As you evaluate new digital printer platforms, take a careful look inside the box.
Is the quality of digital networked printers as good as it's going to get? Not at all. The newest generation of printers is approaching image quality in a new way.
To date, digital platforms have offered in-plants limited quality improvements over their optical predecessors. That's because most existing digital print platforms retain many of the same imaging components and processes used in optical devices.
Since optical and digital devices approach the imaging process from different perspectives, the technology needs to be tailored to the process. Conventional optical toner/developer and photoconductors erase all of the non-image area on the page, charging only the image area.
However, digital devices can produce much better quality with an imaging process that exposes only the image area. When lasers are asked to chisel out all the charge around characters and dots to produce the desired image, thin lines are often lost, and lines that run from the top to the bottom of the page (cross-track) typically are wider than those that run from side to side (in-track). Dot definition and edge quality can also suffer.
As you evaluate new digital printer platforms, look for one with newly designed toner, developer and other components and a process that directly exposes the image area. Advancements in LED writers significantly improve dot definition and uniformity. New technologies also promote edge definition and smoothness.
Kodak and Heidelberg debuted several digital imaging technologies in the Heidelberg Digimaster 9110 network imaging system. In-plant managers report that the platform's image quality is attracting attention from their internal customers. One shop manager said it takes just one sample for his customers to request that "the new printer" handle his department's work from now on.
Portland Print Shop
The City of Portland's printing and distribution facility recently installed a Digimaster 9110. Production Manager Lou Reiniger notes that the image quality is "exceptional" and cites a host of applications where these quality gains are appreciated.
"This new system produces consistent and even coverage in solid areas. And it excels at holding a sharp edge on extremely fine lines. That's especially important in service and operations manuals that contain engineering drawings and schematic diagrams," he notes. He adds that engineering drawings are often reduced to 11x17˝ and Z-folded into the bid specifications.
In addition, Reiniger values the device's ability to hold a screen and to produce sharpness and depth in black-and-white halftones.
Lengthy bid specification books include black-and-white photographs and maps with screened areas for differentiation. Newsletters and other publications also contain photographic images.
"These images really look sharp and crisp," he notes, "In the past, we had to go to press to get this kind of quality. Now it's available on a networked device that can produce more than 100 pages a minute. This capability makes it much easier to meet our aggressive deadlines."
Reiniger's print shop runs three shifts 24 hours a day and offers "in by 6 p.m. and out by 6 a.m." service on many jobs. He says that offering rapid service and unsurpassed image quality is essential to the shop's survival.
"We operate as a separate business, so we are not subsidized by city funds," he explains. He says that competitive pressure is intense because the city periodically compares the capabilities and pricing of Reiniger's facility with outside vendors.
"We have always come out on top in terms of both quality and service, which is why we are still here. But we can't stay on top with old technology. We are always looking for products that equip us to improve image quality and productivity."
Technical Details
If you are wondering how this new printer platform works its magic, the answer is in the technical details. Its advanced LED writer works in combination with a new discharged area development process known as DAD to create precise line and dot definition. It exposes an entire line at the same time, at a fixed focal length from the photoconductor. Dots and lines are symmetrical in both in-track and cross-track directions.
Halftone and screen images offer unsurpassed sharpness and definition thanks to an enhanced LED writer that provides 256 levels of overall writer brightness and 64 levels of individual LED brightness.
Edge sharpness is also enhanced by Kodak's Gray Resolution Enhancement Technology (GRET), which further enables the print head to print gray levels on the photoconductive image loop. The print head can produce 15 distinct exposure levels. The resulting dot size can be made incrementally smaller than the D-max black dot the printer would otherwise use to build images.
GRET technology applies variable dot size to produce a smoother line than is normally possible. An algorithm searches image content and adds smaller gray pixels to the line or text to create a smoother edge—while maintaining maximum throughput.
The printer calibrates itself at start up and recalibrates after six hours of operation. This process involves mapping the entire photoconductive image loop, and taking more than 500 individual measurements—in 1.5 seconds.
The print engine's logic and control unit computer performs adjustments based, in part, on input from two monitoring devices. A vibrating reed electrostatic voltage potentiometer monitors the charge level on the photoconductive image loop, while an infrared logarithmic transmission densitometer measures the mass of the toner developed on the loop. System adjustments produce consistent density in solid areas, while maintaining sharpness in line edges and halftone dots.
Since this process control system continuously monitors and adjusts variables, the need for manual quality checks is eliminated. Customers can manually override the system if desired.
Freshly designed digital printing platforms offer noticeable gains in quality and efficiency. These capabilities can ensure that internal customers and corporate executives appreciate the convenience and value offered by an in-plant facility.
Sam Errigo is vice president of digital marketing for Danka Office Imaging. You can contact him at: sam_errigo@danka.com.



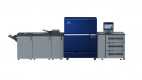

