Even as platesetters flourish, many in-plants are sticking with imagesetters. We asked several in-plants why they chose the imaging technology they use.
by Bob Neubauer
With so many printers turning to computer-to-plate technology, why are some in-plants sticking with imagesetters? We decided to ask a few managers. Providing their comments were:
Mike Schrader
-Printing & Publications Manager
-Mercury Marine
-Fond du Lac, Wis.
-15 in-plant employees
_________________
Dan Kovalsky
-Director Print & Digital Media Services
-Constellation Energy
-Baltimore, Md.
-22 in-plant employees
_________________
Charlie Tonoff
-Manager Corporate Printing Services
-Highmark
-Camp Hill, Pa.
-20 in-plant employees
_________________
Sticking With Film
Why have you chosen to stay with film instead of going direct to plate?
Mike Schrader: For the type of work that we do we have not been able to justify a platesetter.
Dan Kovalsky: We've always believed that CTP was a stepping stone to computer to press. The elimination of film is a big chunk of savings, therefore, we thought that we'd wait until press technology matured and then we would try and make a business case to upgrade to a digital press.
Charlie Tonoff: Direct to plate is still too costly for our operations, though we have decided to move into wide-format printing so we can output imposed, RIPed files as proofs instead of running film and stripping. This is a fairly inexpensive, but necessary step for CTP and adds value.
Have developments in on-press imaging factored into the decision?
Schrader: In the future we are planning on producing more four-color work. At that time we will be either migrating to a platesetter or a direct imaging press.
Kovalsky: Yes, quality has improved significantly. At this time, we are researching the technology by evaluating the capabilities of different machines. Concurrently, we are evaluating the corporate demand for short-run color (color copies, short run offset, etc.). Perhaps the biggest decision that we need to make is whether we purchase a toner-based or ink-based machine. By mid 2002, we'll perform a formal cost benefit analysis and present that to our leadership for review.
Tonoff: At this time no, though any new presses we may consider procuring, we will look at direct imaging.
What are some advantages of an imagesetter over a CTP device?
Schrader: Five years ago, price was the biggest factor.
Tonoff: Lower costs, even after considering process improvements. I can not think of any other advantages in today's market.
What ROI time frame or useful life expectancy are you budgeting for with your imagesetter?
Schrader: We needed under a two-year ROI, with a life expectancy of at least five years.
Kovalsky: We most often use five years as the target. However, our Agfa 7000 is eight years old and we hope to squeak another year.
Tonoff: We have had our imagesetter eight-plus years. It runs very well. We have no indications that parts will not be available any time in the foreseeable future, so I expect to continue to operate indefinitely. If something occurs that requires replacing the imagesetter, that would be a perfect time for CTP.
Have you considered imaging poly plates with your imagesetter?
Schrader: Yes, but the size is our limitation. We have four offset presses, and our current imagesetting device will only accommodate two of the plate sizes. We felt that it was not worth it to add another processor and have the hassle of constantly changing the material.
Kovalsky: We tried it. It worked fine for a few limited categories of work that we produce. Using the plates is viewed by prepress and press operators as more trouble than it's worth for our application.
Tonoff: Yes and no. Press operators want to continue running metal. They have a very high comfort level with that, as I also do. Much of our work is very tight registration and we have reservations [about] running two different plates and the potential problems inherent with that.
Do you have the digital workflow in place that's required to go CTP?
Schrader: Yes, we have been completely digital for at least three years now.
Kovalsky: We believe that we have the beginnings of a good workflow. About 11⁄2 years ago, we began an integrated effort to apply ICC Profiling as a standard across our shop. Mostly, this was done for training purposes and to better communicate color with our designers. While it takes a pointed effort on everyone's part, the results are surprisingly good and the entire staff is learning digital requirements. More currently, we are investigating PDF as a workflow solution.
Tonoff: No, our customers simply will not pay the additional cost to go CTP, even with the work sent externally.
Are you planning to look into CTP?
Schrader: We have already been looking into CTP. We have prepared a five-year plan and a CTP device is part of that plan, which includes producing four-color work that we do not currently produce. We are hoping to produce some of that work with our current equipment and prove we can satisfy our customers, then show upper management what savings could occur with certain equipment. We have not decided on aluminum plates or poly plates yet.
Tonoff: I will continue to look at and consider CTP.
Success With CTP
Many in-plants have done away with film entirely. Here's an inside look at how CTP is working at two in-plants at opposite ends of the country:
• Lisa D. Hoover
-Assistant Director of Admin. Services
-Bucknell University
-Lewisburg, Pa.
