A number of in-plants have added DI presses, speeding their turnaround times and saving money. Here are some of their experiences.
Offering their observations for this story were:
Gerard Catrambone
Associate Director
Office of Publications
University of Illinois, Chicago
Heidelberg QuickMaster DI 46
Hal Cypert
Communication Services Manager
Print and Mail Services
County of Tulare, Visalia, Calif.
Heidelberg QuickMaster DI 46
Dan Lee
Group Manager, Prepress and Special Services Printing
LDS Church Printing Division
Church of Jesus Christ of Latter-day Saints
Salt Lake City
Ryobi 3404 DI
Scott Lipsey
Quality Control Coordinator
Printing Services
Mississippi State University
Starkville, Miss.
Heidelberg QuickMaster DI Pro
Jobs printed on your DI press:
Hal Cypert: We print brochures, books, booklets, envelopes, business cards, letterhead and flyers.
Scott Lipsey: We have run every type of job through our DI. From envelopes to magnets. The majority, though, is four-color newsletters, brochures and posters. We run spot color in the DI for hard-to-print solids and very close registration jobs.
Dan Lee: Small 11x17˝ posters, four-color brochures, some small advertising pieces, four-color programs.
Gerard Catrambone: We're doing everything from multiple-signature newsletters to single-sided flyers. We're doing brochures, newsletters, some recruiting pieces, post cards.
Productivity advantages of DI over a traditional offset press:
Hal Cypert: Makeready time is greatly reduced, as the press images the plates on the plate cylinder in perfect registration. A color profile is established for each job. On exact repeats the color values saved can be used.
Scott Lipsey: The registration is perfect. Zero time is spent on registration. Quality of print is achieved very fast, saving time on getting the press production ready. It really is a huge time saver.
Dan Lee: Mostly the time savings is in prepress because there's no prepress involved. It goes directly to the press. The setup time on the press is much quicker than conventional offset too. There's not the water, because this is a waterless press. We can get up to color a lot faster.
Gerard Catrambone: I can get jobs in and out next day, and that's including bindery work. I can treat this thing—and I do sometimes—as a color copier. They want 1,000, 1,500—it makes more sense to do them on the DI.
Cost advantages of DI over traditional offset:
Scott Lipsey: The biggest price advantage comes in the form of the number of jobs you can achieve off the DI. You can easily pop off a number of four-color jobs by lunch. That is the biggest cost advantage. The biggest profit comes from the quantity of work you can achieve. Another area you save on, and you do not even consider it a lot of the time, is not having to buy the chemicals for fountain chemistry. Being waterless is a wonderful money saver.
Gerard Catrambone: The price per plate on the DI is $10. One plate on my 25˝ is, with film and everything, I think it's like $37. There's no labor involved—very little anyway.
Hal Cypert: Reduced makeready time was the biggest cost savings. Not having to hang and register the plates saves both time and materials.
Dan Lee: Cost savings include, less costs for prepress, makeready and cleanup
Quality compared to regular offset:
Scott Lipsey: Being waterless, the quality is outstanding. The images and color seem more vivid. Also, with the registration being so great, we never have reruns due to blurred images. Registration is wonderful, making for a nice printed piece.
Dan Lee: They're very comparable. When we initially got ours, there were some of the church designers that actually would say, 'put this on the DI press; we want this on that press,' because they were so pleased with the quality.
Gerard Catrambone: Very comparable, I think. It took a while to find a pressman that could run it well. We were really disappointed with it at first. I would cringe whenever jobs would come in with heavy solids. They look beautiful now.
Hal Cypert: In my judgement there is no difference in the DI print quality verses traditional offset.
Other advantages of DI:
Hal Cypert: You can save color profiles of jobs that are produced for future use, which creates color consistency from job to job. Our current operator had no previous four-color experience prior to running our DI press. The operator was trained the week that the press was installed and has been doing fine ever since.
Scott Lipsey: The human error of masking negatives and burning plates is eliminated.
Advantages of DI over toner devices:
Hal Cypert: Toner technology, while improving, has not reached the same quality and durability levels of ink technology. Also, in the toner applications you reach the per-click cost sooner verses offset. Thus, longer-run jobs are going to be less expensive using ink.
Scott Lipsey: The speed of the DI is a major advantage. Running up to a speed of 10,000 an hour. Even though toner-based devices have come down in price per copy, it still cannot compare to the price per copy we get off the DI.
Dan Lee: Color is more true than anything I have seen in a toner-based system. Running these posters that are a solid color, you get banding vibration on the toner process, and when you're running a solid, like a solid blue sky, it shows up. You just see that banding vibration that you don't have on a press. Although I know there are some people that are using the iGen for similar things and they're thrilled with it.
Gerard Catrambone: I think the quality [of a DI press] is still a lot better.
Advice for other in-plants:
Hal Cypert: If you are looking for a sound alternative to vending out your process work and are looking for a product that is operator friendly, then you should consider a DI press.
Scott Lipsey: The DI is a great choice if you have a good volume of small four-color printing. If you do not have an abundance of four-color, then it is not a wise choice. I often say that the DI will "eat up" a four-color job, meaning you speed through a large number of small four-color jobs in an eight-hour shift. Even though the DI can handle a large-quantity job, the real money is made in a large number of small-quantity jobs.
Dan Lee: We have found a nitch for the DI in the intermediate run lengths that are not cost effective to put on a full-size, four-color press but still require the quality of offset. We've been really happy with it. We had some maintenance issues because it was a used press, but other than that we've been really happy with it.
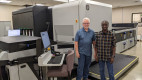



