DI’s New Niche

IT HAS now been 16 years since Heidelberg introduced the first GTO digital imaging (DI) offset press. In that time, enhancements in architecture, quality, speed and control have served to create a viable and sustainable technology.
The history, though, has been rocky. Other displacement technologies on both sides of the run length and quality equation continue to compress the space in which DI presses play. Still, digital imaging presses have many unique positive qualities that every in-plant should consider.
As an independent consultant, I know that one of the things my clients appreciate is my objectivity. I operate in an unbiased, vendor-neutral environment. In this article, I’m going to talk about what the marketing hype won’t: the reality of DI presses from a holistic perspective.
Presstek offers the widest assortment of DI presses, with three on the market according to Tom Leibrandt, the company’s product manager for press products. These range from the entry-level 34DI-E and the high-productivity 34DI-X, both 34cm portrait-format presses, to the 52DI, a landscape format 52cm model capable of 10,000 impressions per hour (iph) with a stream feeder as standard equipment.
Ryobi and Presstek jointly developed all three models. Ryobi markets the 34cm presses as the 3404E-DI and the 3404X-DI. They’re sold in the U.S. by xpedx. Kodak also brands them as the 5334 DI and the 5634 DI. The 52cm model is currently available exclusively through Presstek but is built to their specifications by Ryobi.
There are, however, competitors to Presstek’s technology. Eric Frank, KBA’s vice president of marketing, reports that the 74 Karat is the only 29? landscape-format DI press in production today. It employs Creo laser diode imaging arrays and is the only current DI to use Presstek metal plates. Its compact design both feeds and delivers from the same end of the press. KBA also offers kits to add cardboard and plastic printing capabilities.
The Screen Truepress 344, a 34cm portrait-fed press utilizes the same proven imaging technology as on their CTP devices, and uses Konica polyester plates developed to Screen’s specifications. Screen’s Mark Crawford notes it is the only DI on the market to use traditional wet-offset technology, allowing for conventional ink and fountain solution usage, thus dramatically reducing consumables costs.
Both KBA and Screen offer inline coating options. Presstek is evaluating the development of an inline coater for the 52DI.
When it comes to used equipment, there is a well-established base for the cost-conscious or entry-level buyer. Presstek for example, now offers rebuilt Heidelberg QMDI presses at about half the cost of one of their new entry-level machines. And for the adventurous, there is also a rather large independent dealer and FSBO market.
As far as continued availability, Heidelberg, Ryobi and Adast still do a brisk business manufacturing replacement parts for out-of-production models, and supplies are available from Presstek, which provides 95 percent of DI consumables worldwide.
Service for used and remanufactured equipment is available from factory-authorized technicians from virtually every OEM with presses still in the field. Presstek has 250 service people in the U.S. alone. There are also a host of independent service technicians, many of whom were factory trained.
The big advantage DI has over digital presses, especially in the used market, is service cost. First, there are no click charges, and second, although service contracts are offered, they are not mandatory (though Presstek provides a 90-day warranty on its remanufactured QMDIs). This can greatly reduce total cost of ownership (TCO).
The ‘Opposition’
If you’re trying to make the decision between a DI and an automated conventional press with CTP, start first with your own due diligence. Do you have a CTP system in place already? Trained four-color press operators? Required floor-space? Does DI really fit your growth plans?
DI proponents will promote the benefits of automation, but just as much automation is available on today’s conventional presses, if desired. In certain environments the argument can be made that traditional offset is a more productive fit.
On the flip-side, digital color presses have many positive advantages over DI if the work mix is right. For short-run static workflows under 500 press sheets (business card runs are a great example), in true POD environments where just-in-time requirements necessitate immediate finished and delivered turns, digital presses from HP, Kodak and Xerox have the upper hand. This is also true at in-plants where near-infinite variability of text and images is required.
Then there is the mid-volume-level production equipment (50+ cpm), from companies such as Canon, Konica-Minolta, Ricoh and, of course, Xerox. Such equipment has taken big leaps in image quality over the past few years. Mid-volume production equipment should be considered if monthly volumes and TCO don’t justify either DI or a production-class color digital press.
An interesting perspective from a psychological viewpoint was offered by Jeff Steinhardt, graphics sales manager for xpedx’s Denver office (which sells both Ryobi DI presses and conventional offset equipment).
“The DI architecture doesn’t look like a press, so it isn’t as intimidating to those coming from either the digital or the small two-color offset market,” says Steinhardt. This should also be considered, as perception frequently translates into reality.
