Amway: Consolidating to Expand
When Amway’s in-plant installed a new six-color KBA Rapida 106 offset press a year ago, it served as the capstone of a two-year, $10 million upgrade that was both an expansion and a consolidation.

Outside Amway’s corporate headquarters. From left: Dave Wolters, manager of manufacturing production; Jon Collins, director of global manufacturing strategy; and Jim Brundidge, plant manager.
For years, the nutrition, beauty and home products company ran two separate printing divisions: one for packaging and one for general printing/literature. Consolidation into a single Paper Products printing operation was intended to allow the in-plant to optimize resources, balance workload and maximize workflow efficiency.
The two discrete printing plants were producing plenty of work overall — catalogs, magazines, brochures and other business materials on one side, and folding cartons and pressure-sensitive labels on the other. However, inconsistent volumes created production peaks and valleys.
“During those peak periods, such as during catalog production, we were too busy, while we would have to shut down equipment at other times,” recalls Joyce Wallace, supply chain account manager for Paper Products.
Related story: Amway In-plant Adds Six-color Press
Concurrently, some of the in-plant’s major equipment (including a pair of web presses) was aging out, so the time was right to make changes. It would be a tremendous undertaking, yet a fairly short move in terms of physical distance.
A Massive Operation

(From left) Rob Dargie, Amway engineer; Greg Schiefelbein, regional sales manager for KBA North America; Cory Pease, Amway group leader; Dave Wolters, Amway manager; and Denny McQueen, Amway engineer, join the Amway team at Amway’s headquarters.
Amway’s in-house printing capabilities are located in the company’s corporate headquarters complex, which spans more than 3 million sq. ft., in Ada, Mich. Founded in 1959, the company is one of the most successful direct-selling businesses in the world, with more than 19,000 corporate employees and millions of distributors worldwide.
The former literature printing operation was moved about three-quarters of a mile within the complex to the packaging area. First on the list was to expand the old packaging area to house the division’s packaging equipment along with the bindery equipment from the old literature area. Five brand new pieces of equipment were then brought online as the new facility emerged.
Along with the new equipment, the expanded facility houses two narrow web flexo carton presses with in-line diecutting, two sheetfed diecutters and two folder-gluers. The area also is home to two full size saddle-stitchers, three buckle folders, two ream cutters and various shrink-wrapping equipment used for bundling and packs. There is also a large hand-assembly area.
“This expansion allowed for a much better flow between all of the equipment,” Wallace adds. The digital print center and prepress department were also moved to new locations.
There was no shut down or interruption of service during the move, Wallace stresses.
“We would move one piece of equipment and get it up and running before moving to the next,” she says. “That’s why it took as long as it did. It was a priority that the move would not have an effect on customers.”

Clad in a hair and beard net because the plant produces food and drug packaging, Operator Mark Marentette stands near the shop’s MBO M80 folder.
During the installation of the KBA press into the 166,000-sq.-ft. consolidated operation, the in-plant kept an aged Heidelberg press operational in the original packaging facility. Once the new press was up and running, the Heidelberg was decommissioned.
A Versatile Press
The versatility of the KBA offset press makes it a perfect fit for the new in-plant. The press has the capability to run “onion skin” to 50-point board. The current workload includes literature items on thin paper stock and laundry soap cartons on 30-point board. The press also has expanded capabilities for varnishes and coatings as it can print with both conventional and UV ink.
Thanks to those upgrades, she notes, a catalog customer was able to bring high-end cover design and production for its beauty, health and nutrition catalogs in-house for the first time.
“Without the KBA, we would have had to outsource the cover, and then bring it back in for stitching,” says Wallace.
The in-plant also invested in a high-speed MBO M80 folder, with front-end pile feeder and back-end log builder, designed specifically to fold 16-page signatures for catalogs.
Meanwhile, the division’s pressure-sensitive label business was completely overhauled. A combination offset/flexo press that was not efficient for multiple-market short label runs was replaced by a digital label operation that includes an HP Indigo WS6800 and an A B Graphic
Digicon Series 3 diecutter and coater. The old rewinder was also replaced with a slick new one from A B Graphic.“The KBA, the HP Indigo and the ABG equipment have us well positioned to support the Amway business and our independent business owners with top quality print and packaging for many years to come,” declares Plant Manager Jim Brundidge.
Wallace describes the quality of the new HP as steady, consistent and amazing, noting that, “registration and color consistency problems just go away on digital.”
Cost savings is even a bigger driver, though. “The digital process is efficient on very short to medium long runs and will save the corporation by reducing inventory and disposals due to unforeseen artwork and regulatory changes,” Wallace adds. “The quality and efficiency of this process will allow us to bring our Nutrilite vitamins and supplements labels in-house for the first time.”
With so many functions under one roof, the in-plant sees the value of cross-training its employees (approximately
115 full-timers plus 20-30 temporary employees). “Flow to the work” has become a catch phrase around the operation to describe the new philosophy of training printers and operators to be more flexible in order to manage the ups and downs of daily demand.
an internal slogan describing the optimization process — and better serve all of their internal and external print customers. first refusal and takes pride in earning its work and customers — and it’s earning plenty. In 2015, Paper Products reported $39 million in revenue from 5,030 orders and 263 million total units produced. Major literature jobs include eight language versions of three main catalogs with an average run of 150,000 and an overall quantity
Group leaders, account managers and schedulers are also optimizing processes to become “One Paper” — an internal slogan describing the optimization process — and better serve all of their internal and external print customers.
The in-plant does not have the right of first refusal and takes pride in earning its work and customers — and it’s earning plenty. In 2015, Paper Products reported $39 million in revenue from 5,030 orders and 263 million total units produced. Major literature jobs include eight language versions of three main catalogs with an average run of 150,000 and an overall quantity of 3.2 million.
In addition, the in-plant also insources a significant amount of print work — about 35% of its total production.
“We contract bacon boards, popcorn boxes, guitar string sleeves — whatever looks like printing,” says Wallace. “That helps further with those peaks and valleys and spreads out costs, making our internal work less expensive.
“Understanding the financials and running the business as much like a commercial printer as possible has always been a high priority,” she declares. “That, along with the very best customer service in the business keeps customers coming back and print orders coming in.”




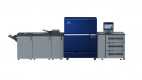

