Perfect registration. Faster makereadies. Lower costs. In-plants with direct imaging presses boast of these benefits and more.
by Bob Neubauer
AT THE University of Texas at Austin a few years ago, the administration started to fall in love with color. Alumni invitations and other projects were increasingly being designed in four-color process, then farmed out to local printers when they proved too complicated for the in-plant's aging two-color presses.
To save the school money and give it more control over the final product, Printing Services started looking into digital color, with the administration's blessing. In the end, the in-plant settled on a Heidelberg Quickmaster DI direct imaging press.
Since then, posters, flyers and invitations to football-related activities have all been printed in-house, with surprising speed and excellent quality, according to Production Manager Tommy Willms.
"We're certainly capable of doing next-day turnaround," he remarks. "The DI allows us to do that real quick because you eliminate the film output process, and the blueline stage, and the stripping, and the platemaking."
Virtually every printer that has taken the plunge into direct imaging offset technology tells the same story of faster makereadies, better registration, quick job changeovers and lower costs. Printers with a frequent need for four-color jobs between 500 and 5,000 runs find DI to be a great fit.
"The quality of the printed material is outstanding," lauds Jerry Wilson, division director of Alabama's Division of Printing and Publications. The 61-employee in-plant installed a Heidelberg Quickmaster 46-4 DI last summer. "We're able to take jobs in and complete them faster and satisfy the customer's needs better with that machine than we were with regular offset."
DI has allowed in-plants like the University of Texas to get into four-color printing and bring jobs back in-house. Other in-plants, like the County of Tulare's operation, in Visalia, Calif., see DI as a way to take work off their color copiers and provide better quality printed pieces.
Find Out More To find out more about direct imaging, get a copy of "The GATF Guide to Direct-Image Presses." The 144-page book costs $75 ($55 for GATF/PIA members) and can be ordered by calling (800) 662-3916 or visiting www.gain.net. Also, Presstek has produced an informative White Paper on digital imaging presses. You can get a free copy by e-mailing marketing@presstek.com. Finally, a new study by the Graphic Arts Marketing Information Service, part of GATF and PIA, provides an understanding of direct imaging market dynamics. The study, Direct Digital Imaging, is free to GAMIS members. For more information, call (703) 519-8179 or e-mail jbland@printing.org. |
Slow To Catch On
Despite these benefits, though, acceptance of DI has been relatively slow. In the decade-plus since the technology was introduced, 2,628 systems have been sold, according to "The GATF Guide to Direct-Image Presses," published in February. (Since the end of 2002, another 500 or so were sold, says book co-author Frank Romano.)
Recently, Xerox decided to stop marketing its DI presses, making some in the industry wonder if the company had lost faith in the technology. But although Xerox spokesman Larry Vogel admits, "We were, frankly, not thrilled with the number of installations that we had," he insists DI technology has many strong points. Xerox dropped DI, he says, to focus on dry-ink-based digital printing.
"We decided that we've got more than enough work to do in the iGen3 space," he says.
The gap left by Xerox's departure from the DI market was quickly filled by Kodak Polychrome Graphics (KPG), which will now market its own DI press, the DirectPress 5034DI (an OEM version of the Ryobi 3404 DI, previously sold by Xerox as the DocuColor 233 DI).
John Schloff, KPG's vice president of digital printing and color, says KPG, a large provider of consumables, chose to enter the DI market because it feels the three areas most important to its customers are computer-to-plate technology, digital printing and DI.
"Our customers have told us that they want an unbiased supplier that can work with them along all three of those options," Schloff says. "We've positioned ourselves to be able to do that."
KPG's 5034DI, like most DI presses, uses imaging technology from Presstek, which coined the term "DI." Presstek was involved in direct imaging from the very beginning, when a spark-erosion process was used to image plates on the first DI press, the Heidelberg GTO DI.
Since then, Heidelberg has installed 900 DI presses in North America and continues to improve its offerings. At Graph Expo it announced a Smart Spooling feature on its Quickmaster DI Pro presses. This saves printers money by reducing the amount of plate material that gets wasted.
"When you forward from that job to obtain the next full job, the forwarding is customized to the length of material that was imaged on the prior job," explains Joerg Daehnhardt, product manager for direct imaging. In other words, if you only used a small amount of the plate, it will only spool ahead a small amount.
