Are you getting the most out of your digital paper? Find out from the experts.
By Kristen E. Monte
DIGITAL PRINTING delivers a leap in technology—but make sure you don't stumble when it comes to the digital paper you use.
In-Plant Graphics spoke with industry suppliers of digital paper to get some important runnability tips. Read on and take note.
Identifying Quality Paper:
• Quality paper should arrive well packaged and protected, be clean and not dusty when inspected, and feed evenly without major efforts. The paper weight is important because there are usually complex paths in digital presses, and there are limits to the thickness some presses can handle. Storage and handling information should be available from the supplier.
—Gerry Rector, Neenah Paper
• Characteristics of quality digital paper are reliable runnability at high speeds, excellent print quality and papers developed especially for the equipment type.
—Cindy Hamrick, International Paper
• Ask the following questions: Will the paper dry in time to laminate after printing or will it have to be spread out on tables to dry, causing time delays? Can media quality be trusted enough to print unattended? Will the next run look the same as the first? Does it tear, fade, weather well? These are the things you can't tell when looking solely at the price tag.
—Meyer Weiss, InteliCoat Technologies
• Quality digital paper can be identified by a few key attributes, including smoothness, shade, brightness, formation, and opacity. Also, the paper needs to be precision cut squarely with no dog-ears and provide good runnability
—Garth Geist, Unisource Worldwide
.
Getting Good Deals:
• There are many ways to save on digital papers without compromising quality. First, analyze the types of projects that you do. Color jobs are typically higher value and demand a higher-quality (brighter, smoother) paper. Consider buying premium digital paper for your color work and stocking up on lower-priced (lower brightness) paper for black-and-white copying. Don't just track the paper costs; also consider the cost of downtime due to paper jams and misfeeds.
—Laura Shore, Mohawk Paper
• Before the in-plant manager can get a competitive price, he/she needs to make a commitment to use digital paper on a consistent basis, because the printing quality, when using digital paper, is far superior to standard paper. Once this commitment is made, the in-plant manager will have enough paper volume to negotiate the best deal with his/her supplier.
—Garth Geist, Unisource Worldwide
.
Buying in Bulk:
• Don't buy for several years of printing unless necessary. Look for paper that can stay in its protective packaging. Designate an area that is safe from traffic. Store paper in a relatively even environment.
—Gerry Rector, Neenah Paper
• When buying in bulk, the in-plant manager needs to make sure that the packaging provides a good moisture barrier. Controlling humidity is critical to ensuring good runnability and performance.
—Garth Geist, Unisource Worldwide
.
Paper Storage:
• All storage conditions should be controlled for temperature and humidity. The majority of experts agree on 72 degrees and 50 percent relative humidity. In addition, all paper should remain in the original packaging (carton and ream wrap) until the time of use. The in-plant manager must be particularly mindful of this in humid climates during the summer and in dry climates during the winter.
—Garth Geist, Unisource Worldwide
• Before usage, store the paper in the press room for at least 24 hours, preferably a few days. Optimal average moisture content: 4 to 4.5 percent. Although it is optimum to let the paper cure for about 10 days after printing and before digital operations, that doesn't happen much in the real world environment. Plan for at least a day or two.
—Gerry Rector, Neenah Paper
.
Better Runnability:
• Paper exposed to sudden temperature changes can absorb too much moisture, which may affect image quality and printer performance. Paper should be removed from the tray and resealed in its original ream wrap to ensure optimal print quality and smooth runnability.
—Cindy Hamrick, International Paper
• For better runnability, store digital paper suspended in its original bag/box. A controlled print environment that allows for some dry time after printing and before laminating is ideal. Also avoid very dry or moist printing conditions and follow manufacturer applications guides.
—Meyer Weiss, InteliCoat Technologies
• Moisture is probably the biggest cause of printing problems, so the manufacturer's packaging is important. Keep the paper flat, package sealed and away from being damaged by other equipment. Also, buy the paper in the size that is needed, so that trimming is not required. Trimming can result in some dust and debris that is detrimental to digital press printing.
—Gerry Rector, Neenah Paper
• Paper has a natural tendency to curl, due to the manufacturing process and the hydroscopic nature of cellulose paper fibers. When using digital paper the user must make sure to load the paper into the imaging device with the proper side up. Failure to do this may lead to more frequent jams.
