Once but a dream, CTP has become an essential element at even small in-plants. Here's one manager's story.
By Jim Sabulski
Years ago I found it hard to believe I would see the day when everyone had a personal computer. Some time later, using the same logic, I doubted that all print shops were going to have computer-to-plate (CTP) systems. I thought it would be reserved for the large-format shops that could afford it. You see now why I am a printer and not a prognosticator.
Not unlike at many small in-plants, the majority of offset work produced in College Misericordia's in-plant is one- and two-color line work. For more than 12 years, metal plates were produced using diffusion transfer technology. Although the plates were capable of producing upwards of 50,000 impressions, consistent results were difficult to achieve, depending on the quality of the hard copy, the life of the developer and the exposure time settings.
Jobs that contained halftones, screens and/or tight two-color registration required film, which we would outsource. Conventional stripping of these negatives would follow, and we would burn negative-acting plates in-house on a small NuArc plate burner.
Then one day we were informed by our supplier that diffusion transfer plates and chemicals were becoming scarce and that a time would soon come when they were simply obsolete. Not only were we forced to find an alternative method of producing plates in-house but the clock was ticking.
Fortunately, manufacturers were offering small-format CTP options more so than ever before. Even so, the move to CTP was a cautious one. It didn't take much research, though, to realize that polyester CTP was our most affordable option.
Taking the Plunge
We asked several vendors to supply us with imaged plates that we could test on our presses. In 2004, after a number of experiments, we purchased a Kimosetter 340 from Kimoto Tech and its corresponding RIP. Influencing the decision most was a low startup cost (about $3500.00), an environmentally friendly chemical-free workflow and the fact that the unit uses a thermal transfer ribbon instead of toner to image the plate. This eliminated the problem of toner scatter during the imaging process and toner flaking while on the press.
For a short time we continued to use our diffusion transfer system while slowly incorporating Kimo plates into the workflow. The main reason for this was that often we did not have a digital file to work from or the file we had was not suitable for the platesetter. We pressed hard to digitize all existing files, and in no time metal was out and poly was in.
The unit paid for itself in less than one year. Currently, about 2,000 poly plates are being produced in-house annually at a cost of about $1.75 for a 13x19˝ plate. Compare this to diffusion transfer, which—after purchasing the plate, transfer film, developer, fixer and lacquer—was costing about $6.00 per plate. This doesn't include disposal of chemicals.
We did, however, produce 500 fewer of the DT metal plates because on repeat jobs they could be gummed and reused. Still, our in-house plate making costs went from $9,000 annually to $3,500. We have also decreased outsourced film costs because the 1,200 dpi/100 lpi the unit offers is adequate, in some instances, for jobs that contain halftones and screen work.
The unit is not without its disadvantages though. Plate stretch is a concern. We have eliminated it significantly by assuring proper ink and water form roller pressures and plate to blanket pressures. Also press operators must become familiar with hanging the plates as they cannot be clamped as tightly as their metal counterparts.
Although run lengths are quoted by the manufacturer to be between 3,000 and 5,000, we have achieved runs of 10,000 quality impressions. Again, press settings are crucial. The unit is not capable of angling screens so duo-tones, and process work is out of the question.
Perhaps the biggest issue is understanding the limitations of the machine. Because of its speed and convenience, on occasion, we have found ourselves trying to get more out of it than is possible. As we all know, some jobs simply require metal and for those we still outsource film.
In addition to the cost savings, the efficiency and ease of use is incredible. The unit will image a 13x19˝ plate in three to four minutes. It is then ready to be hung on the press.
Also, it is easier to make just-in-time decisions as to which press will be used to run a job. We have three small presses, a Hamada RS34II, a Hamada 660 and a Hamada 550, all requiring different size plates. Depending when jobs are needed, we can group like jobs and accommodate rush jobs easier because we can plate the jobs literally minutes before they go to press.
Moving into a Digital Workflow
Although the CTP unit will accept application files such as Pagemaker, InDesign, Illustrator, Photoshop and Quark, we prefer to utilize non application files such as PDF and EPS for the purpose of crossing platforms between our Mac and our PCs.
Our production artist creates PDFs from application files. She then sends the PDFs as soft proofs to the customer. As we are not producing full-color work on our presses, issues of critical color are often not a concern.
When the job is approved, she imposes as necessary and creates another PDF for the platesetter, color separated if applicable. Both of these files are then attached to the digital work order in our management software.
If a job is reordered she can pull a work order from history and see exactly what was printed the last time. If there are no changes, the same PDF is sent to the platesetter. Although we are far from what I would call a PDF workflow, we are beginning to take the first steps toward it.
Those of us who have been in the business long enough to witness the dramatic changes that technology has had on the industry wonder how we ever survived without a computer. Similarly, I now wonder, as I begin to convert our darkroom into my new office, how our in-plant survived without CTP.
.
Jim Sabulski has been Manager of Printing and Mailing Services at College Misericordia, in Dallas, Pa., for 14 years. His tenure in the graphic arts industry began at the age of 14, and he has never looked back. He holds a Bachelor of Arts degree in English and is currently pursuing a Masters of Science in Organizational Management. In June of this year he received his certification from IPMA as a Graphic Communications Manager. Jim Sabulski can be reached at:
jsabulsk@misericordia.edu
- Companies:
- Quark Inc.
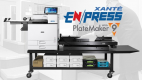




