Whether it's for the environmental benefits or the cost and time savings, an increasing number of in-plants are installing computer-to-plate systems.
By Carol Brzozowski
With a year of computer-to-plate (CTP) experience under its belt, Arkansas State University's in-plant has no desire to ever go back to film.
"It's probably one of the best investments we've ever made here," says Director David Maloch of his shop's Heidelberg Prosetter 74.
That's what an increasing number of in-plants are discovering. According to an In-Plant Graphics survey, 34.7 percent of in-plants have installed CTP—and the number is growing.
The environmental benefit is one of the prime reasons.
"That drives a lot of stuff in the college/university market," notes Art Larsen, director of the University of Maine Printing and Mailing Services in Orano, Maine.
In September, his operation installed a Presstek Dimension 800 with Anthem chemistry-free thermal plates to augment its "soup-to-nuts" operation. The in-plant's 36 employees do under $2 million in billing annually for the university system through an extensive pressroom that features a print-on-demand area.
In his funding request, Larsen outlined the chemistry expenses and how CTP would pay for itself in two to three years through money saved by not buying chemicals.
Eliminating Chemical Costs
With CTP, 400 gallons of developer and fix for film and platemaking has been eliminated, he says. Additionally, the operation has seen a reduction in production time and material costs and a greater accuracy over manual stripping, Larsen notes.
Following a three-day installation, a two-week learning curve ended with the operation removing its imagesetters and taking out the plate processor. Larsen has noticed a decrease in the time it takes to get plates out.
"My strippers were telling me one typical job would take them two to three hours, and it's now taking less than 20 minutes to get plates out once the digital files are transferred over to them," he enthuses.
Proofing is being done on an HP5000 or Xerox 6060.
Larsen says the Dimension 800 was chosen because it was the only one that could handle the various-sized presses while being chemical-free without light-sensitive issues.
Larsen likens the switch to CTP to the transition to cold type from linotype.
"The old linotype operators were probably a little disgruntled and didn't believe it was going to work, but lo and behold, here we are," he says. "The newer technology is neat, and we end up with a better product at the end."
Poly Plates Prove Trustworthy
Time savings has been an important benefit of going CTP for Robert Mettee, who manages in-house printing for the Boy Scouts of America, in Irving, Texas.
Six years ago, the nine-employee shop purchased a Mitsubishi DPX 460. Mettee used to outsource stripping and platemaking, and the one company in town that did it was so bogged down in work, the materials weren't always on time.
Mettee was reticent about CTP since his operation deals with four-color process and couldn't afford systems that did metal plates.
"Mitsubishi came in with the polyester plate and said it wouldn't stretch that much for short-run four-color process," Mettee recalls.
A Dallas printer that used the system produced plates for him and tested them at his operation. Mitsubishi's claims were confirmed for Mettee.
He then had to sell the idea to upper management. Mettee estimated the machine would pay for itself in three years; in reality, it was two.
CTP has allowed the shop to go from a week to get a job ready for press down to 10 minutes to paginate and output a job. Additionally, it cut the need for a stripper.
"The pressmen grab the file on a RIP and release it and walk away, and in a couple of minutes come back and get their plates and then hang them on the press," Mettee says.
Plus, there's less makeready. The Mitsubishi is calibrated for the presses, so an operator having a problem with a plate can just make a new one, hang it on a press, "and it will fall right into register, and they can take off running again," Mettee says.
Proofing is done with an Epson 3000 connected to the RIP, which replaces the blueline.
Mettee says getting the press operators used to polyester plates was the biggest hurdle.
"Every time they got a halfway decent long run, they wanted metal plates, and it took a little longer to get them over the curve to realize that poly plates were going to last a long time; they weren't going to stretch that much," Mettee says. "When they do stretch, it's just as easy to output another one and put it on, but it's very rare. If they put on a 100,000 run, then they have to make several plates. But for 10,000 and under, plates hold up fine."
'It Made Economical Sense'
A broken imagesetter forced the Printing Services department at Arkansas State University to make a decision: replace it or migrate to newer CTP technologies."With film savings and other issues, it made economical sense to go to computer-to-plate," says David Maloch, director of the nine-employee operation. "We presented a package to the administration, explaining the money we would save on film, the faster output, the more efficient operation and the quality issues. They thought it was a great choice."
The in-plant added a Heidelberg Prosetter 74 with violet laser and metal plates more than a year ago.
Maloch says the technology offers the ability to get plates to the press quicker, important in an operation that receives a student newspaper job in the morning to be printed by the afternoon.
The major benefit realized from the CTP investment is in workflow, Maloch says.
"Not only can we get plates ready for press quicker, we can generate a proof much quicker," he says. "When we were trying to create match print proofs, it was taking anywhere from 45 minutes to an hour minimum, whereas now we can just send a file to the proof printer and it can generate a proof within minutes."
The proofing device is an HP 5500. Maloch says the colors match better, and what the customer sees off the press is a higher resolution than what they see on the proof.
