Harlequin Takes a Novel Approach
With such best-selling romance authors as Debbie Macomber, Susan Wiggs and Sherryl Woods, Harlequin commands an awesome array of talent. The world's largest publisher of fiction romance novels publishes 130 million books annually in North America alone, all of this flowing through its 400,000-square-foot distribution center in Depew, N.Y.
To ensure inventory, Harlequin traditionally printed additional copies, millions of which never left its warehouse. In other cases, when demand exceeded supply, reprints took too long to produce on its vendor's offset presses.
"For some time we had been looking at ways to print some of our books digitally," says John Reindl, general manager of Harlequin's Distribution Center. "The technology finally got to a point where the digital printers could support the type of paper that we use. We wanted to mimic the print quality of offset so that the consumer would not notice the difference.
"We also wanted a solution that we could set up in our own distribution center," continues Reindl. "So our approach was to bring in digital printing to facilitate our short-run printing needs, which is anywhere from 500 to 4,000 copies of any one title to top off the main offset runs. But we still planned to outsource the bulk of our printing to our offset printer."
This vision was realized when Harlequin set up an in-house digital paperback book printing line. Designed by Jim Robinson, vice president of operations, and staffed by seven people over two shifts, the in-plant is able to print and finish more than 1,000 paperback books per hour. To print the books, Harlequin selected a high-volume Océ VarioStream continuous-feed printer, a toner-based solution that prints almost 10,000 books in an eight-hour shift.
"With 95 percent of our books in the same format, and few changeovers associated with our production process, we felt we could target a higher degree of automation and inline processing than we had seen elsewhere," Reindl adds.
The digital printer is not the limiting factor, however. Some of the finishing processes limit capacity, like the stacker that takes printed signatures and stacks them into book blocks.
Basically, after printing, the paper is cut and folded into 16-page signatures. These then go through a folder and stacker to create book blocks. Then these book blocks go to the Muller Martini Sigma Binder and into a Muller Martini Esprit three-knife trimmer before they exit as finished books.
An In-line Solution
"Many digital printers print the books and then do the finishing off-line," says Reindl. This eliminates the risk that downstream jams in folding, stacking, binding and cutting will impede the printing.
"We wanted to do it differently, with all of our production inline," says Reindl. "We needed a solution that would allow us to move book blocks from one part of the production process to another. But the book blocks are still loose signatures. The importance of getting the book blocks out of the folder and to the binder without the blocks tipping over, and maintaining their stability, was a critical part of the process. We searched and found only one solution that would allow us to do this."
The conveying solution that Harlequin embraced was a multi-faced, integrated conveying approach designed and built by Shuttleworth Inc., specifically for conveying cut-paper products. The design incorporated the following systems:
• Star Rollers: As the book blocks exit the stacker toward the binder they travel on a 15-foot long conveyor equipped with Star Rollers. These eliminate shingling or creeping of the bottom layers of paper when stacks are transported and accumulated on the conveyors. The star-shaped profile enables loose stacks of paper to be conveyed and accumulated between the stacker and the binder without disrupting the integrity of the stacks, because only the points of the star touch the stacks.
• Slip-Torque Conveyor Technology: This employs polished stainless steel shafts covered with segmented, loose-fit rollers, which form the conveyor surface. Slip-Torque provides the gentle handling needed for transporting Harlequin's book blocks from stacker to binder.
• Buffer Accumulation Conveyor: If the line is running normally, there will be no accumulation of book stacks on the conveyor. The stacks would flow through to a blade stop before entering the binder. But if the binder goes down, book stacks are diverted into a buffer conveyor, which can accept up to 85 stacks (five minutes worth of throughput), allowing enough time to dislodge the binder jam-up. Once the binder is cleared, the book stacks will automatically feed into the binder.
The buffer conveyor reduces total line delays by allowing the printer, folder and stacker to continue production for a cost-effective period of time when the binder is down. This gives greater productivity, and reduces product damage and operating time.
"We haven't had to use it much," says Reindl of the buffer conveyor, "but when we have had to, it has worked quite well."
With its streamlined digital printing and finishing capability, Harlequin can now cost-efficiently print and finish in-house whatever overages are needed above its initial offset runs for any title on a just-in-time production model. It can now also print and finish short runs for select titles that require, initially, very small quantities. Previously, these would have been sent out for offset printing with a minimum order of 5,000 required, even if only 3,500 copies were needed.
The new print and finish line has significantly improved Harlequin's inventory load, resulting in a 15 to 20 percent reduction in titles held in stock.
"The key value of the conveying system is that it supports our inline process, which is critical to the success of the system," says Reindl. "Our print and finish system would not have been possible if we did not have a solution that allowed us to maintain stable book blocks coming out of the stacker and going into the binder, and a back-up solution to keep the print and finish throughput operational in the event of binder malfunction." IPG



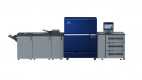

