

With the new Xanté X-33 UV flatbed printer, the in-plant is able to print directly onto rigid materials like wood, glass, metal, and acrylic. Here, Bob Donahue runs the machine.
As director of Purchasing, Mail and Printing Solutions at Franklin University, Bob Donahue gets a close look at the type of work being procured outside the university. If he determines his in-plant could produce that work more cost effectively, he looks into bringing that service in-house.
This entrepreneurial approach has inspired the addition of services like dye-sublimation and garment printing at the Columbus, Ohio, in-plant. Recently, the four-employee shop also added engraving to its list of value-added services when it installed an Epilog Mini 24 laser engraver. With a 12x24˝ engraving area, the desktop device is enabling the in-plant to personalize leather drink coasters, glass drinkware, name plates, and other specialty items. It can engrave metal, wood, acrylics, plastics, stone, and other rigid materials to create personalized pieces that departments can give out as tokens of appreciation.
“The more you personalize, the higher the perceived value,” points out Donahue.
This follows the addition of a Xanté X-33 UV flatbed printer, which has enabled the shop to print directly onto rigid materials like wood, glass, stone, metal, acrylic, or corrugated plastic, instead of printing onto vinyl and laminating onto other material.
Related story: Franklin University Expands … Again
“I can just print directly to corrugated plastic for yard signs,” enthuses Donahue. This has cut production times by two-thirds, he says.
“It improves our profit margin, plus we’re able to reduce the price to our customer,” he says. “That’s a double win.”
Beyond signs, the in-plant has printed sheets of magnets, slate awards, and artwork on prestretched canvas.
“It’s an extremely versatile machine,” Donahue praises. Plus, its small footprint made it easy to fit into his 3,500-sq.-ft. shop.

Bob Donahue uses the new Epilog Mini 24 laser engraver installed at Franklin University Printing Solutions.
The X-33 is powered by iQueue, Xanté’s Adobe PostScript-based PDF workflow software, which simplifies adding variable data, managing color, controlling image quality, and creating multi-up imposed layouts.
“With the Xanté, I’m taking a file and I’m just dragging and dropping it into the print queue,” says Donahue.
He is looking into using the X-33 to brand the boxes his in-plant uses for delivering jobs. The shop recently rebranded itself from Print Services to Printing Solutions and has a new logo.
Another recent installation was a new Konica Minolta AccurioPress C6100, to replace a Konica Minolta bizhub PRESS C1100. This joins an existing C6100 in the in-plant, but the new one has a three-knife trimmer so the shop can now complete booklets in-line. That has been a big help in producing magazines for an outside customer. They no longer must be taken to a separate booklet maker for finishing.
“It probably reduced our time by one third,” he remarks.
The main reason for upgrading to the C6100, he says, is because of the accompanying IQ-501 Intelligent Quality Optimizer, which provides automatic density correction and improves color consistency and front-to-back registration accuracy.
“We’re seeing that improved color consistency,” Donahue testifies. “We can now run both machines on the same project … and get the same color quality and consistency.”
- People:
- Bob Donahue

Bob has served as editor of In-plant Impressions since October of 1994. Prior to that he served for three years as managing editor of Printing Impressions, a commercial printing publication. Mr. Neubauer is very active in the U.S. in-plant industry. He attends all the major in-plant conferences and has visited more than 180 in-plant operations around the world. He has given presentations to numerous in-plant groups in the U.S., Canada and Australia, including the Association of College and University Printers and the In-plant Printing and Mailing Association. He also coordinates the annual In-Print contest, co-sponsored by IPMA and In-plant Impressions.

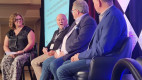



