THROUGHOUT HIS years as director of materials management for the Philadelphia College of Osteopathic Medicine, Dean Gray has always used a mix of coated and uncoated paper.
Recently, at the request of a designer, he switched the annual report—traditionally printed on coated paper—to uncoated paper. The results were pleasing.
In fact, by printing on uncoated stock, the in-plant met the PCOM marketing department's goal of softening up the annual report's previously stiff and formal look.
"It gives an air of less formality and stiffness," Gray notes.
For years, using uncoated paper meant taking risks on quality. That is no longer the case due to innovations in paper-making, printing and ink technologies. As more designers see the success of printing on uncoated paper, Gray feels, they will specify more jobs on it.
Switching to uncoated paper at PCOM required a few modifications. Chalking was one of Gray's challenges, and he had concerns about scuffing as the uncoated sheets went through the bindery process. He has found that, in dealing with uncoated paper, he must have more inks formulated to avoid chalking and enhance drying. And he has to adjust the screen—sometimes to 250—to compensate for dot spread.
The in-plant, Gray says, had no press challenges. It printed the job on a five-color Heidelberg Speedmaster SM 74.
Uncoated Advantages
Historically, uncoated paper was the only choice until the 1860s, when layers of clay, binders and additives were used to improve printability and appearance, according to the Weyerhaeuser Co.
Those who formerly believed high-end printing could only be achieved with coated papers are amazed to discover the advantages and value that uncoated paper offers, notes company spokesperson Mary Jean Cashman.
"With a new organic trend to colors and the influence of recent economic conditions, uncoated papers are making strides in popularity," she says. "When you need a high gloss, that's certainly a time to use a coated sheet. But there's so much more opportunity with uncoated papers—not mentioning the initial dollars saved."
One of the differences—obviously—between coated and uncoated paper is the coating, with sheets coated either on one side or both. Different sizing (treatment to give paper resistence to liquid penetration) may make a sheet smoother and appear shiny, but that's not because it's coated, notes Christy Zukowski, marketing communications manager with Boise Paper Solutions.
"I think the primary reason folks would gravitate towards an uncoated sheet would be it's less expensive," she says. "A lot of the inks and toners applied on these sheets come out looking shiny, so it gives you that more upscale look, but you're not paying for that coated sheet."
Another factor is the press, which dictates the type of sheet printers should be using, she says.
"There are ways to curb costs by selecting a color copy paper with high brightness and nice smoothness that would work well with those inks and toners in order to achieve the best results at a lower expense rate," she says.
Jim Kohler, a graphic arts and printing scientist with Hammermill/International Paper, says one advantage of uncoated paper is that there is much more stock availability, especially on smaller sizes.
"A lot of the coated stock is made for folio size—sizes larger than 11x17˝, 19x25˝, 20x26˝, 35x40˝ and such," he says. "Uncoated stock has far more sizes, colors and textures, so that's a real key there."
Lynda Ramsey, director of printing papers at Weyerhaeuser, says increasingly more printers and paper specifiers are choosing uncoated sheets, and manufacturers are responding with uncoated paper that's competitively priced with coated free sheet papers.
Zukowski notes many in-plants are now using a lot of uncoated cut sheet paper. In response, the company is supplying an array of uncoated grades, from multipurpose use to higher-grade color copier paper.
Weyerhaeuser offers a three-book series titled Weyerhaeuser Paper University, which offers printers instructions on how to print on uncoated paper, covering a variety of topics from how paper choice can convey a mood to the relationship between ink and paper and exploring advanced printing techniques on uncoated paper.
Kohler believes a piece of paper is a selling point.
"Coated paper, to me, always implies class, but it's kind of cold," he says. "Uncoated has a warmer feel to it, it's more personal."
Plus, the feel of the paper also is different, Kohler points out.
"Uncoated has that soft feel, and you can get it in more textures and colors than you can in coated sheets," he says. "Coated sheets tend to be smooth."
Laura Shore, vice president of marketing communications for Mohawk Fine Papers, adds that uncoated papers offer a variety of colors, visual effects and surface textures—including smoothness.
"Different degrees of smoothness are achieved in a process known as calendaring, the last step in paper making when the paper is run through a stack of large steel rollers with different surfaces," says Shore. "These rollers or calendars tighten the fibers and smooth the paper. Common finishes for uncoated paper, in order of increasing smoothness are: eggshell, vellum, smooth and super smooth or ultra smooth."
In contrast, coated paper comes in a narrow range of colors, such as white and ivory, and has limited surface finishes such as satin, matte, dull or gloss.
"Images printed on calendared smooth uncoated papers are sharp—if not sharper—than those printed on a calendared coated paper with a dull or matte finish," Shore says.
Coated Class
Not all in the industry agree.
Dennis Essary, director of office papers for Stora Enso North America, says uncoated paper delivers "bulk and stiffness" versus coated at the same basis weight.
