One of the biggest challenges an in-plant can face is shifting to an all-digital workflow. But most of the time, say these managers, it's worth it.
By Mike Llewellyn
Over the course of his 30 years in printing, Dan Dore, operations supervisor at Johns Hopkins University's Applied Physics Laboratory (APL), has seen it all. He was there for the rise of offset lithography. He saw the advent of digital printing. And now he's guiding his in-plant into an all-digital workflow.
By the end of this year, all of the federally funded in-plant's offset equipment will be sent off to government surplus, and the shop will focus exclusively on high-speed digital printing and duplicating, print-on-demand and copying. Dore says the benefits for the Laurel, Md., in-plant, and for APL, are clear.
"A good deal of what we were printing on offset were runs of less than 5,000," he says. "That's just not economical, especially since we're now doing print-on-demand."
For example, Dore says the in-plant used to output the 300-page employee handbook to a platesetter, print it two-up on a two-color press, then have it cut off-line and collated.
"But now we're just taking the PDF and printing exactly the number they need, and usually an extra 20 or so," he says.
With run lengths dropping, and customers' speed expectations getting ever more stringent, many managers find that their in-plants' offset presses are becoming specialty items. And for those in-plants that don't require massive print runs, or even those that find they can save more money by outsourcing that work, an all-digital shop has become an attractive goal.
"When we can bill less to the customer and turn jobs around faster, the institution always benefits," says Barbara Lindsay, assistant director of Printing Services at Georgia Perimeter College.
With a brand new HP-Indigo 1000 digital color press in the Clarkston, Ga., facility, Lindsay says the five-employee in-plant decided to sell off a two-color press and reroute all of the color work the shop would have run on that press to the new digital printer.
"The workflow with the Indigo worked so well," she says. "We could have kept the press, but there was just no reason to."
An increasing amount of four-color work was getting outsourced, Lindsay says, so the press was simply becoming underutilized. With the new HP-Indigo press, she adds, about 100 of those 130 or so previously outsourced jobs will be brought back in-house.
Getting Started
"This is all still fairly speculative for us," says Lindsay of the new digital press, "but when we did the ROI, [going digital] was a no-brainer."
In addition to cost savings, the simple physical constraints of the facility made investing in digital technology look like the only route for the in-plant to take.
"We don't have room for a four-color press," she explains. "We're a relatively small shop."
Lindsay also points out that even if a four-color press could fit in the facility, she only has one operator to run it.
"And it's very difficult to run a four-color press with one pressman," she says.
Lindsay doesn't expect too many customers to fret over the fact that their jobs will be moving from an offset press to a digital printer.
"With the Indigo's quality, these folks aren't going to be able to tell the difference," she says. "The quality is beautiful."
To make sure there were no surprises, though, she brought the designers from Public Relations along to the HP-Indigo demos, where digitally printed samples were laid down next to offset-printed versions.
"We could not see significant difference," she says.
The in-plant at Johns Hopkins University's Applied Physics Laboratory also added new digital equipment recently—a two-color digital duplicator to handle the envelopes that used to be outsourced.
"So now we can do very short runs," Dore says. "The quality isn't quite as good as offset, but it will do."
Additionally, the in-plant is looking forward to upgrading its Xerox DocuColor 12 and DocuColor 40 to a DocuColor 6060.
A Mandate To Go Digital
But these managers know that a transition to digital is more than just equipment—it's a new approach to running an in-plant.
Inspired by their tour of an all-digital Florida in-plant, administrators at Portsmouth City Public Schools, in Virginia, started fresh by hiring Manager Dan Pothier back in 1998 specifically because he had the experience to make the shift to digital happen.
Although the in-plant still runs a very limited amount of work off a one-color Multilith and a two-color Ryobi, Pothier says 90 percent of the work that was being printed on offset presses before 1998 is now printed digitally.
"And 80 percent of that went to digital duplicators," he says.
The first benefit of switching to a digital workflow for the in-plant was the streamlining it offered between printing and mailing.
"A lot of the jobs that were printed on offset also required mailing," says Pothier. But now, the use of high-speed laser printers lets jobs flow smoothly into the mailing operation.
The shift to the new technology was welcomed by the in-plant's customers, he says, not only because of the speed at which jobs could be turned around, but also because of the accuracy.
APL's Dore agrees that customers are well served by his in-plant's move toward an all-digital workflow. The in-plant designed the move to appeal directly to what customers have been looking for, he says—for starters, competitive prices.