—Garth Geist, Unisource Worldwide
.
Brightness, Opacity, Smoothness:
• Before even looking at surface attributes, take a close look "inside" the sheet, at the formation of the paper. Papers with good formation (even distribution of fibers) provide the best results in digital equipment, with better toner adhesion and smoother solids. High-bright, blue-white sheets give the colors more snap and contrast.
—Laura Shore, Mohawk Paper
• High opacity is best to prevent show through. Select the smoothest, most even formation papers. Superior formation is the best predictor of paper performance in digital presses. Many people think that paper with the highest brightness, and therefore the most contrast, best shows off the colors that are used.
—Gerry Rector, Neenah Paper
• Optical brighteners can enhance brightness of a paper but typically cause paper color shifting over time. These brighteners are not recommended for media used for archiving prints. When examining opacity, keep in mind that the closer a product is to 100 percent opacity, the better the chance customers will have of not seeing what is on the other side of the print.
—Meyer Weiss, InteliCoat Technologies
• Minimum brightness level should be 92 TAPPI GE standard and opacity should be 94 or higher. The smoothness of uncoated and coated papers varies. Uncoated papers should have a smoothness reading of 100 or lower. Coated digital papers should be 1.0 or lower. Also, the higher the brightness, the better the contrast between printed and unprinted areas, and the smoother the sheet, the better the image "lays down" when printed, thus avoiding a rough or mottled appearance.
—Garth Geist, Unisource Worldwide
.
Folding Without Cracking:
• Before folding paper with toner on the crease, apply a flexible overspray that holds the ink or toner in place. Thinner coatings/ films are better as they allow for better folding and don't impact the hand of the print as much as thicker coatings/ laminates do.
—Meyer Weiss, InteliCoat Technologies
• Most digital presses use toner that tends to crack across a fold. If this cannot be avoided by the design, it usually helps to score the paper before folding. If you are going to bind the piece, grain direction is important and binding should be parallel to the grain direction.
—Gerry Rector, Neenah Paper
• Make sure the fold is prescored and that it travels with the grain of the paper. If the user is not sure of the paper's grain direction, try folding the paper lengthwise and crosswise, because paper will always fold more smoothly in the grain direction, or try tearing the paper lengthwise and crosswise, because paper will always tear straighter in the grain direction.
—Garth Geist, Unisource Worldwide
• The best advice is to design the piece so the folds go through unprinted or lightly printed areas. If you must fold a printed area, then choose a very smooth paper, and consider scoring cover weight papers.
—Laura Shore, Mohawk Paper
.
Preprinted Paper:
• Preprinting by conventional printing and then adding personalized data with digital printing is a good second step. The type of paper is dependent on the job and the press. Typically, paper that is high in quality will be guaranteed for both conventional and digital printing. A trial is always recommended and most paper suppliers offer free paper. Avoid using heavily textured papers in digital applications after offset printing. Printing on paper that was engraved, foil stamped, embossed or produced using thermography may cause high-speed copiers to jam.
—Gerry Rector, Neenah Paper
• The in-plant manager should check their ink supplier to select a laser-compatible printing ink. If the in-plant does not have offset equipment, check with a reputable offset printer in your area for recommendations. In many cases, you just might develop a reciprocal relationship and complement each other's capabilities.
—Garth Geist, Unisource Worldwide
.
Laser Paper in Digital Printers:
• The paper for laser printers must be manufactured to a very smooth finish to enable the sheet to handle even the finest graphic detail. Since laser imaging involves heat and electrical charges, paper must contain a lower moisture content than offset papers to transfer and bind the toner to the sheet. This produces the high-resolution image expected when using digital technology.
—Cindy Hamrick, International Paper
• Laser paper is suitable for laser printers and should be fine for most black text printing with ink-jet printers. Don't try to get a photorealistic or glossy print through using laser bond, however, as the color will be washed out and the resolution low.
—Meyer Weiss, InteliCoat Technologies
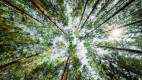


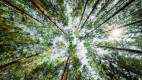
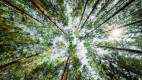