"Coated paper delivers higher print quality and a higher value perception to your customer," he says.
He believes the smooth printing surface of a coated sheet allows inks and toner to lie more uniformly.
"It provides greater contrast and fidelity," he says. "Your print image will have more snap on coated paper."
In switching a job from coated to uncoated, changes in prepress focus on line ruling, Kohler says.
"For example, on coated, you might run 200 lines per inch but on an uncoated, you may run 150 to 175, depending on the type of pressure you have," he says.
It's also dependent on the press itself and whether one is using computer-to-plate or film. Using proper adjustments, one can use uncoated paper for stochastic printing, he says.
While there may be disagreement on the qualities of coated versus uncoated, there is no disagreement that the major consideration when using uncoated instead of coated paper centers on ink.
"Obviously, coated prints better than uncoated solely because it's got the coating on the top side of the sheet, so the ink stays right on the surface," says Kohler. "You generally use less ink on the surface."
With ink saturating more into uncoated paper, it takes more ink to print an uncoated sheet, he points out.
For instance, a coated sheet will run a black ink density of l.6 or l.7 compared to 1.1 for uncoated.
"When you run a coated sheet, you run less ink but get higher ink densities," he says. "When you switch to uncoated you've got to open up your ink dams a little bit."
Shore points out that coated paper was an early solution to dot gain. Dot gain is when a dot or drop of liquid ink spreads like a drop of watercolor falling from a paintbrush onto an absorbent sheet, such as uncoated paper. It's a situation for which printers must compensate, she says.
Shore says that when a photographic image printed on uncoated paper includes a shadow, the ink in the shadow areas can build up on the press and become mottled. The solution: under color removal (UCR) or gray component replacement (GCR).
Heavy ink coverage on uncoated paper can sometimes rub off or offset on the sheet next to it in a post-press stack. Various coatings, such as varnish, aqueous and ultraviolet, will seal the ink to prevent rub-off.
Dry time is another consideration.
"Coatings have a capillary action to them, so they absorb oils very fast from the ink," Kohler says. "Once the oils are removed, the resin particles are left available to oxygen and it dries. With uncoated paper, the smoother the sheet, the tighter the sheet is and the longer the ink-drying time."
Kohler says "toothy stock" will use more ink, but dry quicker because the oil is going to absorb into the open structure of the sheet.
"With a very smooth sheet, it's going to take a longer time for those oils to saturate in the sheet, so drying time is extended," he says.
Tips for Using Uncoated
Kohler offers the following tips for switching from coated to uncoated for a digital job: "Make sure your stock is digitally qualified. If you see a sheet that says 'digital guarantee,' you assume it can run on all digital equipment, and that's not necessarily true. Some are designed more for ink jet, some are designed for lasers and ink jets."
For example, while one of his company's papers is guaranteed to run through a laser and, in most cases, an ink-jet printer, it cannot be used in a large Indigo press.
"The term 'digital guarantee' can be a little misleading at times," he says. "You have to make sure the paper's going to work not only in your press but in your laser equipment."
As for inks, make sure they're laser-compatible and won't melt the fuser, Kohler advises.
Essary believes if printers use a coated stock on a digital job, they will maintain their equipment performance while delivering better print quality.
Tips for Coated Paper
When using coated paper on digital printers, Kohler advises printers that sheets need to be stable enough to go through the machine.
"We have tested sheets we thought were guaranteed, and when it ran through the fuser, the coating melted," he says. "I always recommend to people that if they've never run a product before in the type of device they're running, try it out first."
In digital printing on coated stock, Essary says it's imperative to use a coated sheet specifically designed with the bulk, lay-flat and dimensional stability to function appropriately through a variety of digital printers or presses and maintain superior toner adhesion.
--By Carol Brzozowski
.
Sidebar: Making Uncoated Sheets Shine
According to Laura Shore, of Mohawk Fine Papers, different types of ink and methods of applying it can produce great effects on uncoated paper.
• Semi-transparent and naturally bright, fluorescent inks increase the clarity and brightness of images printed on uncoated paper.
• Touch plates or bump plates use one unit of the press to apply extra ink only to those areas of an image requiring a special "pop," such as fluorescent.
• Though it has higher ink and printing costs, Hexachrome—a six-color printing process that adds green and orange to cyan, magenta, yellow and black—is brighter, cleaner and more vibrant than CMYK.
• Enhanced black—a denser, richer black achieved with two hits of black or process applied over 50 percent cyan—adds drama and contrast for a bit more cost.
• The smoothest uncoated papers deliver the best results when using metallic inks, which are best applied with dull varnish or dull aqueous for rub protection.
• Though more expensive and usable only on specially adapted presses, UV inks produce the sharpest images, leaving little time for dot gain and eliminating the need for a varnish or aqueous coating.
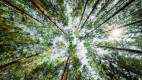


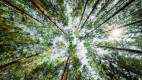
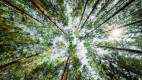
