One large digital press in an in-plant is impressive. Two of them in the same shop is remarkable. But three is extraordinary. So when Medifast, a clinically proven, portion-controlled weight-loss program, installed a third Xerox iGen4 in its Ridgely, Md.-based in-plant in January, the in-plant entered the realm of the exceptional.
“The company is growing by leaps and bounds,” reports Larry McCord, senior supervisor at MDC. “A third iGen4 was needed.”
Medifast’s growth has brought a huge increase in work to the 14-employee in-plant, called the Medifast Distribution Center (MDC). The company added a second distribution center in Coppell, Texas last year to handle the needs of the West Coast, but 95 percent of the company’s printing needs are still handled by the in-plant.
MDC prints all in-house mailers, booklets, brochures and flyers and handles up to 250,000 pieces of variable data printing each month. About 10 percent of its work is insourced from companies around the region.
“We are taking off like a rocket,” says Kent Hunter, second shift supervisor. “In our region we are [Xerox’s] number one click generator. And we are their number one customer.”
In a remarkable shrugging off of market conditions, Medifast’s in-plant defied the recession and instead grew in size—which, if you ask the editors at Forbes, isn’t surprising. In 2008 Medifast was ranked 85th on Forbes’ list of “America’s 100 Best Small Companies.” It rose to 16th in 2009, and in 2010, it shed off any doubts about its potential and became number one.
“We sat out the recession and decided not to buy a ticket,” quips Patty Neubaum, morning shift supervisor. “If anything, we felt growing pains.”
As its overall volume has increased, so has MDC’s insourcing volume, Hunter says.
“We have added several clients and our reputation as an inexpensive, high-quality printer has spread throughout the Eastern Shore,” he reports.
The iGen4 offers several advantages over the iGen3, according to Neubaum. The in-plant receives big savings from not having to have to change the developer as often as on the iGen3, she says. On the iGen3 you would have to change at every 50,000 prints.
“With the iGen4 it is at 750,000 prints,” she says.
The carrier dispensing system allows the shop to save even more developer, she adds. These savings, of course, are passed along to the parent company.
Hunter calls the iGen4 a “work horse” and says that “you can put anything through them.”
Larry McCord, MDC senior supervisor, explains that Medifast has had a long relationship with Xerox. This partnership made the decision to add a third iGen4 easy.
McCord feels the future is bright for the in-plant. Business is so good that the shop plans to add even more equipment soon.
“Now, we are looking at the back end of the in-plant, at the bindery,” hints McCord.
Related story: Losing Weight Is A Growing Business



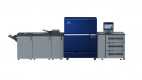

