Web-to-print Caps Digital Overhaul at Mesa College
When veteran print administrator Penny Hedgecoth joined San Diego Mesa College as its Digital Printing/Mail Services administrator, the college’s print department was a completely analog operation. At the same time, budget constraints were making it difficult to replace staff lost to attrition.
Hedgecoth needed to find a way to operate with only six employees while providing better services to the college community. So she made the decision to convert the operation from analog to digital.
“While we have always tried to provide next-day service to faculty and staff,” she says, “it just wasn’t always possible with a manual, analog workflow in place. With the attrition we have had, it was absolutely critical for us to establish a more efficient work process in order to serve the institution and help keep it at the top of the performance list among California community colleges.”
Situated on a beautiful 104-acre mesa in the geographic center of California’s southernmost city, San Diego Mesa College is one of the state’s largest community colleges. It’s a fully accredited, comprehensive two-year college serving 25,000 students, and employing more than 1,000 faculty and staff members.
Hedgecoth joined San Diego Mesa College’s print and mail operation with years of experience in other academic and private sector printing organizations. She applied that experience and a great deal of enthusiasm to create a modern print and mail operation based on a digital workflow.
Digital Upgrade
Her first task was to replace some of the older printing equipment and ensure that all equipment was connected to the college’s network. In 2006, a year after Hedgecoth began at Mesa College, the department purchased three Xerox digital printers: a Nuvera 120, a 4110 copier/printer and a DocuColor 250, which was recently updated to a DocuColor 560. The team was then able to send jobs to the printers digitally. Today, that equipment has been joined by a Xerox 265, a Canon imagePROGRAF iPF755, a Baum hydraulic cutter and an assortment of other bindery machines.
Hedgecoth’s second task was to find a way for customers across the campus to quickly and easily send files electronically for printing.
“In the past,” she says, “most of the work came into the shop on paper. A paper work order was filled out, and the paper originals were copied. This was simply not a sustainable process.”
To create a more productive digital workflow and make its services more accessible to faculty, staff and students, the in-plant implemented EFI Digital StoreFront as its job submission tool in the summer of 2014. Now work is seamlessly transferred from Digital StoreFront to the in-plant’s Xerox color and monochrome printers, often for same-day turnaround.
“We had to undergo a fairly significant justification process,” Hedgecoth says. “Our Budget Advisory Resource Committee looks at the financials but also evaluates how any investment the college makes will benefit students. We were able to meet all of their requirements with our request to implement Digital StoreFront.”
Since adding the Web-to-print solution, Hedgecoth has worked to educate faculty and staff on the new digital process.
“All work now comes in electronically,” she explains. “If there is something on paper, we scan that into the Digital StoreFront library and it is available for production as well as for potential later reprints or repurposing.”
Repeat work is easier to produce now, which is great because it is an important feature for some of the school’s academic programs.
“Our American Sign Language Department, for example, refreshes its coursework every three years, so our system is set up to ensure their content will be available when they are ready to redo their course materials,” Hedgecoth says.
Seamlessly Streamlining
With additional labor resources being difficult to come by, it is significant that a single staff member can monitor all of Mesa College’s Digital StoreFront submissions and queue jobs up for print.
The department plans to move to a new facility in 2016, which will be located in the front of the college and will include a delivery dock. Although the new space will not be larger, it will be designed specifically to house a printing and mailing area.
The in-plant recently started doing wide-format printing with its Canon imagePROGRAF iPF755, and is also now printing for students. The new location will be centrally located on campus, making it easier for students to access.
Most of the work that is completed for students is submitted
in-house from copiers and printers located around the campus. The new location will introduce students to a new way of printing. The Digital StoreFront will be opened to students to use with their personal laptops and computers. Students will be able to print using a Pay4Print card, rather than paying with cash.
Hedgecoth is delighted with how organized Digital StoreFront has made the operation.
“Users only need to create their library once, and then all of their materials are available,” she says. “In terms of workflow, when we leave on a Friday and come back on Monday, there could be as many as 1,000 jobs waiting for us. Incredibly, we can get those jobs out the door and be ready for the next day with a clean sheet.”
‘I Can’t Believe You Did That’
“Feedback from staff and faculty has been great,” Hedgecoth adds. “I can’t tell you how many times one of our customers has said, ‘Wow, I can’t believe you did that.’ It makes the whole crew feel pretty good about their contribution to the college. I feel that our operation has made giant leaps towards progress with Digital StoreFront, providing a more efficient turnaround time to our clients.”
“Since the implementation of Digital StoreFront, I have seen a marked increase in productivity, and even employee morale,” notes Rachelle Agatha, Mesa’s vice president of administration. “Instead of just trying to keep up with the workload, Penny and her staff have started thinking about new products and services and ways to better serve the campus.”
Another productivity enabler with Digital StoreFront is its reporting capability. “In the past,” Hedgecoth says, “it could take someone more than 100 hours a month to assemble the information we needed to submit to accounting for chargebacks. Now we simply generate a report in a few minutes, convert it and send it off. You can’t even compare the two processes.”
Hedgecoth and her team are looking forward to moving into the new facility and making the operation even more efficient. She says Mesa College is pleased with the in-plant’s ability to provide quality products at lower prices than outside printers.
“Already we have the bandwidth to start thinking about new products and services we can offer the college, whereas before, we were just trying to keep up,” Hedgecoth says. “It’s a whole new world for us, and the future is bright.”



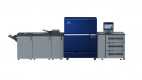

