Computer-to-plate technology has certainly cut a few steps out of the printing process. But plate manufacturers want to eliminate the processing, as well.
By Mark Smith
Computer-to-plate (CTP) production is all about removing steps, variables and labor from the workflow. So it naturally follows that people would look to eliminate the chemistry-based plate processor.
The leading plate manufacturers have very similar takes on the future of this development. Their shared vision begins with a focus on non-ablative switchable polymer and/or on-press development systems.
Presstek, however, is an exception. The Hudson, N.H.-based company has pioneered the market with its current generation of chemistry-free plates and the use of thermal-ablation imaging.
"This (choice) is not based upon an affinity for the technology itself, but rather because we believe this approach offers the best opportunity for chemistry-free and process-free plate products," notes John O'Rourke, marketing director, Digital Media.
Other manufacturers contend that thermal-ablation plates fall short of the grand vision for two reasons:
1) A debris removal system (vacuum and filter) is generally required on the platesetter.
2) Plates must be put through some level of a water wash step after imaging.
Presstek has been working to minimize the process requirements in both areas, O'Rourke says. Its latest "process-free" offering, Applause, actually represents the fourth generation of the technology, he points out.
"Most CTP plate products have a coating weight of approximately 1 micron thickness," O'Rourke notes. "Our Anthem plate utilizes an ablative layer that is 25 microns thick. Applause reduces this by an order of magnitude to .025 micron in thickness."
This improved coating system eliminates the need for any post-exposure treatment (i.e., water wash or wiping), according to the marketing director. It also reduces the impact on the platesetter, he says.
"What we have learned so far is that each imaging platform is unique," O'Rourke explains. "While Applause may require use of a vacuum collection system, we can see an opportunity to simplify the air management system on our own Dimension platesetters, and we expect filter life will be extremely long—perhaps even achieving lifetime filters.
"Beta testing on other imaging platforms is under way, but it's too soon to determine exactly what will be needed in terms of air collection. It's possible that a very simple system will suffice," O'Rourke adds.
Applause's commercial release date has yet to be announced, and the same goes for its pricing. "By eliminating all of the various cost centers around chemical plate developing, we know we can deliver a lower 'plate on press' cost with Applause," O'Rourke says. He expects the plate to be rated for 100,000 impressions.
Controlled Ablation
When it comes to alternative technologies, the distinctions can get a little fuzzy. Fujifilm, for example, is developing a solution employing "controlled ablation" technology, according to Jim Crawford, group manager, Output Media, at Enovation Graphic Systems, (Fujifilm USA) in Hanover Park, Ill. The technology works by having the initial ink charge to the plate carry away undesirable (exposed) material during roll up on press, he explains.
"The advantage of this technology is that the platesetter does not require debris evacuation," Crawford says. "Also, no special laser/imaging systems are needed to image the controlled ablation technology."
The material's current run length capability is in the 25,000 impression range, based on normal press and paper conditions, he adds. An on-press imaging version reportedly is in limited trial with Komori S40D and Heidelberg SM 74DI presses in select markets.
No Ablation
Agfa is pursuing a non-ablative alternative, but its solution differs from the common form of switchable polymer technology, points out David Furman, senior marketing manager, CTP Systems. The company is developing "latex coalescence" technology, he says.
"Our technology is a true lithographic coating," Furman explains. "The image area remains on a grained and anodized aluminum substrate, which acts as the hydrophilic medium."
With switchable polymer technology, the polymer coating is exposed to create image and non-image areas and isn't removed from either, he notes. While the substrate may be aluminum, the polymer controls ink/water balance and that can lead to problems, he asserts.
The working principle of Agfa's processless technology is similar to its existing Thermolite Plus product, for on-press imaging/DI applications, Furman says. The material will be compatible with 830nm thermal lasers and require no add-ons, such as debris removal systems, he adds. Initially, it will be targeted for runs of 100,000 impressions and fewer, with post-exposure requirements and product availability still to be determined, he reports.
Cross-linking Systems
Citiplate is in a unique position because it is concentrating more heavily on being a custom plate manufacturer, says Robert Dainton, technical director.
The technologies Citiplate is pursuing are all photopolymer-based, according to Dainton. This includes non-ablative thermal (830 nm, IR), ultraviolet and violet (30-40 mW) plates.
"They are cross-linking systems," Dainton notes. "In our scenario, the non-image portions are softened by the fountain solution, but removed with the ink and deposited on the paper. That keeps the fountain clean and stable."
