With color copier technology improving daily, what's in store for black-and-white?
Duplicating speeds and paper capacity were the specs by which black-and-white copiers were evaluated in the past. Today, customers want scanning, Internet connectivity and e-mail capabilities—not to mention mega speed.
And, they want color.
In a world where color has become a phenomenal communications tool, what is the future of black-and-white copiers?
Surprisingly, it will be color that has to compete, according to several leading printer/copier manufacturers, including Canon, Konica and Minolta. These experts—which sell both color and black-and-white devices—feel the future of black-and-white looks quite bright, indeed.
Black-and-white copiers offer faster speeds, greater affordability and a range of features and finishing options not yet available on color machines. Black-and-white's stronghold on the market will not fade away...at least, not any time soon.
"Certainly color is making inroads," says Dennis Amorosano, director of marketing for Canon USA Copier and Networked Office Systems Division. "But color is still more expensive, and not every application can justify the cost. Also, you can't get the speed with the reliability of black-and-white.
"Color still has a long way to go before it can truly compete with black-and-white," he continues. "So I don't foresee any wholesale shift anytime soon."
In the meantime, both the black-and-white and color copier markets are in a transition period.
"In the past, color product sales have been limited because color products simply couldn't compete with the speed, finishing capabilities and cost of black-and-white systems," explains Steve Pearl, Minolta's group product marketing manager of black-and-white, fax and MFP. "Today, both markets are in transition because the speeds of color systems are increasing, the finishing features are being made available and system prices are declining.
"However," Pearl continues, "color technology is not yet at the point where there is a hybrid system that can match the functionality and price of many black-and-white systems. This is especially true for production environments, such as in-plant printers who have the volume to support very fast black-and-white systems. Black-and-white printer/copiers still have a speed advantage over color copiers and are still able to offer a wider range of finishing capabilities."
Interfacing And Internet Connectivity
Today's printer/copiers are being transformed into communication hubs that can distribute documents in different ways, and can even interface with the Internet. For example, a document can be scanned on a digital copier, then sent over the Internet to an e-mail address from the system's control panel. This offers an inexpensive and convenient alternative to faxing or mailing.
"Digital systems allow businesses to reproduce documents, transfer electronic documents to paper, convert hard copy documents to electronic files and send documents to remote locations," says Minolta's Pearl.
Kevin Kern, vice president of product development and support at Konica Business Technologies, encourages in-plants to take advantage of digital copiers.
"Digital capabilities, black-and-white and color, afford huge opportunities for in-plant printers," says Kern. "Speeds are increasing, prices are decreasing and capabilities are growing, all of which provide exciting strategic opportunities for the in-plant shop, as well as the company as a whole.
"The in-plant print shop is becoming more strategic to the entire operation than in the past, mainly because reproduction is becoming more important," Kern continues. "Individual departments that used to outsource are now keeping more of their print work in-house. Because in-plants have the expertise in producing the best quality at the most reasonable costs, they're saving their companies money. Thus, their role is changing; it's becoming more strategically important."
On The Network
Network connectivity is also strategically important to companies, and copiers must offer this capability to survive in today's virtual world.
"You have to be able to hook [your copier] to the Internet today or you can't get in the conversation," notes Canon's Amorosano. "There's also a significant interest in a machine's ability to scan and turn items into digital format. For example, some customers want to scan and store documents. Others want to scan, then distribute documents in a more cost-effective way than fax or Federal Express.
"We're starting to see a real demand for scanning," Amorosano notes. "In the next two years, of all the functions, scanning will be one of the key areas driving the marketplace."
Scanning also eliminates the need for a recirculating document handler, Kern adds.
"On analog copiers, originals have to go back to the document holder. With digital [copiers], scanning places the image into the machine's memory and prints it from memory rather than recirculating the document. This saves wear and tear on the document, and the reproduction quality is better."
While digital technology, Internet connectivity and scanning top the list of new features, Océ reports that multifunctionality is another growing requirement.
"Customers want scanning, copying, printing and finishing in one device," explains David Schumaker, vice president of marketing for Océ Document Printing Systems. "Scanning to an archive for easy transformation of analog documents into digital files and, later, retrieval is also highly desirable."
Océ and Canon are working with a company called eCopy, which has developed software that lets users scan paper documents on digital copiers, then send them via e-mail, fax or secure electronic document delivery services instead of printing them.
Most of today's in-demand features relate more to printing needs than copying needs, contends Pearl.
"A few years ago, first-copy-out time, duplicating speeds and paper capacity were the specifications on which copiers were evaluated," he says. "Now, customers are asking about a digital copier's Internet connectivity and e-mailing capabilities. They are also asking about RIP times, processing power and who makes the controller."
In-plants not only have large volumes, but are often asked to satisfy a number of customers' needs. New units have speeds of 70-plus pages per minute and, more importantly, come with finishing options and output controls that allow in-plants to meet those varied needs. Optional folders, trimmers, staplers, saddle stitchers and three-hole punches are all in demand, even on slower copiers. Saddlestitching is now available on some 45-ppm systems.
Several manufacturers, including Minolta and Konica, predict the 70-plus-ppm environment will grow, particularly in in-plants. Kern claims industry forecasts are calling for 2 percent growth this year and 8 percent in 2002. This notable growth will be the direct result of cluster printing, which enables faster reproduction speeds, he says (see Cluster sidebar, next page).
Large-capacity document handlers, which hold 11x17˝ paper, are now standard on high-end machines. However, some manufacturers have gone a step further and developed extra large capacity trays, holding oversized paper up to 12x18˝ and 6,000 sheets. This feature, requested by in-plants, Kern says, is being incorporated into black-and-white machines. Combine this with inline finishing, and 12x18˝ booklets can be produced as part of the copy or print function.
Another unique feature is post-process sheet insertion that allows color covers to be inserted into black-and-white documents. Text and cover are pulled together in the finishing process.
Still other advancements are starting to command attention, such as front-end enablers and document management capabilities, which Russell Marchetta, Ricoh's public relations manager, reports are being incorporated into the latest Ricoh models.
Built-in Maintenance
Most manufacturers acknowledge that a certain amount of printer/copier problems are inevitable.
"No system will run perfectly forever," concedes Pearl.
To improve maintenance response times, Minolta developed a remote diagnostic system that monitors the use and performance of Minolta systems and can automatically send an e-mail to the dealer when a problem occurs.
"Automatic notification shortens the time it takes for a dealer to be aware of an issue and also better prepares the technician for solving the problem," Pearl says. The diagnostic system will be released later this summer.
Konica has developed proactive maintenance programs and trains its service technicians to maintain equipment on a proactive instead of reactionary basis, Kern says. The company also offers maintenance tracking on its machines.
Océ, setting the pace for prompt service response, now offers cell phone responses from technicians. Schumaker reports that an estimated 20 percent of maintenance calls are resolved via the telephone.
Additional Reading
- Companies:
- Canon U.S.A.
- Ricoh Corp.



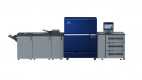

