Both imagesetters and platesetters have advantages, but many vendors feel CTP is the way to go.
By Mike Llewellyn
IMAGESETTERS STILL have a home in the in-plant world, but among manufacturers these days, they just aren't that popular.
With their ears to the ground, most major manufacturers of imagesetters expect interest in the technology is about to run its course, particularly with advent of violet laser computer-to-plate (CTP) technology.
The equipment is still selling, they point out—albeit slowly. But overall, according to Ken Hanulec, director of marketing for Creo Americas, most in-plant managers would be better off investing in computer-to-plate systems rather than getting their shops' feet wet in the digital sea with an imagesetter.
Hanulec says when in-plants do purchase a Creo imagesetter, they tend to do so because the machines cost significantly less and because they can be modified to take on other tasks within the shop aside from producing film. For instance, Hanulec explains, with a small change in the calibration of the exposure system, some imagesetters can be modified to image directly onto polyester or paper plates, turning the imagesetter into a makeshift platesetter.
Additionally, he notes that there are a handful of in-plants that sell film as part of their business model. These in-plants, says Hanulec, would benefit greatly from updating or purchasing an imagesetter. But most imagesetters sold by the company, he adds, are bought by firms outside the United States in countries with inexpensive labor costs.
Dave Carey, product marketing manager for Agfa's computer-to-film division, says imagesetters are still finding homes for one major reason: Price.
"Imagesetters can handle a variety of tasks," he says, "and although they can cost as much as $74,000, you can also get one for as little as $14,000."
According to Carey, imagesetters are one way for wary in-plant managers to take their shop into the digital arena. Used equipment is very inexpensive, he adds, and for a high-productivity shop, it just doesn't make sense to entirely avoid going digital.
CTP The Way To Go
Still, many vendors, like Creo, are pushing CTP over imagesetters. Creo's Hanulec says the issue for in-plant managers should no longer be whether to go with an imagesetter or a platesetter, but which platesetter manufacturer would best suit the in-plant's needs. And in-plant managers would be wise to keep their eyes open for much more than low cost, he adds. Introducing digital technology is a project that requires a great deal of research on the part of the buyer, he points out.
"The most successful [in-plants] view the project as a whole and never consider just a single component in their decision-making process," he says. "Smart [in-plants] consider the technology, the overall stability of the vendor, the support infrastructure and the financing arrangements."
Phasing Out The Film
Creo is not alone in its migration away from direct-to-film technology. Mark Tonkovich is Heidelberg USA's CTP product manager, and he says that while Heidelberg still has imagesetters in its portfolio, due to a lingering demand for the equipment, the company plans to phase out the line in the coming years.
When Heidelberg released PrimeSetter, its flagship line of imagesetters, at the last Drupa show, the company already had the future primacy of CTP in mind, says Tonkovich. The base design of the PrimeSetter was used in the manufacture of the ProSetter series—one of Heidelberg's platesetter lines.
"Because polyester-plate CTP—and now metal plates with violet CTP—have been bringing down the cost of going direct-to-plate, computer to plate is better suited to meet the needs of most in-plant managers," he says.
In Tonkovich's estimation, in-plant managers opting to go with an imagesetter instead of a platesetter are doing so most likely because they have not done in-house imaging before and they feel an imagesetter would be less wasteful than a platesetter.
"However, the two workflows are identical whether imaging film or plates," he notes.
Exceptions To The Rule
But there are some in-plants that would do very well to purchase an imagesetter. According to Joe Blauer, national sales manager for quick prepress solutions at Esko-Graphics, in-plants with no offset equipment should invest in an imagesetter. If a shop has to outsource all of its press jobs, an imagesetter would allow the in-plant to ensure a quality product, as well as give it the leverage to select the type of press to produce the job.
Aiding The Proofing Process
In-plants should also consider an imagesetter if they consistently need to present high-quality proofs to their clients.
"If there is somebody that needs a proof with the same dot structure as the plate is going to have, they would still be able to get a traditional analog-style proof from an imagesetter," says Blauer, since the same film is used to image both the proof and the plate.
This is one of the reasons Gregg Gabbana cites for deciding to purchase an imagesetter in June of 2000 for the UNISYS Print Replication and On Demand Manufacturing department, in Plymouth, Mich.
"We could use the imagesetter and its films to create both the proof and the plate," he points out.
CTP Cost Dropping Mark Tonkovich, product manager for computer-to-plate systems at Heidelberg USA, recommends in-plant managers keep their eyes on platesetters because considerable technological advances are making the equipment as inexpensive as imagesetters. "Polyester CTP is already within the price range of imagesetters," he notes. Meanwhile, violet laser platesetters, used to image metal plates, have surpassed their thermal counterparts when it comes to price. Tonkovich says thermal platesetters use hardware-heavy external drum technology to rotate the drum (to which the plate is fixed) at speeds reaching 1,000 rpm. The internal drum technology used in violet platesetters, on the other hand, does not require this level of mechanical operation and is therefore less expensive to manufacture. Additionally, the lasers themselves often differ widely in price, violet lasers being the less expensive of the two. (Violet lasers boast a longer life cycle, as well.) Combined with the lower cost of the internal drum technology, the less expensive violet laser assembly allows Heidelberg to lower the cost of metal CTP systems to its customers. |
The 71-employee in-plant uses a Screen Katana imagesetter and an Imation Matchprint proofer. Gabbana says the imagesetter produces high-quality films, allowing the operation to print some eye-catching pieces on its three two-color presses.
"We're running everything at 175 line screen," he notes—and sometimes as high as 200 line screen. "We're very happy with it. The reliability of it is fantastic."
Still, he acknowledges that if the in-plant ever gets a four-color press, it will likely also get a platesetter to save on labor and consumables costs.
Shopping For 'Setters
When an in-plant manager is on the market for an imagesetter, it's important to keep a number of factors in mind. First, says Blauer, of Esko-Graphics, it's essential that in-plants purchase the imagesetter and the workflow software together as part of the same package.
"It's good to get the complete system—especially in an in-plant environment with tight deadlines," he says. Acquiring the complete system assures a hassle-free process all the way to the completion of a job, he contends.
Additionally, Blauer reminds in-plant managers of the importance of seeking out internal drum technology in imagesetters, as well as in platesetters. This technology keeps the film fixed in place with no risk of it shifting during the imaging process. The smallest movement, he says, and the film will be inaccurate and will have to be scrapped.
In the end, though, if an in-plant has a choice between an imagesetter and a platesetter, most of the time CTP will be the best bet.
"If an in-plant has its own presses, and it's able to go with digital plates," he says, "then CTP is the best way to go."
Find Out More
Agfa
|
www.agfa.com
|
alfaQuest Technologies
|
www.alfaquest.com
|
Creo
|
www.creo.com
|
ECRM Imaging Systems
|
www.ecrm.com
|
Escher-Grad Technologies
|
www.escher-grad.com
|
Esko-Graphics
|
www.esko-graphics.com
|
Fuji Photo Film USA
|
www.fujifilm.com
|
Heidelberg USA
|
www.heidelberg.com
|
Kodak Polychrome Graphics
|
www.kpgraphics.com
|
RIPit Computer
|
www.ripit.com
|
Screen (U.S.A.)
|
www.screenusa.com
|
Xanté
|
www.xante.com
|
Xitron
|
www.xitron.com
|
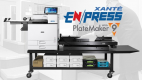




