Paper Inventory Management: A Lean Approach
AN IN-PLANT is a perfect candidate for applying Lean production practices. We are essentially a manufacturing environment that uses multiple steps in various processes. We utilize a variety of equipment, technology, human resources and supplies. There is an ever-present risk of waste and errors, and quality and speed are at the forefront of our concerns.
One of the best features of Lean is its low-cost approach to quality improvement. Lean philosophy forces you to come up with affordable solutions and avoid purchasing expensive equipment or implementing costly systems to tackle performance or quality issues. As a government-funded health care organization, we have embraced Lean for this very reason.
When the two print shops of the McGill University Health Centre, in Montreal, Quebec, merged in September 2009 and relocated to an office building, we took the opportunity to do some housekeeping. An initial sorting of unnecessary and outdated supplies was done at the old locations and the rest was packed and shipped to the new location.
In a mad scramble to get the shop up and running, the paper was placed on shelves or stacked in designated spaces with only a basic plan. Having just entered one of the busy seasons, our first priority was to provide service, and doing it while adapting to our new environment proved to be quite a challenge. So for the next few months, staff was running around hunting for paper and finding it in more than one location. Out-of-stock panics were becoming routine, and our coordinator was going nuts.
Very Busy Operation
Our in-plant provides printing services to six hospitals plus four external health care establishments. It produces more than 20 million impressions per year, with jobs ranging from forms to wide-format. Two Xerox Nuvera printers operated by one technician share the bulk of that volume; the two offset press operators run a Multilith 2650 as well as a Ryobi 3302. Digital color is handled by one employee operating a Xerox DocuColor 252 and a 700.
The department is staffed by eight employees, six of whom are in production. One employee performs prepress tasks while another handles job requests and various other office duties. One of those duties is ordering supplies such as paper, toner cartridges, inks, etc.
Like most shops, the paper we use most is 20-lb. bond, which accounts for probably half the volume. The rest of the paper is quite varied and includes pre-punched three-hole and five-hole paper, colored bond, carbonless paper (both pre-assembled and unassembled), fine papers, label materials, digital papers, card stock, etc. Total inventory at any time is approximately $70,000.
For years our inventory management system relied essentially on visually checking our shelves and taking notes of what needed replenishing. An employee who required a certain paper stock for a job would scribble it on a piece of paper and hand it to the coordinator who would flip through a card system, retrieve the right card and enter the order on the hospital's materials management system (MMS). Most items were not cataloged, so a description had to be typed into the system each time.
Applying Lean Practices
In February of 2010 we held an open house to showcase our new facilities. Having completed a course in Lean Six Sigma a couple of years back and being keenly interested in Lean approaches, I decided to apply what I learned to organize the paper shelves and make it one of the attractions of the tour.
A major Lean tool is the 5S (or 6S) approach. IPG had a great article in the form of a Xerox advertorial (December 2009) that described 5S applied to an in-plant. We knew that we had to do some major sorting and straightening of our paper shelves. This would reduce the time wasted looking for supplies. But the other aspect was the process that we were currently using for ordering. Could we somehow dramatically reduce the waste there?
Ideally, a bar code system would be the way to go. The cost of such a system would have to be offset somehow by hard savings—not an easy thing to do. So, drawing from my Lean training, I started to devise a system that would be low-cost, very visual and easy to use.
First we sorted our paper and straightened our shelves. We divided the shelving units into sections, columns and rows, and labelled them accordingly. Next we decided which paper would go where, keeping in mind the proximity to the point of use. For almost every type of paper, we designated a primary and secondary location. If the paper was not in either location, then we were out of stock. In other words, no need to go hunting for paper all over the shop.
Then we designed a tag that had the MMS catalog number, a description of the paper including color and size, and the primary and secondary locations. We placed the laminated tags in plastic holders and applied them to the shelves.
How It Works
The way it works is as follows: When a staff member sees that an item is running low and there is no other stock in the secondary location, he/she pulls the tag from the plastic holder and hands it over to the coordinator. All the tags have a blue background. Beneath each tag is an identical one with a red background. When the employee removes the blue tag, the red tag indicates that the item has been given to the coordinator for ordering. This alerts other employees and puts their minds at ease.
The coordinator simply types the catalog number into the MMS system and orders an appropriate quantity. A record is kept on order cards, an old-fashioned but effective system that may eventually be replaced with an electronic one.
The total cost of implementing this system was less than $300, not including my time. The initial design was done by myself while another employee refined it, and then created all the tags, which were printed in color on a heavyweight paper and then laminated for durability.
Reaction to this system among staff has been positive. Stock-outs are rare, and paper is easily located. If you cannot justify an electronic system, this is definitely worth considering.
Related story: McGill Consolidates Two In-plants

Carmin Cristofaro is consultant in process improvement. He was previously in charge of the in-plant at McGill University Health Center in Montreal.
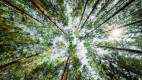


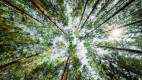
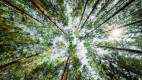
