CTP can substantially slash the amount of time, labor and money needed to complete an offset job.
by Mike Llewellyn
Michael George is a very busy man. Whether he's meeting with customers, flying to trade shows or solving any number of daily crises in the in-plant, he's always looking for a way to get a little more time.
George is director of Villanova University Graphics, a 13-employee shop tucked away on the second floor of Galberry Hall in a far corner of campus. Operating in what was once a house, the in-plant is its own storm of activity, and it's in a constant race against the clock.
A little over two years ago, George says the Philadelphia-area in-plant made a purchase designed to beat the clock—a Heidelberg Quicksetter 400 computer-to-plate (CTP) system. Picked up at Graph Expo 2000, the Quicksetter images both film and plates. It has helped Villanova's in-plant handle some major volume increases.
"The type of work that we're doing has stayed the same, but the volume has really increased," George says.
CTP has helped the shop keep up.
With some 30 percent of in-plants now using CTP systems, according to IPG research, the message seems to be getting out: CTP can substantially reduce the amount of time, labor and money necessary to complete an offset job. In-plants that use platesetters agree.
Waste Management
Back in October 2001, the Wal-Mart Printing and Mailing Distribution Center, in Bentonville, Ark., installed a CreoScitex (now Creo) Lotem B2 thermal platesetter. Replacing an older imagesetter, the Creo unit has cut up to 75 percent off the usual makeready time, according to Prepress Manager John Brouse.
"The auto-load system is very good for time," notes Brouse. "And it's also very reliable. It's only gone down hard twice. But those weren't really major problems."
He says the shop chose a Creo platesetter for its flexible filing system.
"You work with pre-RIPed files. You can archive a job and bring the file up without having to RIP it again," he explains. Altogether, Brouse says prepress time has dropped from an hour to 15 minutes for a typical job.
At Villanova, George says the Quicksetter not only knocked hours off job times, but it freed up an employee to focus on other areas of the growing business.
"I used to have one person dedicated to prepress," he says. But since the purchase of the CTP system it hasn't been necessary to devote any employee exclusively to the operation of the Quicksetter.
Although CTP gets attention for the amount of time it saves, most managers say their platesetters save money on materials, as well.
As coordinator of graphic arts for Jackson Public Schools, Cindy Paxton says her highest priority is always saving money.
The Mississippi shop runs a Purup Eskofot [now Esko Graphics] DPX System. The shop acquired the platesetter two years ago. It all but eliminated the use of a dark room, she says, and the cost of prepress has since been cut in half.
"For one negative and one plate, you're going to pay $2.50 each," she says. "I'm not using it for every application, but the cost [of prepress materials] for most jobs has dropped from $5.00 to $2.50."
She says while the shop still uses film for higher-end jobs, she was nonetheless able to eliminate a staff position in the dark room.
Gerlinde Williams, administrator of Central Printing for the State of Oklahoma, is also very happy with the amount of money a platesetter has saved. The seven-employee Oklahoma City shop has been running an A.B.Dick DPM 2000 for several years.
"It eliminates the negative, it brings down the manpower and it saves a lot of time," says Williams.
Before purchasing the platesetter, the in-plant used an imagesetter exclusively. But Williams says she sat down one day to figure out just how much money the platesetter would trim off prepress overhead.
"I had all the savings figured out. We knew we would save money," she says. "And the savings were quite substantial."
In fact, Williams says after installing the platesetter, the shop was able to lower the price of offset jobs across the board.
Justifying The Cost
To get approval for the purchase of the Quicksetter, Villanova's George was subjected to a rather involved process.
"Villanova has an entrepreneurial society and a budget committee," he says. "I spent two months getting proposals from different vendors. I took that research to them, and they bought into it."
George says originally he wanted a five- to seven-year plan to pay for the device, but the university wanted it paid for in three.
No big deal, he says.
"So now we've got one more payment. And then it's ours."
