Expanding into Four-color
A year and a half ago, the University of Southern Indiana's Publishing Services operation was outsourcing 75 to 85 percent of its four-color work. This bothered Terri Bischoff, assistant director of Publishing Services, at the Evansville, Ind., school. She knew the university would be better served if her in-plant could gain control over this work, improve the quality and reduce turnaround times. To do this, though, would require some new equipment.
After researching digital printing technology options, Bischoff and Director Leslie Parker came to a decision. They felt that a Presstek 52DI digital offset press would be the best fit and would allow them to handle the majority of four-color print jobs.
"We had the money in reserve, a skilled staff, and adequate space," Bischoff says. "We believed we could make this investment without breaking the bank."
So in July of 2011, the 12-employee in-plant installed the new press and started bringing four-color work back in-house. Customers noticed the difference right away.
"Not only do they appreciate the improved quality," Bischoff says, "but they also like the fact that we have complete control over the job rather than outsourcing the work to an outside firm who is juggling the priorities of many customers."
A Busy In-plant
Founded in 1965, the University of Southern Indiana (USI) enrolls more than 10,500 undergraduate and graduate students in 70 undergraduate majors, 10 master's programs, and one doctoral program. Publishing Services coordinates the production of all university publications and graphic needs from the initial idea to the last staple. The in-plant has first right of refusal for all university printing. Partially funded by the university, it also generates revenue to purchase equipment and pay salaries.
The in-plant's full-time production staff consists of three graphic designers, two press operators, one bindery technician and three copy center staff. For years, Publishing Services had been operating with a pair of two-color Hamada presses supported by a Presstek Vector platesetter and a Xerox 700. Its bindery consisted of a Perfecta cutter, a Stahl folder and a BinderyMate twin-head stitcher.
"When I got here over five years ago," says Bischoff, "we were still using film-based platemaking, and disposing of the chemistry was a real dilemma, to say nothing of the productivity impact. Adding a chemistry-free platesetter improved production time, increased our print quality, and moved us in a 'green' direction."
Because most of the university's marketing materials were printed in USI's signature red and blue colors, this configuration was adequate to meet customer needs. Over time, though, customers' preferences began to shift to four-color printing.
"We could handle the shorter runs on our Xerox printer," says Bischoff. "But there was a growing amount of work we simply couldn't handle and had to outsource to local printers. While we do work closely with the local community on a lot of fronts, it was becoming quite obvious that we needed to update our production platform to regain control over the quality, cost and timing of our work."
Working with Parker, and relying on the experience gained during her past employment with local printers in the Evansville area, Bischoff examined her options.
"I had exposure to DI technology at a commercial printer where I was previously employed, and understood the benefits of the process," says Bischoff.
Bischoff and Parker were particularly attracted by the Presstek 52DI's automated performance, and its small environmental and physical footprint.
"We really like the waterless printing technology and the types of inks the press uses, as well as the fact that it uses thermal imaging technology to image chemistry-free plates," Bischoff says. "We already had chemistry-free platemaking in place for our two-color press and did not want to introduce a press that required chemistry."
Like many in-plant operations, Publishing Services is space-constrained; Bischoff indicates that the press, with its small footprint as compared to other offset press options, fits perfectly into the shop.
Customer Approval
Customers have been very pleased with the press's quality. Bischoff also points out that if a quick reprint is needed or if a job must be put back on press for any reason, having the Presstek DI on site is ideal. In addition, if there is a problem with a file, Publishing Service's design group is right next door and can expeditiously address any issues.
"If we are working with an outsourced vendor," she says, "these types of issues can add lots of cycle time and/or cost to the job."
Publishing Services finds it economical to move runs as short as 500 from its toner-based digital press to the Presstek 52DI.
"It saves us time and money, and the quality is better," Bischoff explains. "While we still have our two-color Hamada, we also find that we frequently run spot color work on the 52DI because of the increased quality it gives us."
With the increased volume of in-house work as a result of the new press, the department's bindery had to be upgraded.
"We knew we would need to enhance our bindery," Bischoff says. "We were outsourcing booklet and newsletter finishing to an outside bindery operation, and we produce a lot of booklets and newsletters. Our latest investment has been a Horizon vacuum-feed booklet maker."
This system, comprising a Standard Horizon SPF-11 stitcher/folder, FC10II trimmer and 10-bin Horizon Vac 100 collator was installed in August.
"This makes us even more self-sufficient," she says.
Looking Ahead
Bischoff expects the volume of four-color work to continue to grow.
"I have seen a real change in the types of jobs we produce," she says. "The designs are more complicated, and with four-color capability, we can do so much more graphically than we could with one- and two-color printing. And once one department takes advantage of the new service, others see it and want to follow suit."
Not only is Publishing Services handling more print in-house, but the volume of design work coming to the shop is also increasing.
"The university is growing by leaps and bounds, and we want to be able to keep up with that growth and the demand for print it is generating," Bischoff notes. "Even though in a lot of places, print volumes have declined, we haven't seen that at USI. With our new printing and finishing capabilities in place, we look forward to a future of growth and an even happier customer base within the university. Our future looks bright, and our staff is excited to come to work every day.
Related story: Penn State Adds DI Press
- Companies:
- Presstek Inc.
- USI Inc.
- Xerox Corp.
- People:
- Leslie Parker
- Terri Bischoff
- Places:
- Evansville, Ind.
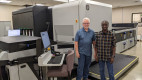



