If you run a lot of 500- to 10,000-page four-color jobs with tight turnaround times and have the right computer skills, digital offset printing may be just what you need.
By Bob Atkinson
In-plants face increasing demands for short-run, fast-turnaround jobs, including full-color work. The problem? The traditional film/plate/ press route is poorly suited for these types of jobs.
New technology has offered some help with this problem, first in the form of computer-to-plate (CTP) systems that eliminate the time and costs associated with film. Then, starting about a decade ago, an even more powerful technology arrived: digital printing, where a RIP computer connects directly to the final output device, eliminating all offline work associated with film or plates.
Two variants to this technology appeared about the same time. High-speed electrostatic copiers or duplicators using solid toner (e.g. Xerox DocuColor) or liquid "electroink" toner (e.g. HP Indigo) are aimed at very-short-run work—500 copies or less in most cases. These devices have done well in the industry, with more than 13,000 installed worldwide today. The quality they can achieve now is certainly impressive, and the range of stocks they handle improves each year. If you're printing just a few hundred (or fewer) copies of a piece, or any job with variable data (where each copy has customized text or graphic elements) then these devices are the best way to go.
The Other Kind of Digital Printing
This article, however, is about the other type of digital printing: digital offset printing (DOP), which uses more-or-less conventional presses, inks and paper stocks. While not as well known as digital copiers and duplicators, these digital presses have quietly gotten better, faster and more dependable each year. They are most cost-efficient on jobs from 500 to 10,000 copies. Above 10,000-sheet runs, conventional presses combined with a platesetter make more sense on a cost-per-copy and total-ownership-cost basis.
A DOP press is a lot like a conventional sheetfed (or web) offset press. It uses plates and blankets, with either the usual 'wet' process inks or waterless inks. So the good news is that you already know a lot about how the press works.
The key differences are the on-board imaging units, the same technology used in many imagesetters and platesetters. Infrared lasers or laser diodes 'draw' the image from the RIP computer directly onto blank processless plates already on the press. On each unit, plates are typically installed in rolls or cassettes of 18 to 36 plates each, and the plates are changed automatically, with the old ones deposited into a used-plate area for removal. The entire plate-change and imaging cycle takes seven to 15 minutes or so on most DOP presses. Then you're ready for the next run. That's a big time savings over the total changeover time required for conventional press workflows, which translates to more jobs per shift, per press and per press person.
The Up Side
Some advantages of this type of press are:
• Lower cost per sheet than conventional presses in 500 to 10,000 job runs, especially in 13x18˝ sizes.
• No time or staff needed for offline film and/or plate production.
• You can make changes in the job right up until the press starts.
• Much faster total job changeover time than conventional systems: seven to 15 minutes instead of 45 minutes or more.
• Most DOP presses are waterless, imaged in perfect register on the press and highly automated, giving you an extremely fast makeready time—sometimes just five or six sheets. This also allows for just a single press operator in many cases and more consistent image quality across the run, even with a less-experienced operator.
• Image quality and stock flexibility now matches most conventional presses.
• Software upgrades can actually improve press productivity over time.
The net effect off all this? More good-looking jobs.
The Down Side
• DOP presses are still about 20 to 25 percent more expensive to purchase than an equivalent conventional press combined with a platesetter.
• If you are not currently running a platesetter or other digital press in-house, there's a whole new set of computer/prepress skills you'll need to acquire: flight-checking files, using a workflow system, running a RIP computer, etc.
• Some components on a DOP press—particularly the imaging units—can't be fixed with a wrench or any other tool in your shop. You need to be guaranteed timely access to all key parts and qualified service by your press supplier.
Key Technologies
More than 90 percent of the imaging units and on-press plates used in the roughly 3,000 DOP presses installed worldwide are manufactured by Presstek, an early innovator in the DOP field. The company's current ProFire Excel imaging units, coupled with processless ProFire Digital Media plates, are capable of 300-line AM or FM screens and run lengths of up to 20,000 sheets.
They are the underlying technology used by DOP presses from Heidelberg, KBA, Komori, KPG, Ryobi, Adast and others. While Creo, Agfa and Mitsubishi are also in the business, they account for a relatively small number of press models, sites and total media volume in DOP.
