is to have copies of live printed pieces for their portfolios.
Though it is a working endeavor, the in-plant provides ample learning opportunities; students can learn prepress, press and postpress functions and gain an understanding of how to design for print. Gregory also sends them to trade shows for further exposure to the process.
"As a university in-plant, we believe it's our responsibility to form academic partnerships," she says. "The design area is a natural fit and our art director—who was once a design intern here—is a member of the design board on campus and helps keep the design faculty aware of the needs of the print business."
At Washington State University, Steven Rigby, director of printing and Web development, believes the work experience allows the students to grow as people, mature, accept responsibility and work with older people and authority figures.
"We're able to teach them life skills and work skills they normally wouldn't get until after they leave school," he says. "Sometimes college kids can get cocky, so they need to know they have to answer to somebody. This also gives them practical experience—some are interested in pursuing a publishing career."

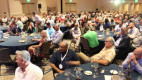



