Shedding A ‘Negative’ Attitude

The definition of bittersweet, from a printer's perspective, is saying goodbye to a timeless but antiquated craft in favor of a more automated, and precise, process driven by computer software. But letting go of a manual process honed through years of experience, is more than offset by the gains offered in the new technology.
Take the State of Colorado's Division of Central Services, Integrated Document Solutions (IDS) in-plant. For years, the Denver-based shop had relied on a traditional prepress plate-making system—masking the plates and using a burner. But the times, they were a-changing. Colorado, like the rest of the country, was pushing for greener, environmentally friendly sensibilities in its manufacturing activities. The shop needed to go green and eliminate prepress and postpress chemicals, and with the pending acquisition of a two-color press, IDS was at a crossroads.
The 22-employee IDS team had relied on a Xanté platemaker, which for years had suited its needs. Longer runs, however, required the ordering of negatives through an outside vendor, and film—not inexpensive and getting harder to find—made for an inefficient process. IDS had actually used a computer-to-plate (CTP) system 15 years earlier, but it had become antiquated and unable to handle software upgrades, so it gave way to the Xanté platemaker. Now it was time for a return to CTP.
"We felt like we needed a lot more ability to make our plates here; we wanted bring that ability in-house," notes Mike St. Peter, IDS production manager. "It was getting really expensive, and film—the old negative process—was going by the wayside. We wanted to get away from all of that. We were working with the Xanté polyester plates for quite a while; it served purposes for small runs. But when it comes to using a two-color press, we were going to require a lot more quality and precision. So we'd need a good plate system."
That's when Mike Lincoln, northern regional manager for the Department of Personnel and Administration (the Division of Central Services IDS regional office) went into research mode along with his key personnel. They visited shops comparable to IDS in size and scope, listened to recommendations and learned the pros and cons associated with their respective CTP systems.
Impressed with Presstek
In 2009, Lincoln found a shop that was looking to sell its two-color press, which included a Presstek Vector CTP system. He was duly impressed. The parties were unable to come to terms, though, so IDS sent out an information for bid (IFB) solicitation. Among the proposals: A two-color Presstek/ABDick 9995 with the chemistry-free Presstek Vector. The shop, which was already sold on the Vector solution, sent its stamp of approval for the Presstek bid to its purchasing department. The press package was formally approved by IDS' parent.
Of all the reasons for IDS to go CTP, the number one objective of performance was fully met.
"The image is very consistent from plate to plate," notes St. Peter. "We like the daylight safe plates. The centering of the image is very consistent. It's almost to the point where we don't have to adjust the cylinders on the press. There's no more storage of plates or negatives. No more chemicals, which is what we wanted."
The installation process was a cinch, according to press operator Pete Vigil. The system was running and producing plates within a day or so, mainly due to the ease of use and straightforward training by the Presstek technician on hand.
"It was mainly a matter of learning the icons, and there weren't many of them," Vigil notes. "It was basically what we were doing on the Xanté—going in, finding the jobs and making the plates."
Trouble-free Startup
The first job performed on the Vector was a four-color poster for the state. IDS coordinated with its team of designers to generate a clean PDF for the Vector to process. The job went off without a hitch. And in the year since it was installed, the Vector has been virtually maintenance free, with the IDS crew handling routine duties such as changing the filters and draining/cleaning the water.
"One of the interesting things is being able to see the image before you make the plate," Vigil points out. "It automatically separates the colors on it to CMYK on the computer. We can break it down, each color, one color at a time, and make one plate at a time."
Joining the 9995 in IDS' facility are a pair of ABDicks—a 9910 with a swing-away T-head for black and two-color printing, along with a 9810 with an envelope feeder that handles a great deal of one- and two-color envelope work. The shop produces posters, calendars, brochures and a variety of work for agencies such as the Colorado Wildlife Association and the governor's office.
Lead press operator Leo Franco loves the Vector's intuitive features. "The computer program itself talks to you and will tell you if the PDF is corrupt in any form," he says. "An alarm will go off, telling you if it's a grayscale, not a solid image. It will tell you if the image is screened, which you can't tell on the computer. It doesn't leave room for error at all."
Franco notes that customers are impressed with the final product. "The quality is phenomenal and our customers have commented on it a lot. We can run high quality, regardless of the volume. It's been a really big boost for us."
During the vetting process, IDS wasn't presented with an option of going the violet plate system route. In hindsight, St. Peter feels his shop made the right decision.
"It didn't look like it was something for us," he says of violet plates. "This all-enclosed thermal unit is really nice. We didn't need any extra yellow lights or materials as far as gumming up the plates. Thermal is really nice and the plates come out great. I've seen the screens on these things. Highest screen we run is in the 150s; it can go quite a bit higher but our presses have a hard time holding the screen.
"I was really impressed with the screen images on this plate material," St. Peter concludes. "It really does a great job."

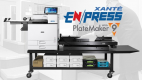