In addition, Daehnhardt says, an overimaging feature allows you to reimage the same plate to print a solid on the next job.
Also, Heidelberg will reportedly soon offer a new, more cost-effective plate material for its DI presses called Saphira Caleidoplate 46, made exclusively for Heidelberg.
More Affordable DI
Perhaps the most important thing Heidelberg has done to increase interest in DI has been to create a remarketed press program to make refurbished DI presses available.
"That definitely opened a market that hadn't been there before," notes Daehnhardt.
One in-plant that purchased a remarketed press was the County of Tulare's Print & Mail Services. Manager Hal Cypert says he looked at Xerox and Indigo digital printers, but in the end decided to go with a refurbished Quickmaster 46 DI, for which his 15-employee shop paid $186,000.
"The cost of ownership, in the long run, is going to be cheaper for us with the DI," he says.
This may surprise some printers, since many still list "cost" as the main reason they have not looked into DI. But for those with the right type of short-run four-color work, DI can certainly save money in the end.
"From a cost-justification standpoint, they're probably one of the easier ones to put down on paper and actually justify the investment," remarks Don Trytten, vice president and general manager of xpedx Import Group, U.S. distributor of Ryobi's DI presses. "We have tremendous interest in our machine because of the quality and the ease, and the relatively fast imaging time."
Enthusiastic Fan Club
All these factors have brought DI a number of fans in the in-plant market.
"The efficiency of it is probably the best thing," remarks Glenn Hamilton, a press operator at the Oklahoma Department of Transportation, which purchased a Xerox 233 DI about two years ago. "The positioning is perfect every time. And also the ink fountain is set." He says he was "shocked" by the good quality of the DI press.
Trytten, of xpedx Import Group, is not surprised.
"Every in-plant, almost, has an application for it," he insists. "It also fits the application of the in-plants that maybe moved away from offset, and this allows them to incorporate an offset machine in the office atmosphere."
This is precisely what the County of Tulare's in-plant did. Hal Cypert says his shop has been running about 100,000 color copies a year, with run lengths averaging 1,000 sheets. From now on, though, any order of 300 copies or more will be done on the DI press. The quality will be better, he notes, and a greater variety of stocks can be used.
"We estimate that we will move 90 percent of our work off the color copiers and print it on the press," he says. "This will give us the ability to provide more color at a cheaper price."
The Quickmaster 46 DI will enable the in-plant to bring approximately $80,000 worth of outsourced color printing back into the shop.
"We felt this is going to be the best way to bring four-color into our shop with a minimal amount of operator expertise in the area of traditional four-color printing," Cypert says. He notes that the automation makes the press relatively easy to run.
With all of its benefits, DI seems sure to grow in popularity. According to "The GATF Guide to Direct-Image Presses," the market for two-up, four-color DI presses will triple from 2000 to 2005, and then more than double by 2010.
The Future
But will direct imaging units eventually be part of all offset presses? No one seems to think so. The technology has so far proven most popular on two-up presses. The larger DI presses have not been big sellers.
And consider that new DI marketer KPG is not worried about its existing consumables business.
"Plates are our bread and butter," notes Schloff. "We see a tremendous future forward for that to continue."
"I wouldn't say [DI] is the future," adds Heidelberg's Daehnhardt. "But it is one of the futures.
Certainly those in-plants that own DI presses see a big future in them.
"Some of our customers...even ask for work to be done on that because of superior quality and turnaround time," says Jerry Wilson, of Alabama's Division of Printing and Publications. "So that's saying something there."
For More Information
Adast America
|
www.adast.com
|
Creo
|
www.creo.com
|
Heidelberg
|
www.heidelbergusa.com
|
KBA North America
|
www.karat-digital-press.com
|
Kodak Polychrome Graphics
|
www.kpgraphics.com
|
Komori America
|
www.komori.com
|
MAN Roland
|
www.komori.com
|
Presstek
|
www.presstek.com
|
Ryobi (xpedx Import Group)
|
www.ryobi-group.co.jp/en
|
Sakurai Graphic Systems
|
www.sakurai.com
|
Screen (U.S.A.)
|
www.screenusa.com
|
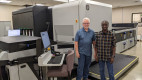




