You can avoid printing pitfalls by paying more attention to how you handle your paper. Follow these tips.
by Dennis Davey
Following a few rules of thumb for paper handling and usage can significantly impact document quality and press operation. Here are some tips:
Streamline Workflow
One simple workflow rule is "First In, First Out." When paper arrives in a warehouse, the first paper to go in should be the first paper printed. This will prevent paper from aging in the back of a warehouse because it is blocked by more recent shipments.
Paper damaged from improper storage can erode print quality and even damage equipment. "First In, First Out" ensures that all paper will be warehoused minimally, resulting in uniform quality as it goes into production. Implementing this policy is a simple, economical workflow strategy to deliver more consistent paper and maximize production rates and document quality while minimizing waste.
Protect Paper During Production
Store paper in its protective wrapping or covering throughout the entire document production process. Pallets of printed pages should not sit unprotected on a print shop floor for hours before running them through the bindery.
Equally important, offset printed forms should not sit unprotected before being digitally personalized. A loose plastic sheet should suffice to protect the paper from dust and scuffs. If paper is left unprotected in a print production environment, even for brief periods of time, it is exposed to dust and moisture that erode document quality.
Paper should be protected during longer periods of storage, as well. Unprotected paper will equilibrate to the environment, so any extremes should be avoided. High humidity, for example, will cause it to take on moisture and curl at the edges. Excess dryness will cause it to lose moisture and become tight at the edges and brittle.
Such conditions can result in print registration and wrinkling problems on offset presses, as well as image deletion problems on digital printers. To ensure optimal performance, store paper under temperature- and humidity-controlled conditions that approximate the environment in which it will be utilized.
Acclimate Paper
Moving paper from location to location can result in humidity and/or temperature changes affecting print performance and quality. If paper has been stored in a non-temperature-controlled environment, it should be brought to a staging area inside the in-plant and allowed to acclimate.
Acclimation time varies according to roll or case size, temperature and humidity (see charts). For example, paper that is kept in an unheated warehouse during winter should be allowed to acclimate while in the original packaging material in the heated pressroom.
It is equally important to consider climate changes during transportation. Paper may endure severe temperature changes even in the short distance from an in-house warehouse to the printing floor. Acclimating paper after it travels will result in optimal press performance and print quality.
Retain Tracking Information
Keeping proper identification with unused paper and printed documents throughout the entire production process is essential. Printed documents can go through many forms of conversion after their initial run: everything from form conversion to digital printing. Keeping identification—such as product, grade and lot numbers—on a ticket attached to documents throughout the entire process is key. This will enable easy identification and troubleshooting if any problems are encountered down the line.
Using this information, paper mills can track problems and troubleshoot technical issues quickly and efficiently for the printer and its customers. Georgia-Pacific, for example, has implemented a system within its customer service center to quickly track product lots and resolve problems.
Match Paper With Application
A printer that is strictly offset may still need to use paper specially engineered for digital printing. Many applications, such as transactional statements and forms, are later digitally customized. For these documents, it is necessary to use paper designed for both digital and offset printing to ensure high quality for the end user. Paper such as GP's Spectrum Multi-System, which runs in a variety of environments, is ideal for cross-platform applications.
Digital printing for personalization has become common in the printing industry. Considering the entire life of a document will help you choose the paper that offers the best runnability and quality in all the printing environments it will encounter.
A few up-front precautions in paper selection, storage and handling can go a long way to ensure trouble-free performance throughout the life of the document.
Acclimation Times
Paper in Rolls
|
|
Difference in Warehouse and Pressroom Temperature
| |||||||
|
|
10
|
15
|
20
|
25
|
30
|
40
|
50
|
60
|
30˝ Diameter
|
40˝ Diameter
|
Paper should stand, unopened for:
| |||||||
15˝ wide
|
8˝wide
|
5 hrs.
|
9hrs.
|
12 hrs.
|
15 hrs.
|
18 hrs.
|
25 hrs.
|
35 hrs.
|
54 hrs.
|
30˝ wide
|
16˝ wide
|
8 hrs.
|
14 hrs.
|
18 hrs.
|
22 hrs.
|
27 hrs.
|
38 hrs.
|
51 hrs.
|
78 hrs.
|
60˝ wide
|
32˝ wide
|
11 hrs.
|
18 hrs.
|
23 hrs.
|
28 hrs.
|
35 hrs.
|
48 hrs.
|
67 hrs.
|
100 hrs.
|
|
64˝ wide
|
14 hrs.
|
19 hrs.
|
26 hrs.
|
32 hrs.
|
38 hrs.
|
54 hrs.
|
75 hrs.
|
109 hrs.
|
Paper in Cases or on Skids
|
|
Difference in Warehouse and Pressroom Temperature
| |||||||
|
|
10
|
15
|
20
|
25
|
30
|
40
|
50
|
60
|
Cubic Volume of Paper:
|
|
Paper should stand, unopened for:
| |||||||
6 Cubic Feet
|
|
5 hrs.
|
9 hrs.
|
12 hrs.
|
15 hrs.
|
18 hrs.
|
25 hrs.
|
35 hrs.
|
54 hrs.
|
12 Cubic Feet
|
|
8 hrs.
|
14 hrs.
|
18 hrs.
|
22 hrs.
|
27 hrs.
|
38 hrs.
|
51 hrs.
|
78 hrs.
|
24 Cubic Feet
|
|
11 hrs.
|
18 hrs.
|
23 hrs.
|
28 hrs.
|
35 hrs.
|
48 hrs.
|
67 hrs.
|
100 hrs.
|
48 Cubic Feet
|
|
14 hrs.
|
19 hrs.
|
26 hrs.
|
32 hrs.
|
38 hrs.
|
54 hrs.
|
75 hrs.
|
109 hrs.
|
96 Cubic Feet
|
|
15 hrs.
|
20 hrs.
|
27 hrs.
|
34 hrs.
|
41 hrs.
|
57 hrs.
|
79 hrs.
|
115 hrs.
|
Paper in Cases or on Skids Difference in Warehouse and Pressroom Temperature
10 15 20 25 30 40 50 60
Cubic Volume of Paper: Paper should stand, unopened for:
6 Cubic Feet 5 hrs. 9 hrs. 12 hrs. 15 hrs. 18 hrs. 25 hrs. 35 hrs. 54 hrs.
12 Cubic Feet 8 hrs. 14 hrs. 18 hrs. 22 hrs. 27 hrs. 38 hrs. 51 hrs. 78 hrs.
24 Cubic Feet 11 hrs. 18 hrs. 23 hrs. 28 hrs. 35 hrs. 48 hrs. 67 hrs. 100 hrs.
48 Cubic Feet 14 hrs. 19 hrs. 26 hrs. 32 hrs. 38 hrs. 54 hrs. 75 hrs. 109 hrs.
96 Cubic Feet 15 hrs. 20 hrs. 27 hrs. 34 hrs. 41 hrs. 57 hrs. 79 hrs. 115 hrs.
- Companies:
- Georgia-Pacific
- People:
- Dennis Davey Following
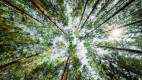


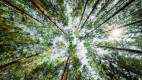
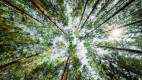