Research Reveals Savings
When the University of West Alabama's Printing Services department installed a RIPit SpeedSetter 400 more than two years ago, there were two simple reasons: It was affordable, and it could output a landscape plate for a Hamada press.
Director Jimmy Robinson conducted a study comparing how much the university's print shop spent on film and labor to the cost savings that would be realized by purchasing the system. Robinson showed a cost recovery of three years.
Previously, the Livingston, Ala., shop used a tabletop filmsetter, outputting film, stripping and burning metal plates.
Robinson says there was not much of a learning curve once the new CTP system was installed.
"The only learning curve the press operators have is tightening clamps to stretch the plates," he says of the polyester plates. "They are easy to stretch so you don't have to clamp them down very hard. We were able to pretty much work into it after about a month and maybe three or four color jobs before we were cranking things out daily.
"It does a good job. We've had no trouble with it at all. The only thing we had to do was upgrade some software. The cost of one of those plates is only $1.67 apiece."
Robinson says the benefits center on time savings.
"It's amazing the amount of time you can save from stripping and plate making," he says. "We go straight from computer. The guy grabs a plate, mounts it and he's printing very quickly."
Need Plates—Fast
Kevin Hannah is the printing plant superintendent in charge of electronic prepress for the California Office of State Publishing, which installed an Agfa Galileo violet laser platesetter three years ago. The Sacramento printing operation—which ranked second on the IPG Top 50—outputs budget documents exceeding 3,000 pages.
"We needed a way of producing plates for lithographic printing as quickly as possible," Hannah says. "We had an older Rockwell system, an electronic beam recording system that was much slower. There were no more upgrades, and it was becoming problematic to keep it operational. We have to service the state legislature and we have a very short time frame to do that. We need dependable equipment."
The office conducted an industry technology analysis and determined Agfa could produce plates at the fastest speed, as well as handle a range of plate sizes. Proofing is done on Sherpa devices. The operation now does twice as much plating in the same amount of time, Hannah says.
"We've seen a cost savings in overtime because of the speed at which the work can be produced," he adds. "One of the most important things is it upgraded all of the staff's skills in current technology, which they have actually embraced."
Additionally, there is a reduction in press down time.
"This system allows us to just replace a single page rather than run a whole set of films, as we had to do before," Hannah says.
Getting Jobs to Press Quicker
CTP has saved time and money for Louisiana State University Graphic Services, which added an eight-up thermal Creo CTP device in December. Such savings were crucial for the nation's fifth largest university in-plant, a dual operation with digital and offset capabilities and nearly 100 employees.
"We needed to get things to the press quicker," says Don Davis, associate director. "Film, match prints and bluelines were just too costly in time and money to do."
The university agreed and gave the green light to fund CTP. Being a state institution, LSU's Graphic Services had to put the CTP system out to bid. Graphic Services wrote the bid specifications in a way that would offer the operation capabilities it sought, including CTP and digital proofing at high and low resolutions.
"We did not go to processless plates yet; the market is not mature enough," Davis says, adding that his operation uses Fuji metal plates. "Down the line, we have to have something chemical-free that is good for us and the environment. We are down to very few chemicals—just the plate processor."
Davis marvels at how smoothly installation occurred: "From Creo on the platesetter to Fuji on the plate processor, both started uncrating noon Monday, and by Wednesday afternoon, we processed our first test plate through the platesetter and processor. We already had the Creo workflow proofing system up, which we put in during October."
Eastman Kodak's plans to acquire Creo have left Davis, and other Creo customers, to speculate about their future support needs.
"To me, the key to the success of the merger is to maintain the strong support and service from both companies but especially Creo," he says. "Without that, the merger will not reach its potential or help us, the end user, meet the growing needs of our customers."
Davis says the key benefit of CTP is time savings because "we're in competition with the local printers just like everybody else. We probably were a little bit later in changing over, but we wanted to ensure the workflows and proofing devices were mature enough to handle the volume of work. I've only got three people in prepress. A few years ago when I came here, we had five. With the three people we can still turn the jobs extremely quick."
.
New Imaging Technology
The Impressia Metal PlateSetter uses Xanté's new Z-7 metal CTP imaging technology. Non-photosensitive Aspen Metal Plates allow for a process-free, chemical-free, no rinse workflow. This new technology links traditional anodized and grained aluminum plates with Impressia's imaging system. Metal imaging technology enables imaging directly to metal substrates. To ensure strength and durability, the Impressia Metal PlateSetter uses Radiant Exposure Technology, which incorporates high-intensity radiant light to instantly expose the Aspen Metal Plates.
Four New CTP Configurations
Presstek offers four new configurations of its chemistry-free Dimension Excel computer-to-plate systems: Dimension225 Excel, a two-page platemaker, and Dimension425 Excel, a four-page platemaker. Both feature semi-automatic plate loading and unloading and plate production at up to 11 plates per hour. Dimension250 Excel is a two-page platemaking system featuring automated loading with plate prestaging and platemaking at up to 17 plates per hour. Dimension450 Excel is the four-page high-productivity version of the 250.
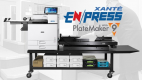