Ken McKeel, manager of graphics at R.J. Reynolds Tobacco Company, also runs a Heidelberg platesetter. McKeel says getting into CTP was not even a question.
"Whether it gets justified or not, you're going to have to do it," he insists, explaining that his shop is trying to stay ahead of the curve when it comes to technology. McKeel contends the in-plant routinely saves up to 75 percent on prepress costs.
Williams says justifying the purchase of the platesetter to the state of Oklahoma was a breeze, considering the money it promised to save.
"I didn't have to do a lot of justification at all," she says.
The Trend-setting Platesetter
For those interested in going direct-to-plate, there are plenty of questions to ask vendors before buying.
"Make sure it fits all the presses in your shop," recommends Jackson's Paxton.
McKeel adds, "Get a platesetter based on the kinds of plates you're going to use. Different types of plates have different costs. Smaller in-plants really only need pre-baked plates."
Sooner or later, say these managers, every shop will have to engage with CTP at some level; it's a matter of time.
"Film is going to be a thing of the past," predicts McKeel.
.
Polyester: Cheap, Durable, Hip
Way down in Forsyth, Ga., Georgia Public Safety Training Center Printing Services supplies offset-printed manuals for 16 different state law enforcement and public safety agencies. The jobs account for 20 percent of the shop's workload, and Manager Gene Burke has been running Xanté platemakers along with the presses for eight years.
The Xanté 8200 Platemaker and PlateMaker 3 image polyester plates.
"We haven't used metal plates in a long time," he notes, referring to the days when his shop used a dark room.
Burke says the best reason to use polyester plates is the price.
"The polyester plates we use are something like 80 cents each. That's a little more than what you can get them for, but we want to stick with Xanté plates because if we need service we don't want them to be able to say the problem is 'You're using the wrong plates,' " he says.
Burke says metal plates are significantly more expensive than polyester plates.
"If you can get a metal plate for $1.50, you've done very well," he says. "Usually, they run anywhere from $1.75 to $2.50."
At Villanova University, polyester is the fashion, as well.
"We don't use metal plates," affirms Michael George, director of University Graphics. "That sort of system didn't fit within our budget."
He says the polyester plates are well-suited to the run lengths typical of his 13-employee in-plant.
"We do very little four-color. It's lots of stationery orders, brochures, stuff that is short-run. This is the best equipment for that sort of thing," he believes, adding that polyester plates are not designed for very long press runs.
Regardless of shorter run lengths, George says the shop is quite happy with polyester.
"We've pushed these plates to 20,000 impressions," reveals George.
Since going with a CTP system, George says the quality of the finished product has improved, as well.
"Going from a traditional negative, the quality is much sharper and much easier to read," he contends. "You don't have the same exposure fluctuations either."
And Gerlinde Williams, administrator of Central Printing for the State of Oklahoma, says there's an extra bonus to working with polyester plates.
"It's a one-time-use plate, which you can file in a computer," she says. "Metal plates have to get filed in an actual cabinet."
So in addition to money, labor and time, it seems polyester plates save space, as well.
.
Find Out More
A.B.Dick
|
www.abdick.com
|
Agfa
|
www.agfa.com
|
Creo
|
www.creo.com
|
ECRM Imaging Systems
|
www.ecrm.com
|
Escher-Grad Technologies
|
www.escher-grad.com
|
Esko-Graphics
|
www.esko-graphics.com
|
Fuji Photo Film U.S.A.
|
www.fujifilm.com
|
Heidelberg
|
www.heidelbergusa.com
|
Kodak Polychrome Graphics
|
www.kpgraphics.com
|
Mitsubishi Imaging
|
www.mitsubishiimaging.com
|
Presstek
|
www.presstek.com
|
Printware
|
www.printwareinc.com
|
RIPit Computer
|
www.ripit.com
|
Sakurai USA
|
www.sakurai.com
|
Screen (USA)
|
www.screenusa.com
|
Xanté
|
www.xante.com
|
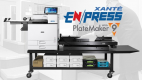