What's Coming Next?
The MAN Roland DICOweb points to the future: reusable plate systems, with the job imaged right on the press cylinder. A special coating is sprayed on, imaged and the job is run, then the coating is washed off.
Mitsubishi's Diamond 16 Max-V web press project and WIFAG's Evolution 471 system are both heading down this road. High-volume newspaper and commercial web printers are an ideal match for this technology, but expect it to move into the sheetfed marketplace a few years later as manufacturing costs drop.
Is DOP Right for You? If you run a lot of 500- to 10,000-page four-color jobs with tight turnaround times, and you have (or are willing to learn) the computer/prepress skills involved, these presses may be just what you need.
They should be especially attractive if you now use a film/ plates/press cycle. If you already have a platesetter, though, the financial case may be tougher to make. IPG
On The Market
Here is a quick look at some of the current DOP presses, in two-page and four-page sizes:
Adast
www.adast.com/ang/profile.html
547 DI (four-color) or 557 DI (five-color): 14x19˝, waterless, 10-minute total job changeover time, stock up to .016˝, 12,000 sph, optional perfecting and IR dryer.
Heidelberg
www.us.heidelberg.com
Quickmaster DI 46-4 Pro: The current version of the first DOP press to be widely marketed and still the industry leader. This model accounts for about 60 percent of all DOP presses worldwide. Waterless, 13x18˝, 10-15 minute total changeover time, stock up to .016˝, custom plate lengths based on the actual image size to minimize waste, optional dryer.
Heidelberg Speedmaster 74 DI: 20x29˝, four to six colors, 15,000 sph, stock up to .024˝, wet ink process, optional perfecting, coating unit and dryer, total changeover time (four-color) about 10 minutes, can also use conventionally imaged plates
KBA
www.karat-digital-press.com
KBA 46 Karat Plus: 13x20˝, four-color, waterless, total changeover time about 11 minutes, 7,000 sph, optional online densitometer and dryer. This is basically the same press as the Ryobi 3403. KBA also offers the Genius 52, a non DI-version of this model.
KBA 74 Karat: 20x29˝, four-color, waterless, can print on a range of paper stock up to .02˝ as well as PVC, ABS, etc, 10,000 sph, total changeover time about 17 minutes, temperature-controlled keyless inking, optional coating unit and turntable to move to the second pass of a work-and-turn job with very little delay, can be run by a single operator.
Kodak Polychrome Graphics
www.kpgraphics.com
KPG DirectPress 5034 DI: 13x18˝ four-color, waterless press, 7,000 sph, Presstek Profile imaging system (line screens up to 200 lpi), based on the Ryobi 3404 DI press
KPG 5634 DI: as above, but using Presstek's ProFire Excel imaging system (line screens up to 300 lpi and FM screening), changeover/makeready in about 10 minutes, optional dryer and scanning densitometer for ink control.
Ryobi
www.ryobi-group.co.jp/en/projects/ printing/products/01.html
Ryobi 3404X-DI: 13x18˝, four-color, waterless, up to .012˝ stock, Presstek ProFire Excel imaging, optional dryer, 7,000 sph, very similar to KPG 5634 DI above. A UV version of this press is also available for the label/packaging markets.
Screen (U.S.A.)
www.screenusa.com
Screen TruePress 344: 13x18˝, four-color, standard wet ink process, 7,000 sph, AM or hybrid screens, stocks up to .012˝, optional dryer, automatically analyzes every sixth sheet and adjusts ink/water accordingly.
MAN Roland
www.manroland.com
DICOweb Digital Web Press: Roll-fed web press, four- to six-color, wet process, inline dryer, 30,000 iph, eight-minute changeover time, various web stocks in roll widths from 12˝ to 20˝, variable cutoff length and folder, unique reusable plates, where an emulsion is sprayed onto the imaging cylinders, then imaged. After the job, the coating is removed and a new one is applied to the cylinders, ready to be imaged for the next job.
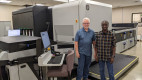