So Where’s the Niche?
As with anything, niches are created by voids and the creativity to fill them. Digital Imaging presses fill the space between what can cost-effectively (and time-effectively) be done either by near-offset-quality digital color devices on one side, and 20? to 29? conventional offset presses on the other.
Comparing speeds, cut-sheet digital printing solutions run between 70 and 110 letter-size 4/0 copies per minute (cpm). Conversely, a 15,000-iph, 14x20?, four-color offset press equals the equivalent running speed of a whopping 500 cpm in digital-speak, in case you’ve never done the comparison. DI speeds fall in the middle, generally ranging between 7,000 and 10,000 iph, equaling from 233 to 333 cpm.
Let’s have some fun. Plate imaging and makeready time for many DIs is now under 10 minutes. This is equal to a 350 press sheet run time on a 70-cpm digital press. So what if we ran 500 13x18? sheets, post-RIP, on both a 7,000-iph DI and a 70-cpm digital press? This would take 14 minutes on both the DI and the digital press. But for 1,000 press sheets, that all changes. The DI can do it in 18 minutes, the digital press 28 minutes.
That’s something to think about.
‘Dear John’ is Alive and Well
In a presentation I gave a few years ago for the Southeastern University Printing and Duplicating Managers Conference, I said, “Buy for POD. Be ready for VDP.” I still stand by that statement...but a few things have changed.
Although we would have hoped for dramatic changes by now, the fact remains that most cut-sheet-printed variable data done today is still text-only. Unless there is a need for true 1:1 personalization—meaning changing both text and multiple (color) images on the fly—a versioning mentality employing segmented base runs on a DI and imprinting with laser, could be a better, less costly solution.
Yes, Virginia, a DI is Offset
Another advantage DI presses have over digital is color versatility. DI presses are configured for four-color process, but they can also use Pantone mixes, including metallics. Although there are digital presses with either enhanced color gamut capabilities or additional custom spot color options, the cost for either is generally higher, and exact Pantone matching can still be an issue.
Digital press manufacturers have long promoted their benefits in comparison to offset. Demographically segmented runs, constantly changing information causing obsolescence, proof of concept, test market applications, etc. All of these fit the DI as well. The big difference is that DI doesn’t just emulate offset quality, it is offset quality, and for many higher-end customers, that’s still the expectation.
Regardless of what size your in-plant is, DI presses have the ability to fill a gap or extend a reach:
• Substrate flexibility exceeds what digital presses can handle.
• Quality exceeds all but the highest levels of traditional offset.
• Both small and relatively large run lengths become cost-effective.
• DI is an obvious choice for process or spot color shell runs for future imprinting on digital devices.
All this combined points to DI being a viable and mainstream technology bridge between high-quality digital color and traditional litho. If nothing else, it’s worthy of investigation.
So I leave you with this challenge. Look at your work mix. On similar volumes, calculate cost per printed 4/0 page for digital compared to DI, or DI versus conventional offset. Also look at laser imprinting costs on DI-run shells versus running full-color VDP when it’s just the black text that changes. You may be surprised to find the niche for you really does exist. IPG
Vic Nathan Barkin has more than 30 years of experience in the printing industry and currently owns a consulting practice specializing in digital printing business development, workflow and technology implementation geared to the in-plant community. He was the manager of Northern Arizona University’s Printing Services department for 12 years and recently served as solutions sales manager, digital printing, for Kodak’s Graphic Communications Group. A Certified Graphic Communications Manager with IPMA, he is also a past president of the IPMA’s Arizona chapter, and has been a presenter at ACUP and SUPDMC. In addition, Barkin serves as an executive board member of the Mountain States Printing Education Foundation, and is an active associate member of the IPMA Rocky Mountain chapter. You can contact him at: vicbarkin@netscape.net
- Companies:
- Presstek Inc.
- Xpedx

Vic Nathan Barkin has more than 35 years of experience in the printing, paper and wood products industries and currently owns a consulting practice specializing in business development, workflow, and technology implementation, focusing on “Green Procurement and Production” practices. Vic is a QMS Lead Auditor certified to ISO 9001:2008 standards, is a consultant for the Rainforest Alliance as an FSC Chain of Custody and Controlled Wood senior auditor, is an FSC, SFI and PEFC lead auditor for PricewaterhouseCoopers and SGS North America, and has engaged in more than 700 site assessments and audits.
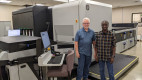



