People like their laser printers—a bit too much. Convincing them to use your in-plant instead is one of your biggest challenges as a manager.
Like the "Doggie in the Window" Patti Page longed for in her 1953 song, laser printers are the cuddly friend everybody wants in today's office environments. Whether it's a handy-dandy personal printer next to someone's workstation, a networked printer or small digital copier serving an entire office, people crave the convenience of a laser printer.
But laser printers are being abused. By overusing them, people are incurring huge costs for their parent organizations and taking big chunks out of today's shrinking budgets.
One of the biggest challenges to an in-plant manager is not only providing cost-effective solutions for digital printing needs within the organization, but actually convincing people in the organization that you are a beneficial solution.
For most people, the convenience of printing locally overrides cost considerations, especially when it comes to multiple "copies" or documents over one hundred pages. This convenience factor often clouds fiscally responsible judgment.
Most people don't consider the true cost of that particular convenience. On average, laser printers range from $1,000 to $5,000 and generally print from four to 12 pages per minute. During the lifetime of a laser printer, a duty cycle of 10,000 pages per month is not uncommon.
When considering the cost of laser printers and small digital copiers, one common mistake is the casual omission of a major expense: the labor to produce and finish copies.
Not only does someone have to monitor the printing of the job and load the paper, but there's often hand collating required, plus stapling, inserting, punching, folding and cutting. The in-plant can efficiently perform these tasks for minor and major projects. High-speed printers perform many of these tasks automatically.
Staggering Costs
The costs of laser printers can be staggering to the average user. The amortized cost of the equipment for five years, along with paper and toner, can be as low as 6¢ per page to as high as 17¢ per page, depending on the brand and model number. Add into that the labor cost to print out even 500 pages with just loading and unloading of paper, and the average cost is around 10¢ each. In comparison, institutional printing centers, on average, offer copies for around 3¢ each.
(The costs cited above are based on the National Average Statistics compiled by Hanson's Buyers guide in 1998. The average toner per page of 17 percent is based on a study conducted in 1994.)
While this may sound like pennies, the accumulated total can be from tens to hundreds of thousands of dollars, which could be put to better use by the parent organization.
A $30 Instruction Book?
A simplistic example of the achievable savings can be illustrated by the fact that many software packages no longer come with instruction manuals. They are now included in the help menu of the software itself. People still prefer to have a hard copy by their desks for easy reference. So what do they do?
They print an entire 300-page manual out on their laser printer. In other words, they spend an extra $30.00 to print the manual that used to come included with their software. (Funny, the software companies sure don't seem to pass those savings on to the users.) A printing center can usually run the same manual for approximately $10.00—complete with binding.
There are, of course, people who are aware and concerned about the costs of these small printers and will routinely go over to the office copier to run additional copies of their laser-printed original. This too, can cost more than most people realize. True, printing to a small office copier is less costly than a laser printer, but it's still more than printing centers charge—labor and all.
And then there are quality concerns. Designing a nice brochure or newsletter and printing out an original on a quality laser printer, only to degrade it by running the job on a traditional copier, has, for many, been the trade-off between cost and quality.
Even new generation digital copiers, which are slightly more cost effective, can have similar costs to that of a good laser printer. According to Danka Office Imaging, costs usually range from 4¢ to 7.5¢ per page, with the average being about 6¢ based on a usage rate of 10,000 copies per month.
Mail merging and other personalization helps document creators reduce separate addressing and imprinting steps. Many institutions have moved from the centralized data center model to that of a client-server model. This shifts the ability and often the responsibility of printing documents from data centers to office personnel.
Printing documents very slowly on the departmental equipment either dedicates or ties up, depending on your viewpoint, the office printer. Some offices have even resorted to "clustering," or dividing up the work to multiple printers on their network. This sometimes "dedicates" every printer in the office for hours or days on one project. An eight-page-per-minute printer will take more than six hours to print three thousand letters. That's assuming there are no glitches.
In-plants Reduce Costs
Costs can be reduced dramatically by sending this work to the in-plant. The time it takes for a 100-ppm printer to run 3,000 pages is only half an hour or less—sometimes dramatically less. Since the cost savings can be 50 percent or more of the operating expense of a small printer alone, the value of the in-plant with regard to both time and money is indisputable.
As technology has changed, many in-plant printing centers have come to the rescue with a complete menu of services. This includes an arsenal of networked, high-speed black-and-white and color digital copier/printers integrated with complete finishing and distribution capabilities.
With current technology it's easier than ever to send print-ready files over a variety of transmission protocols with the ease of pressing the "print" or "send" button. E-mail, FTP, TCP-IP, and direct T-1 connections to centralized printers are all applicable for specific situations.
In-plants not only produce less expensive copies, but also provide a variety of in-line services. High-speed printers can produce 100 copies a minute or more and simultaneously collate and staple, offset-stack, insert separator sheets, print tabs and so on. These features reduce labor costs dramatically, and these savings can be passed on to the customer.
Additionally, by offering free pickup and delivery of jobs, and encouraging digital submission, in-plants make it easy for customers to get their jobs printed. By using in-plants for their medium and long runs, people can extend the lives of their laser printers and save their parent organizations money.
by VIC BARKIN
Vic Nathan Barkin is the Printing and Reproductions Manager for Northern Arizona University. He has more than 20 years of experience in the printing industry, including seven years at Northland Press book publishers and seven years at NAU. In 1995 Vic received a Customer Service Excellence award from the Society of Service Professionals in Printing, and in 1998, Vic obtained his certification from the International Publishing Management Association as a Certified Graphic Communications Manager. You can contact him at: Victor.Barkin@nau.edu.
- Companies:
- Danka
- People:
- Patti Page

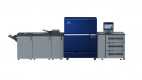



