Paper Inventory Management: A Lean Approach
Then we designed a tag that had the MMS catalog number, a description of the paper including color and size, and the primary and secondary locations. We placed the laminated tags in plastic holders and applied them to the shelves.
How It Works
The way it works is as follows: When a staff member sees that an item is running low and there is no other stock in the secondary location, he/she pulls the tag from the plastic holder and hands it over to the coordinator. All the tags have a blue background. Beneath each tag is an identical one with a red background. When the employee removes the blue tag, the red tag indicates that the item has been given to the coordinator for ordering. This alerts other employees and puts their minds at ease.

Carmin Cristofaro is consultant in process improvement. He was previously in charge of the in-plant at McGill University Health Center in Montreal.

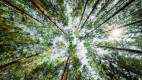


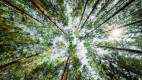
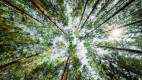