Computer-to-plate systems have dropped in price and jumped in quality. Take a look at the different systems on the market.
By Bob Atkinson
Computer-to-plate (CTP) technologies have been the norm at large print shops and newspapers for almost a decade. In the past few years, though, competition and new technologies have driven the cost of both CTP equipment and consumables down to the point where they're affordable and practical to any departmental or in-plant shop.
In fact, if you use just 250 square feet of plate material per month—that's about 145 13x19˝ plates or 62 20x29˝ plates, for example—you'll find that the cost numbers work. The higher your plate volume, the more you'll save per month and the faster you'll amortize the hardware purchase.
A few CTP benefits:
• 20-30 percent lower total plate cost
• 40-60 percent less total time to produce a plate
• A cleaner, sharper dot
• Better registration/faster make-ready
• Less equipment, floor space, power consumption
• Optional chemistry-free workflow
A PIA/GATF survey from mid-2005 cites competition/pricing/productivity as by far the biggest concerns among U.S. print shops. CTP vendors agree that their technology is an important step to remaining cost-effective.
"Whether you're a commercial printer or an in-plant producer, you need to be a low-cost producer," says John O'Rourke, director of marketing for CTP at Presstek. "You have to look at production costs, the efficiency and productivity of your operation versus your overhead. This is a major consideration when looking towards CTP, and which system is best for you."
Over at Xanté, Tom FitzSimons is also focusing on productivity with the company's PlateMaker 4 and Impressia two-up platesetters.
"Depending on file sizes, the rating for our our systems is up to 60 plates per hour," he says, "and when you couple that with a press like the [Heidelberg] QM-46, which does the auto plate insertion, that's a very productive shop."
The Downside of CTP?
The initial cost of a new platesetter is anywhere from $8,000 to $150,000, and switching to all-digital proofing (typically with a color-managed ink-jet printer) can add $4,000 to $15,000.
Finding the right system for your in-plant can also be daunting, since no one CTP system is right for everyone. Deciding factors include the length of your press runs, press sizes, floor space, energy and environmental issues—and, of course, your budget.
The current hot market area in CTP is for small and mid-size presses. You now have a choice of platesetter models in two-up and four-up press sizes from 13x19˝ to 21x29˝. Many systems handle two or more plate sizes, giving you increased flexibility.
Plate Material
The two most common plate materials are polyester plastic and aluminum. Polyester plates have traditionally had lower image quality and limited job run lengths (25,000 impressions or less), but that's changing. Current polyester plates are capable of 75,000-impression job runs and 200-line screens—good enough for about 95 percent of the work done in in-plants today.
If, however, your work regularly involves long press runs, corrosive press chemistries (like UV inks) or very high quality images (300-line screens or high-res FM imaging), you'll still need to work with aluminum plates.
Three Coatings
There are three coating (emulsion) types used on CTP plates:
• Silver Halide: This is the same emulsion traditionally used in both photography and in the film and plates for commercial printing. These emulsions are imaged with visible light (from red through the newer violet devices). This plate chemistry is quite sensitive (for fast imaging and low energy use) and capable of excellent image quality. The downside? The plates must be handled under safe lights, and the processing/development of these plates involves environmentally hostile chemistry.
• Photopolymer: These emulsions can be imaged with both visible light and UV light, and their processing chemistry is more environmentally friendly than silver-based emulsions. The downside of photopolymer? Slightly lower image quality and higher energy requirements to image the plate.
• Thermal: This was the first coating used on platesetters, and it still dominates the CTP landscape. It uses heat to image the plates, and offers good image quality, daylight handling, bakeable plates for long runs, and the option for a chemistry-free workflow. The downside? Imaging a thermal plate takes a lot longer (and uses far more energy) than the other two plate coating types. Thermal platesetters are generally more complex and expensive than other types. But if you want the best image quality combined with long job runs and the option to go chemistry-free, thermal is the way to go.
A Chemistry-free Workflow
Processless plates (almost always thermally imaged) eliminate the development step. These were created for use on direct imaging (DI) presses, where the plate is actually imaged on press, but now we see a lot of processless plates for platesetters, as well.
