Paper Inventory Management: A Lean Approach
Ideally, a bar code system would be the way to go. The cost of such a system would have to be offset somehow by hard savings—not an easy thing to do. So, drawing from my Lean training, I started to devise a system that would be low-cost, very visual and easy to use.
First we sorted our paper and straightened our shelves. We divided the shelving units into sections, columns and rows, and labelled them accordingly. Next we decided which paper would go where, keeping in mind the proximity to the point of use. For almost every type of paper, we designated a primary and secondary location. If the paper was not in either location, then we were out of stock. In other words, no need to go hunting for paper all over the shop.

Carmin Cristofaro is consultant in process improvement. He was previously in charge of the in-plant at McGill University Health Center in Montreal.

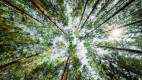


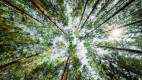
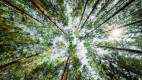