-23 in-plant employees
_________________
• Hal Cypert
-Duplicating Services Supervisor
-County of Tulare
-Visalia, Calif.
-15 in-plant employees
_________________
Why did you decide to go with CTP instead of an imagesetter?
Lisa D. Hoover: We have the A.B.Dick DPM 2340 platesetter. We felt that the type of work we produce was conducive to using CTP. We generally produce one- and two-color work. We were previously outputting film on our Lino 330. We still have our imagesetter, and it is used occasionally to produce film for jobs when film is requested.
Hal Cypert: We decided to go with the CTP over an imagesetter because of the reduction of steps in our process. Instead of outputting to paper or film we go straight to plate and avoid film assembly and the making of metal plates.
Until we purchased the CTP we would output copy using our plain paper printer and either make a negative (we made negs on jobs that had screens or tight registration) or a polyester plate using our platemaker if it was straight text copy. We have never owned an imagesetter.
What are some advantages of a computer-to-plate device over an imagesetter?
Hoover: Probably the biggest advantage of CTP is the time savings. Using CTP eliminates the need for imaging film, stripping and burning plates. In one simple step, the file is imaged directly on the plate.
Another advantage is quality. By saving the stripping/plate burning step, we've eliminated one generation of reproduction, which ultimately produces a cleaner, more accurate image. A third advantage is eliminating the need for plate filing and storage. The plate is used once and thrown away.
Cypert: We can get a job to press faster than with an imagesetter (because of the elimination of steps), and we have reduced costs. We have stopped purchasing film and metal plates and solely rely on polyester plates.
Did going CTP cut costs for you?
Hoover: Using CTP does cut costs. The cost for one 8 mil polyester plate is significantly less than the combined cost of imaging film, stripping and metal plate costs that are incurred when producing a job using the traditional method.
Cypert: Savings come from the elimination of film and metal plate purchases, hauling away of spent developer and fix, and labor savings from the eliminated prepress steps and errors that were made.
What changes did you have to make to your workflow when adding CTP?
Hoover: The workflow did change a bit because the prepress technicians/designers are sending files directly to the DPM 2340. Since most of those operators did not have a stripping background, there was a bit of a learning curve about how to arrange files for work and turn, imposition, etc.
Cypert: Since the addition of our CTP, our workflow has been streamlined from the elimination of prepress functions that we used to perform. We have noticed a remarkable improvement in halftone and screen printing quality. Overall we have noticed shortened production time required on jobs since we have purchased our CTP because we are getting jobs to press much quicker and with fewer mistakes.
How have your press operators reacted to the switch from metal to poly plates?
Hoover: Our press operators have had only good things to say about the polyester plates. They did not have any problems making the transition.
How are you handling proofing?
Hoover: We currently are using a soft monitor proof. The press operators view all RIPed files before they are imaged to a plate. Then they compare what they see on the monitor with a dummy that is supplied by the prepress technicians. Although this sounds like a risky method, it has worked fine for us.
Cypert: We proof off of a plain white paper print prior to making plates. On new jobs this is what our customers give us an O.K. with. After that, we use this to flip check the plates after they have been made to ensure that we did not lose any data. We have established files on the CTP hard drive to store jobs that repeat.
_________________
Points To Consider These insights were provided by Mark Vanover, of Creo Americas, Jeff Hopkins, of basysPrint, and Marc Johnson, of Presstek. • Purchasing an imagesetter allows an in-plant to get familiar with a digital workflow prior to going CTP. • Some vendors let users trade imagesetters in for for platesetters. • By eliminating multiple steps, platesetters allow in-plants to get work plated on on the press in less time. • Because CTP platemaking eliminates the whole filmmaking and handling process, labor is reduced. • The up-front costs of the chemistry itself, disposal costs, processor maintenance time and materials are eliminated. • By eliminating chemistry, CTP is a more environmentally friendly solution. • Last minute corrections can occur in tighter time frames. • Plates do not have to remade because of bad stripping, mishandling within in the film imaging process or hot spots created by film. • Plates imaged digitally are in perfect register. CTP produces a sharper dot with crisper text. • The total floor space required for CTP is usually smaller than the existing imagesetter and processor. • The in-plant that has a full size imagesetter has already made the digital transition and only needs to send the RIPed file to the CTP device versus the imagesetter. Facility modification to the electrical and air supplies are typically modest.
|
- Companies:
- Agfa Graphics
- Presstek Inc.
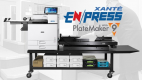