The term processless is a bit misleading, since most of these plates require some treatment after they've been imaged. Usually this just involves a wash stage and gumming. So "chemistry-free" is a more accurate term for these plates—but they still save time, chemical waste and energy. That said, a few plate models actually are ready to hang on the press right out of the platesetter.
For in-plants, the option to go chemistry-free can be a very important one—in addition to city or state regulations, large companies with in-plants often have strict environmental regulations. Presstek's Brian Wolfenden sums up the importance of chemistry-free systems in this way: "One of the most important factors to consider when choosing a CTP system is the chemistry-free option. Presstek offers a totally chemistry-free solution. You image the plate, run it through a tap-water bath and you're ready to print. It's that easy."
Trends to Watch
Some key developing trends to watch in 2006:
1. Watch for the differences (price of equipment and consumables, speed and image quality) between thermal and photopolymer to shrink even further.
2. The two main imaging technologies will remain thermal and violet light. At the moment, violet is gaining some real traction in the small to mid-size shops, because of the lower equipment cost than thermal systems. Ray Cassino, director of Prepress Product Management at Heidelberg explains it this way: "Violet machines are based on internal drums, while thermal-based systems are external drums. Violet systems have 40 percent less moving parts; we know, we make both. So violet offers a significant price advantage to manufacture and a lower selling price for the equipment over comparable thermal systems. And there's no significant difference between violet and thermal plate costs. So at this point, the trend among a lot of smaller print shops is toward the violet technology."
3. Watch for other technologies—the electrophotographic process used by Xanté and the modified ink-jet mechanisms used by JetPlate and Glunz & Jensen, for example—to gain a strong foothold in small to mid-size shops (see sidebar).
4. Look for "processless" to mean just that—no gumming, washing or other tasks after the plates come out of the platesetter. Plates like Presstek's Anthem and Freedom (which require only a water wash) and Applause (no post-imaging processes at all) are leading the way. Presstek/A.B.Dick's two-up Vector TX52 compact platesetter images and then washes Freedom plates inside the platesetter, so they're ready to hang on the press right out of the unit. Another leader is Kodak's Thermal Direct plate, which is also image-then-mount; the non-image areas of the plate wash off in the fountain solution as the press starts up.
.
Sidebar: Ink-jet CTP
While violet light and thermal remain the two key contenders in the CTP market, other technologies are making strong gains, especially in smaller shops. These include the electrophotographic method used by Xanté and a couple of interesting variations on modified ink-jet mechanisms.
Both JetPlate (www.jetplate.com) and Glunz & Jensen (www.glunz-jensen.com) offer ink-jet-based CTP systems, and on the surface they look similar to each other. They both image aluminum plates with a flat-path transport and offer 5-15 four-up plates per hour, based on settings. Both use an external software-based PostScript RIP, and both produce FM images equivalent to a 175-line screen on their best quality setting.
Under the skin, though, they're quite different.
JetPlate offers two models—the 4000 (two-up and small four-up) and the 7600 (four-up). Both use conventional coated metal plates and image the plate with a special imaging fluid, which bonds the emulsion to the plate. Then a regular Kodak developer removes the non-image area. The advantage of this method is that it uses a well-known and proven process. The disadvantage, of course, is that it needs a separate processor. JetPlate has a new model in the wings, the iSetter, which has a built-in plate processor, but as of early February it had not been released.
Glunz & Jensen takes a different approach with its four-up PlateWriter 4200 system. It starts with a plain uncoated aluminum plate and uses its modified ink-jet heads to spray LiquidDot oleophyillic coating onto the image area (this is what holds the ink on press), then run it through a heat-based fuser to cure the plate.
The advantage here is the elimination of the processing stage or need for an external processor. It's still a bit early to say how well these will stand up to long-term use. Potential disadvantages are wear and tear on print heads because of the the special imaging fluid used and drying patterns visible in large solid image areas.
- Companies:
- Eastman Kodak Co.
- Heidelberg
- Presstek Inc.
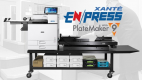