Dainton contends that cross-linking offers advantages in durability compared to physical coalescence of the polymer coating. In the latter case, the action of the press or blanket wash can wipe the image off the plate, he says.
Phase-change technology, however, produces a limited hydrophilic contrast on the plate. "Also, no polymer can remain hydrophilic after a certain time on the press. It reverts back, so you run into a run length problem," he says.
Depending on the requirements of the plate, integrated dampening systems on presses can be a challenge for all plates "processed" on press, Dainton admits. A separate dampening system enables the fountain roller to be dropped first, wetting the plate, before the ink roller is dropped and the unexposed polymer is removed. If a press is running an integrated system, the ink and fountain solution are applied at the same time.
Citiplate is looking to support run lengths in the 50,000 to 70,000 impressions range. It has reportedly done production runs of all these plates for review by potential vendors and/or limited field beta testing.
Two Approaches
Lastra America Corp. is dealing with an added complication as it looks to develop processless technology, notes Josh Goodin, corporate research and development director.
"Lastra bought the plate businesses of Western Litho and Mitsubishi Chemical, so over the past year we've been concentrating on integrating the technology we acquired," he explains.
One approach Lastra is pursuing is a switchable polymer product (requiring no post-exposure step) and the other is an on-press wash-off technology, he says. Both are designed to be imaged by thermal IR lasers.
"With the switchable polymer, we are in the early days of product development," Goodin says. "The on-press processable is closer (to commercialization), but we have issues that still need to be resolved. Both materials are designed for short run lengths; under 50,000 impressions is the target."
Kodak Polychrome Graphics also is working on a couple of options in developing a non-ablative, non-process plate, says Jack Weitoff, vice president, plate business. KPG has been working on switchable polymer, or phase-change, technology and "development-on-press" plates.
"We're optimistic about those [develop-on-press plates]," he adds.
Weitoff prefers to talk in terms of the "goal" for product development—that is, to have a thermally imaged product that can be put through a standard thermal platesetter capable of using the "wet processing" thermal plates the company sells today: "The goal is to have a product that is compatible with the broad base of installed platesetters and to use a standard fountain solution on press," he explains
Switchable polymer technology falls short on that last count, since it requires use of special inks and fountain solutions, Weitoff says.
"Also, the visibility of the image after exposure is not so great and the length of run is limited," he adds.
Even given those limitations, "both avenues look interesting," he says. "I expect we'll have a plate on the market sometime in 2004."
Weitoff sees the length of run supported as a critical issue for all non-process plates.
"Initially, these plates will be limited in terms of application because of their run length capabilities. We can produce runs that exceed 50,000 impressions, and maybe up to 100,000 impressions," he says.
That means the technology, at least initially, will be best suited for the small- to medium-sized shop producing short runs, the plate manufacturing representatives all agree. However, run lengths under 100,000 impressions represent the majority of printing sales, they add.
Bucking The Trends
One company looking to buck that trend is PDI Printing Developments. In its quest to develop a processless plate, the company discovered a polymer surface technology that enables fast (typically two minutes or less), one-step processing, points out Tom Bevan, director of sales and marketing. This first lead to the introduction of its Eclipse plate (500,000 impressions with no baking), and now a next-generation version, Delta 830 (1 million impressions with no baking), which was slated to be introduced at Graph Expo 2003.
Both plates use a polymer developed with a solvent, which accounts for the added strength compared to aqueous formulations, Bevan explains. No chemistry replenishment is required in the processor, since the solvent has a very low vapor pressure (minimizing evaporation) and doesn't oxidize, he adds.
These products are still not processless systems, Bevan readily admits. He says the company continues to work toward a thermal, non-ablative plate that would be washed up (or "developed") on press by the action of the fountain solution.
"We wouldn't necessarily take solvent-based technology to a processless plate because fountain solutions are water-based," he points out.
Potential Drawbacks
Agfa's Furman sees processless technology coexisting with the many other CTP technologies available today. "With processless technology, the big benefit is the elimination of chemistry. But, processless does have it's drawbacks," he says.
While run length is an obvious restriction, platesetter productivity is another drawback, Furman contends.
"The sensitivity of processless technology is much lower than that of traditional CTP systems. Platesetter throughput will be reduced (compared to traditional 'wet' plates) by up to 70 percent," he says.
The direct cost for the plate material undoubtedly will be higher, Furman notes, but one will need to factor in other costs like chemistry and process maintenance to really get an understanding of the total cost of ownership for processless plates.
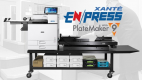




