ICTP may get all the attention, but at some in-plants imagesetters still have a few advantages.
By Vince DeFranco
Though computer-to-plate (CTP) and direct-to-press digital printing steal much of the technological spotlight, imagesetters still hold a place among in-plants and small commercial printers. Since many in-plants use older imagesetters that are paid for, the idea of re-engineering their plants to accommodate new, pricey CTP devices isn't a very popular one.
"We didn't go CTP a few years ago because the cost to get an aluminum platesetter at that time was prohibitive to us," explains Michael Schrader, printing and publishing manager for Mercury Marine, in Fond Du Lac, Wis. "To get the new equipment we estimated it would have cost us over $120,000 and I'm not exactly sure where we're going to be in three to five years; we might not even have offset. As it stands now, 40 percent of our work is DocuTech, and that number has been increasing steadily by 2 to 5 percent per year."
Schrader's 16-employee in-plant produces approximately 120 million impressions per year on its mix of two DocuTechs and three offset presses. The operation has been producing Mercury Marine's literature, including service documentation and owner manuals (primarily black-and-white) for more than 50 years.
Its output numbers are on the rise, however, as production of the company's inboard and outboard boat motors continues to grow. As the world's largest marine propulsion company, Mercury demands a great deal from the literature included in its new products and its after-market support documents.
To create plates for its offset-printed literature, the in-plant utilizes a six-year-old ECRM imagesetter to image film. The company has looked into purchasing a CTP device and has even explored the possibility of imaging polyester plates on an imagesetter.
Schrader notes that despite the growing use of digital photography in the design community, Mercury's service materials still largely remain text- and line-art-based. With infrequent printing of halftones, the plant's quality concerns are not the main focus, and most of the work it prints is 120 lpi. For Schrader, this somewhat negated one of the primary benefits of CTP technology: improving quality.
Mercury Marine also tested a computer-to-polyester CTP system as a lower-cost alternative to full-blown CTP. However, since his operation produces a lot of reruns, and polyester plates are generally not reusable once imaged, the decision was made to stick with the existing tried-and-true imagesetting workflow.
"Our imagesetter has been trouble free," Schrader notes. "We have it cleaned and calibrated regularly, and it is getting less wear and tear as more work goes to the DocuTech."
The machine is six years old, and although Schrader is aware that even the new breed of imagesetters have much more sophisticated screening technologies, his attitude is one of "if it isn't broken, don't fix it."
According to Schrader, the strategy going forward will be to continue to make plates from film and hope the existing equipment lasts a few more years until a long-term investment decision is made.
"If my five-year vision is realized, it will be all digital for us," predicts Schrader. "We will be printing on demand."
'Our Imagesetter Has Proven Itself'
Down in San Antonio, Texas, Janet Pendleton, director of Printing Services at the University of Texas Health Science Center, oversees a similarly equipped digital/offset in-plant that relies on an older model imagesetter for its film. The six-year-old Agfa Avantra outputs the film that produces everything from manuals and handouts to brochures, magazines, newsletters and posters, both for the school and for student walk-in orders. Producing film up to 24˝, the device has been trouble-free for the 25-employee in-plant.
"Our imagesetter has proven itself to be very reliable right now, but for our next investment in that area CTP would definitely be considered," she says.
Pendleton recognizes the unquestionable quality improvements that a new CTP device would offer, but the direct and associated costs are significantly higher.
All offset work is printed on the in-plant's one Heidelberg and two Ryobi presses, while digital work is produced on a DocuTech. Like Schrader, Pendleton sees increasingly more traditional offset work migrating to the Xerox equipment, especially the growing amount of black-and-white work up to 300 copies, coming in on digital files.
"It's not always about quality, but about productivity too," explains Pendelton, citing the conversion of the offset-printed university telephone directory. "It used to be printed four-up, using the imagesetter to make the file, then it had to be cut and collated. If it was formatted to the DocuTech, the pages are already to size, and are collated on the machine, and it's just a matter of doing mechanical binding."
Outputting To Polyester Plates
Arizona State University has had success using its imagesetter to image film and polyester plates.
"We use an Agfa SelectSet 5000 running a Xitron Navigator RIP, and it's working great," says Harv Dahl, print consultant. "It's an older machine, but it does the smaller material, which we need for the smaller-format jobs."
The ASU in-plant produces letterhead, envelopes and business cards, mostly one- and two-color. Although the shop prints some four-color work, most of that goes to the Heidelberg Quickmaster DI, operated in conjunction with the university's graphics program.
The imagesetter outputs to polyester plates for letterhead and business cards, while all envelope work (mostly #10s and some #9s) are run on a two-color Halm Jet press, which requires a metal plate.
"Once in a while we go to some close register color work on the Ryobi two-color press, so we go to film on that also, for a better product." Dahl says. "You can hold finer lines on the film, you get better resolutions, and it's a lot easier to get a good run length off metal versus poly."
With polyester, the plant has performed run lengths up to 30,000 but that requires paying good attention. The average run length for its polyester plates is about 5,000.
For ASU, CTP is not an option for the immediate future.
"It would be nice to be more sophisticated if it would be beneficial to the academic program, but for normal production work, although there could be some advantages in efficiency, this works quite well," he says.
One main benefit of the imagesetting system is the flexibility it provides in the "fluid" university market, where phone numbers and departments heads change frequently. The in-plant keeps a lot of its imaged film handy for revised envelopes. For letterheads and business cards, polyester makes sense due to the low cost to output new plate material compared to the cost of metal plates.
"When we throw a plate away, we're not looking at a lot of dollars because of our small format," Dahl says. "But when you get into 29˝ or 40˝ presses, you have a pretty good chunk of aluminum you are throwing away."
Dahl believes the operation's move to CTP is inevitable but questions the time line to reach that point. He admits he doesn't see the existing system lasting longer than five more years.
"At that point, we'll have to make a change, so we'll look at what's going to work best for combined efforts [of the in-plant and the graphics program] and go with that," he says.
- Companies:
- Agfa Graphics
- Heidelberg
- Xerox Corp.
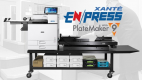




