Digital copiers have changed the way in-plants operate. Find out how paper companies have improved their products as a result.
Over the past several years, as in-plants have swapped their analog and offset dancing partners of old for the fancy new moves of digital copiers, paper producers and equipment manufacturers have been involved in an elaborate pas de deux of their own.
After all, when digital copiers first hit the dance floor, they found few partners waiting and could do little more than watch the older, more experienced machines hog the limelight.
"Originally, the first digital presses required special paper, but the market wasn't big enough and people had a very difficult time finding what they needed," says Peter Harding, vice president of business papers at Weyerhaeuser.
Dissatisfied with their role as wallflowers, the original equipment manufacturers, or OEMs, returned to dance school to start again.
"The manufacturers worked to conform their equipment to the paper that was available versus having the [paper] manufacturers try to figure out how to come up with a whole line of paper that would work specifically for these presses," says Harding. "Now you're better able to get what you need to run on these presses."
Changing Partners
"The printers are changing more for the paper than the paper is changing for the printers," says Kyle Prince, Stora Enso's North American product manager for digital papers. "The machines themselves are becoming more forgiving. The OEMs are having to adapt to customers wanting to be able to use the paper that they've always used. The customers want a printer that can run off-the-shelf paper so they don't have to buy a specialty paper."
This isn't to say that the paper manufacturers haven't had to learn a few new moves of their own.
"The speed, the pressure, the heat—all of the technology that's involved with this [new] equipment has changed what type of products you can run through them," says Aaron Godnai, marketing manager for Meadware, Mead Paper's line of digital printing products.
Kyle Prince agrees. "More and more is being asked of the paper by the printers. They're running faster and have better resolution, so as the printers get better, the paper must get better."
And get better it has. Godnai, for example, says that for Mead's new Accelerator line—intended for use on high-speed color equipment—the company worked hard to develop a gloss sheet with the proper moisture and surface characteristics.
"The biggest characteristic we've found," says Godnai, "is that [the paper] has to have the correct moisture content; otherwise, when the paper hits the infuser, the heat will burn the moisture out of the paper and not allow for proper toner adhesion."
In addition to keeping up with the moves by digital copiers, paper manufacturers have simultaneously had to learn new steps to match the changing needs of the end user.
"The market is requesting brighter and whiter [paper], and in some cases smoother, depending on the applications," notes Stora Enso's Prince, in a statement echoed by nearly all of the paper companies contacted.
Says Ned Spangler, brand manager for Hammermill's imaging papers, "We are seeing very strong growth in color imaging, which typically requires paper with higher brightness levels, smoother surfaces and heavier basis weights."
Printers are also migrating from uncoated bond-type paper, once a copier staple, into high-speed coated papers, largely to accommodate increasing volumes of color work.
"Customers are now looking for a solution on a coated sheet [for digital copiers] that will compare with traditional offset presses," says Godnai.
Harding says the biggest change he's seen at Weyerhaeuser isn't with the content of the paper so much as how it's being delivered.
"Fundamentally, the paper isn't all that different," he says. "Most of [what's new] is really a size statement. Traditionally, offset presses need larger sizes with bigger runs; now with these digital presses, you can have smaller runs, and by virtue of that, smaller sheet sizes." Paper company representatives say customers are flooding them with requests for cut sizes of 81⁄2x11˝, 11x17˝ and 12x18˝.
New Moves For The Future
As paper companies learned to dance in step with the new digital copiers, they imagined a future in which the distinction of which paper goes where isn't so important.
"In the move from traditional offset printing to digital, what we've done is enhance the sheet so it has a dual purpose application that allows it to run across all these machines versus just one or the other," notes Harding. "Our products will be more interchangeable with the technology, and I think the manufacturers have created equipment that allows that to happen."
Mohawk Paper has been working along similar lines, says Christopher Harrold, manager of national accounts and business development.
"The strategy at Mohawk now, in terms of our digital papers, is clearly a cross-platform printing strategy so that the same papers that have traditionally performed on offset presses can now be wed up with jobs on something as common as a Canon CLC device. The paper will have the same visual and tactile attributes as its cousin that would be run on an offset press. We want it transparent."
It almost goes without saying that the new digital papers will still work on the analog copiers of old—if any survive.
"If someone were to buy a ream of Navajo or Mohawk Satin and put it through a traditional platen copier, I'm sure it would work fine," says Harrold.
More Weight On The Way
Harrold, Godnai and Spangler all predict that heavier stocks will become more widespread in the future.
"Down the road, the biggest change, as the technology continues to evolve, will allow for heavier weight stock, heavier weight coated papers, eight-, 10-, 12-point C1Ss, reply cards," predicts Mead's Godnai. "The substrates that they'll be able to run on this equipment [are] going to grow exponentially, and that's a huge selling point for the OEM to the customer. That's going to bring this type of equipment into more direct competition with offset presses."
No matter what the weight of the sheet is, be sure to treat your paper well. Thanks to the complicated dances of the paper and equipment manufacturers, what you're working with should serve you well for a mighty long time.
-by W. Eric Martin
Sidebar: Treat Your Sheets Well Proper paper storage is essential for optimum performance. "You want the paper stored as near to the press as possible, preferably in the same humidity-controlled rooms where you're running the equipment," says Aaron Godnai, marketing manager for Mead Paper's digital printing products. He stresses that proper moisture content is the key. "If you have a shop in Miami and store the paper in a 95-degree, 90 percent humidity storeroom and then bring the paper into the 75-degree, 50 humidity room that holds the presses, it's not going to work. You want a real stable sheet." To achieve that stability, adds Hammermill's Ned Spangler, you should first try to store the paper in its original packaging. Doing so should reduce the amount of moisture added to or subtracted from the sheet. Second, he says, if you can't store the paper in a climate-controlled location, bring the paper into such a location approximately 48 hours before you intend to use it so the paper can acclimatize itself to the environment. -by W. Eric Martin
|
- Companies:
- Canon U.S.A.
- NewPage Corp.
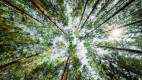


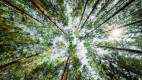
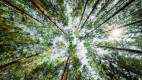