In addition to offering cost-effective print on demand and the opportunity to post PDF versions of jobs online, the in-plant had to address high-volume printing, Dore explains.
Digital: Meant To Be Sometimes, it seems, fate plays a role in the wise management of an in-plant. In 1992, a roofer's truck caught fire and destroyed most of the facility and equipment at Oregon State University Printing & Mailing Services' offset operation. Seeing the replacement of the offset equipment as a cost impossible to justify, the school's administration ruled that the Corvallis, Ore., in-plant would forever more be a strictly digital shop. Soon enough, two Xerox DocuTechs were brought in to replace three production copiers, four presses, two plate makers and two collating systems. All of that happened before Manager Jean-Luc Devis arrived, but he says the fire positioned Printing and Mailing Services for future growth and quite possibly saved the in-plant from going out of business. Since then, Devis says the digital workflow has brought the in-plant two major advantages. "First, the results were improved quality, a 30 percent increase in volume, faster job delivery and a 20 percent reduction in staff," he says. Second, he adds, because the digital printers allow the shop to print straight from a customer's file, the in-plant no longer has to operate two separate processes. Devis says there is no reason to burn plates for a press in addition to operating digital printers. "And now as offset becomes more automated and the quality of digital printing rises, the two are getting much closer in quality," he says. "So there's no need to invest in those separate workflows." Today, the 26-employee in-plant at Oregon State runs two Canon imageRUNNER 110s, a Xerox DocuPrint 92C for highlight color and a Xerox DocuColor 2060, among other smaller equipment. To be sure, there is still a great deal of offset work that comes through the shop, but Devis says the in-plant outsources the work, which accounts for about 25 percent of the in-plant's total revenue, to partnered printers in the area. Rather than purchase an offset press to bring that work back in, though, Devis says the in-plant is in the process of conducting a feasibility study to decide on the acquisition of a new digital press. An HP-Indigo, NexPress or iGen3, he says, will do wonders both for the in-plant's productivity and its ability to expand current variable data capabilities. Today, the 26-employee in-plant at Oregon State runs two Canon imageRUNNER 110s, a Xerox DocuPrint 92C for highlight color and a Xerox DocuColor 2060, among other smaller equipment. |
"So we adjusted our pricing scale to be comparable to offset," he says, citing the fact that at higher volumes offset printing traditionally has been more cost-effective.
"Because the commercial market has lowered its digital prices, we've lowered ours, and now the [prices of digital and offset] are very close," he says.
A positive response to the in-plant's efforts was almost immediate.
"We've saved money. There's a quicker turnaround time. With print-on-demand they can do updates more often," he says. "This has certainly raised our visibility."
Advice From The Pros
To replace the wealth of offset equipment the Portsmouth City Public Schools in-plant sold off, Pothier says the shop has relied most heavily on two Heidelberg 9110 digital printers. He says that while the in-plant lost money by selling the equipment, the presses were old and worn out, and would have needed to be replaced anyway. Additionally, the use of digital printers easily won back what losses the shop incurred.
One important lesson to learn, though, says Pothier, is that while it's often wise to purchase an offset press, large digital equipment should never be bought outright.
"I don't ever buy digital equipment because it becomes obsolete too quickly," he explains.
When the time comes to decide whether or not to guide an in-plant from an offset workflow to an almost all-digital workflow, Pothier says there are a few simple rules to keep in mind.
"You just have to look at your overall labor: What does it take to get something done? The fancier the equipment is, the more expensive it is, so you have to find your cutoff point," he says.
Pothier points out that the labor required to run an offset operation is largely eliminated when an in-plant brings in digital equipment. He also notes that with customers becoming increasingly accustomed to the personalization made possible by their own computers, they'll expect the same from in-plants.
Georgia Perimeter College is already focusing on personalization and one-to-one marketing using its HP-Indigo 1000 press. The in-plant is beginning to partner with a number of departments on campus to offer variable data printing.
Barbara Lindsay believes variable data printing is one of the best reasons to invest in an all-digital workflow. It helps show that the new equipment can expand the in-plant's services.
"This has to be more than just another way to print the same stuff," she says. "And now it's just a matter of pulling together the data from departments like Admissions, Institutional Advancement and Human Resources."
For all of these managers, finding ways to meet their customers' developing needs is in some way predicting the future. By providing a tight, low-cost operation that can also mesh easily with institutional computer systems, they are bringing to bear the flexibility that grants an in-plant a long, healthy life.
.



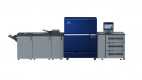

