
Mary K. Schilling, president of Schilling Inkjet Consulting, spoke about trends in inkjet paper at the 2018 Inkjet Summit.
With interest in production inkjet printing surging across all sectors of the industry, it’s a good idea to take stock (pun intended) of the substrates that will — and in some cases will not — work with the process.
Paper is paper, and making sheets and rolls for production inkjet presses isn’t radically different from making them for conventional equipment. Where the two types part company is in their respective interactions with machines and ink: a distinction that has given rise to new types of inkjet papers and a better understanding of how to print successfully with them.
Before there were inkjet papers, there were offset papers, and running the latter on inkjet presses is sometimes possible — but seldom with top-quality results.
Spraying low-viscosity, water-based inkjet ink onto the “naked freesheet” most uncoated offset paper consists of can be compared to “putting colored water on a sponge,” points out Mary Schilling, president of Schilling Inkjet Consulting. Fibers that are unable to “grasp the pigment” leave little of it on the surface of the sheet, reducing reflectivity and compromising the appearance of color.
‘Unintended Consequence’
The opposite problem arises with coated offset papers, which are too non-porous to allow the proper amount of inkjet ink absorption to occur. This, according to Marco Boer, VP of IT Strategies and conference chair of the annual Inkjet Summit, is an “unintended consequence” of using coatings to make up for the shortcomings of the less expensive pulps that paper manufacturers have sometimes resorted to in order to save money.
Offset stocks and inkjet inks can grow friendlier with the help of pretreatment fluids applied to the surface of the paper before printing. The fluids, which essentially are saline solutions, improve pigment holdout and aid drying.
When they’re correctly matched with the ink, says David Zwang, principal consultant of Zwang & Co., “they work really well” — and not only on offset papers. He recently saw a hybrid flexo/inkjet application in which a binding agent laid down before the ink made it possible to jet successfully onto plastic.
Nevertheless, Zwang adds, it’s a misconception to assume that just because a paper has been pretreated, it will work with a given production inkjet printing press unless the press manufacturer has qualified the paper as suitable for its equipment.
“There is still a lot of art to this,” Boer insists, noting that while pretreatment fluids are mostly similar, the porosities and surface tensions of the papers they’re applied to can vary considerably.
Paging Duncan Hines?
Papers manufactured specifically as inkjet grades are either treated or coated with substances that make them better at catching and holding jetted pigments. Treating puts the additives “on the cake batter,” as Schilling describes the wet pulp slurry of papermaking, during the manufacturing sequence. Coating introduces the additives separately, after the paper is fully formed.
There’s a tradeoff of price and quality between the two methods, with treated papers being more economical (because providing the additives doesn’t require an extra manufacturing step) and coated papers superior in printed appearance (because the coating helps the pigment to stand out higher on the surface).
Another way to make paper inkjet-compatible is to calender it — a technique employed in offset papermaking for decades. As a final step, the paper runs through a series of polishing rollers under pressure and at high speed: a process, according to Schiller, that “quickly and aggressively gets rid of all those hairs” (i.e., paper fibers that roughen the sheet and degrade printability).
“The surface of the paper is just as important as the chemistry and the treatment of the paper,” she says.
By calendering a stock, “you’re basically sandpapering it,” Zwang observes. The result is a smoother, more light-reflective paper that also resists the sponging of wet ink from over-
absorption. Boer notes that although the calendering step adds cost, inkjet papers made in this way tend to be less expensive than coated options.
However it is manufactured, paper is only one leg of the stool that inkjet print production rests upon. Ink characteristics and machine performance are as critical to outcomes as substrate composition, although the paper tends to carry an undue share of the responsibility for assuring success (and of the blame when the quality of the printing falls short).
A Case of Simple Physics
With ink, says Schilling, “it comes down to physics.” Everyone wants inkjet printing to be “faster, faster, faster,” but to accomplish this, the inks have to be made thinner so they can be jetted at higher speeds. Having thinner ink means using less colorant, and reducing the colorant has a predictable effect on the vibrancy of the color.
There is a ceiling here, as well. An inkjet ink containing more than the standard amount of 10% colorant would be too viscous to jet reliably, according to Boer.
What’s more, ink formulations have to correspond to the requirements of individual inkjet printing presses. It means, says Schilling, that “every single machine is a different ink” and no such thing as a generic inkjet ink exists. The inherent variation is why inkjet press vendors put effort into “tuning” the right combinations of paper, ink and equipment, points out Zwang.
As the offset world knows, choosing substrates always depends upon the product being printed, with some applications enjoying more options than others.
Boer notes, for example, that transactional printing and books do well on the uncoated inkjet papers that have been available for the last 10 years. With their higher quality requirements, direct mail and commercial work need coated stocks — but “the history just isn’t there yet” to assess the performance of these inkjet papers, according to Boer.
Keep ink coverage in mind as well, advises Zwang. A transactional document with 10% to 20% coverage won’t have the same issues of absorption as direct mail or commercial jobs where the minimum coverage might be 40% or 50%. Remember also, Schilling adds, that long-established standards of quality from offset production are still in force and can be applied to anything printed on inkjet paper with an inkjet press.
With their instant curing, UV inkjet presses open up the range of paper choices by eliminating problems of drying and absorption. But UV inkjet inks, Schilling says, are more expensive than non-UV inks, and are tougher on printheads and slower to jet. Boer agrees that while UV is a plus for inkjet papers, “at the end of the day, there is no free lunch.”
Can the Price Gap Be Bridged?
That fact of life becomes clear to anyone who compares the price of inkjet paper to the price of offset paper and sees the breadth of the gap between them.
Boer broadly estimates that inkjet papers are 20% to 30% more expensive than offset grades — down from as much as 50% higher five years ago. This is principally because capacity reductions from mill closures have driven the price of offset paper up while inkjet paper prices have declined. Boer thinks that at some point, “it’s possible that you might reach parity” between them, but not anytime soon.
Schilling is more conservative. For the offset mills that remain, she says, “commodity paper is still the king,” with inkjet papers representing just “a tiny, tiny part” of what they’re producing. To make inkjet paper, moreover, they have to “cook and clean up differently” from their offset papermaking processes, adding expense and disincentivizing additional production.
Schilling believes that for these reasons, narrowing the inkjet-offset price gap is at an impasse for now. Zwang’s take is that, as offset print volumes decline, the mills will try to replace the lost output by making more inkjet paper — a positive development for availability and price.
One thing that the mills and the inkjet printing community do know, Zwang says, is that there is no single inkjet paper to satisfy all requirements. That awareness inspires ink makers and the press vendors to do their bit for better paper performance — a sharing of responsibility Zwang sees as fair.
“Putting the full onus on the paper mills is misplaced,” he points out.
Predicting where the inkjet paper market goes from here depends on whether the forecast is short- or long-term.
Right now, according to Schilling, consolidation and constrained supply are driving prices up, increasing lead times for orders and making mills and merchants less inclined to offer contract pricing. Meanwhile, as more cut-sheet and continuous-feed inkjet presses come online, a potential conflict of demands arises: Where’s the paper going to come from? And is the state of the market going to slow down machine sales?
Zwang agrees that while the mills are “running as fast as they can,” there are limits on what they can do to ease the present pinch. Boer encourages looking ahead to when, “20 or 30 years from now, inkjet papers could be the standard papers” thanks to the widespread adoption of production inkjet printing.
“At the end of the day, inkjet will become the predominant process,” he declares. “It’s just a matter of time.”

Patrick Henry is the director of Liberty or Death Communications. He is also a former Senior Editor at NAPCO Media and long time industry veteran.


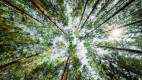


